PVD (Physical Vapor Deposition) coating and plating (such as electroplating) are two distinct surface treatment methods used to enhance the durability, appearance, and functionality of materials. While both processes aim to protect and improve the surface of substrates, they differ significantly in their mechanisms, materials, environmental impact, and applications. PVD coating involves depositing thin films of materials in a vacuum environment, resulting in highly durable, corrosion-resistant, and environmentally friendly coatings. In contrast, electroplating relies on chemical reactions to deposit thicker layers of metal, often requiring additional clear coats that can degrade over time. PVD coatings are more versatile, eco-friendly, and suitable for high-performance applications, whereas plating is more traditional and cost-effective for certain uses.
Key Points Explained:
