Physical Vapor Deposition (PVD) and Chemical Vapor Deposition (CVD) are two prominent surface coating methods used in various industries. While both techniques aim to deposit thin films onto substrates, they differ significantly in their processes, operational conditions, and outcomes. PVD involves the physical vaporization of materials and their subsequent deposition onto a substrate, typically in a vacuum environment. This method is known for its lower deposition temperatures and absence of corrosive by-products. CVD, on the other hand, relies on chemical reactions between gaseous precursors and the substrate to form a solid coating, often requiring high temperatures and potentially producing corrosive gaseous products. The choice between PVD and CVD depends on the specific application requirements, including the desired film properties, substrate material, and operational constraints.
Key Points Explained:
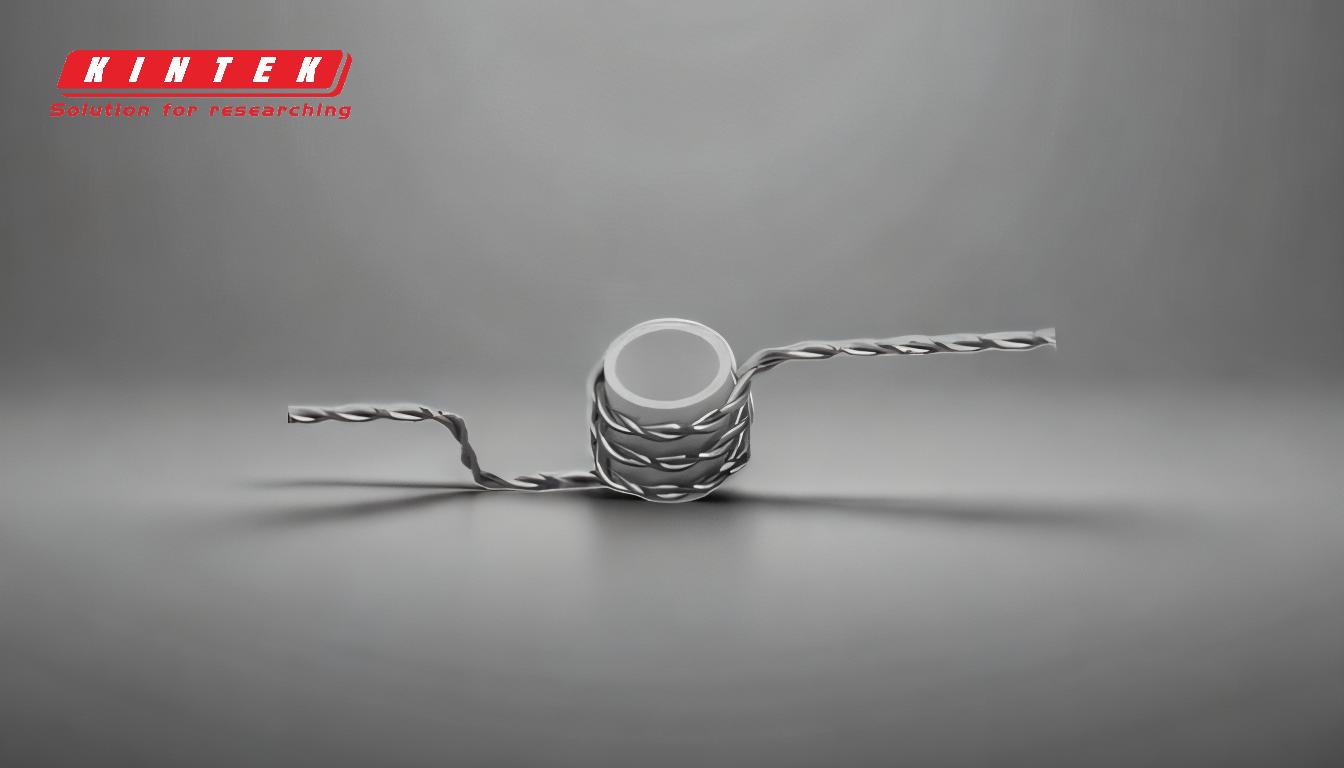
-
Process Mechanism:
- PVD: Involves the physical vaporization of materials through processes like sputtering or evaporation. The vaporized material then condenses onto the substrate, forming a thin film. This is a line-of-sight process, meaning the material is deposited directly onto the substrate without chemical interaction.
- CVD: Relies on chemical reactions between gaseous precursors and the substrate surface. The gaseous reactants decompose or react at the substrate surface to form a solid coating. This is a multidirectional process, allowing for uniform coating on complex geometries.
-
Deposition Temperature:
- PVD: Typically carried out at lower temperatures, which is beneficial for substrates that cannot withstand high thermal stress. This makes PVD suitable for temperature-sensitive materials.
- CVD: Generally requires high temperatures, often in the range of 500°–1100°C. The high temperatures can lead to the formation of corrosive by-products and may leave impurities in the film.
-
Deposition Rate and Efficiency:
- PVD: Generally has lower deposition rates compared to CVD. However, certain PVD techniques like Electron Beam Physical Vapor Deposition (EBPVD) can achieve high deposition rates (0.1 to 100 μm/min) at relatively low substrate temperatures, with very high material utilization efficiency.
- CVD: Typically offers higher deposition rates, but the process can be slower due to the need for precise control of chemical reactions and gas flow.
-
Material Compatibility:
- PVD: Can deposit a wide range of materials, including metals, alloys, and ceramics. This versatility makes PVD suitable for various applications, from decorative coatings to functional layers.
- CVD: Primarily used for depositing ceramics and polymers. The chemical nature of the process limits the types of materials that can be effectively deposited.
-
Film Properties:
- PVD Coatings: Tend to be less dense and less uniform compared to CVD coatings. However, PVD coatings are faster to apply and can offer better corrosion resistance, making them ideal for applications where durability is critical.
- CVD Coatings: Generally denser and more uniform, providing excellent coverage even on complex geometries. The high-temperature process can result in films with superior mechanical and thermal properties.
-
Corrosion and Impurities:
- PVD: Does not produce corrosive by-products, making it more suitable for applications where corrosion resistance is essential. The absence of chemical reactions also reduces the risk of impurities in the film.
- CVD: The high-temperature process can lead to the formation of corrosive gaseous products, which may leave impurities in the film. This can be a drawback in applications requiring high purity.
-
Applications:
- PVD: Commonly used in industries requiring durable, corrosion-resistant coatings, such as automotive, aerospace, and tool manufacturing. It is also used for decorative coatings and in the electronics industry.
- CVD: Widely used in the semiconductor industry for depositing thin films of silicon, silicon dioxide, and other materials. It is also used in the production of wear-resistant coatings and in the fabrication of optical components.
In summary, the choice between PVD and CVD depends on the specific requirements of the application, including the desired film properties, substrate material, and operational constraints. PVD offers advantages in terms of lower deposition temperatures, absence of corrosive by-products, and versatility in material deposition. CVD, on the other hand, provides higher deposition rates, denser and more uniform coatings, and is particularly suited for high-temperature applications and complex geometries.
Summary Table:
Aspect | PVD | CVD |
---|---|---|
Process Mechanism | Physical vaporization (e.g., sputtering, evaporation) | Chemical reactions between gaseous precursors and substrate |
Deposition Temperature | Lower temperatures, suitable for sensitive materials | High temperatures (500°–1100°C), may produce corrosive by-products |
Deposition Rate | Lower rates, but high efficiency in techniques like EBPVD | Higher rates, but slower due to precise control of reactions |
Material Compatibility | Metals, alloys, ceramics | Primarily ceramics and polymers |
Film Properties | Less dense, less uniform, but faster and corrosion-resistant | Denser, more uniform, superior mechanical and thermal properties |
Corrosion & Impurities | No corrosive by-products, fewer impurities | Corrosive by-products, potential impurities |
Applications | Automotive, aerospace, tool manufacturing, electronics, decorative | Semiconductor industry, wear-resistant coatings, optical components |
Need help choosing between PVD and CVD for your project? Contact our experts today!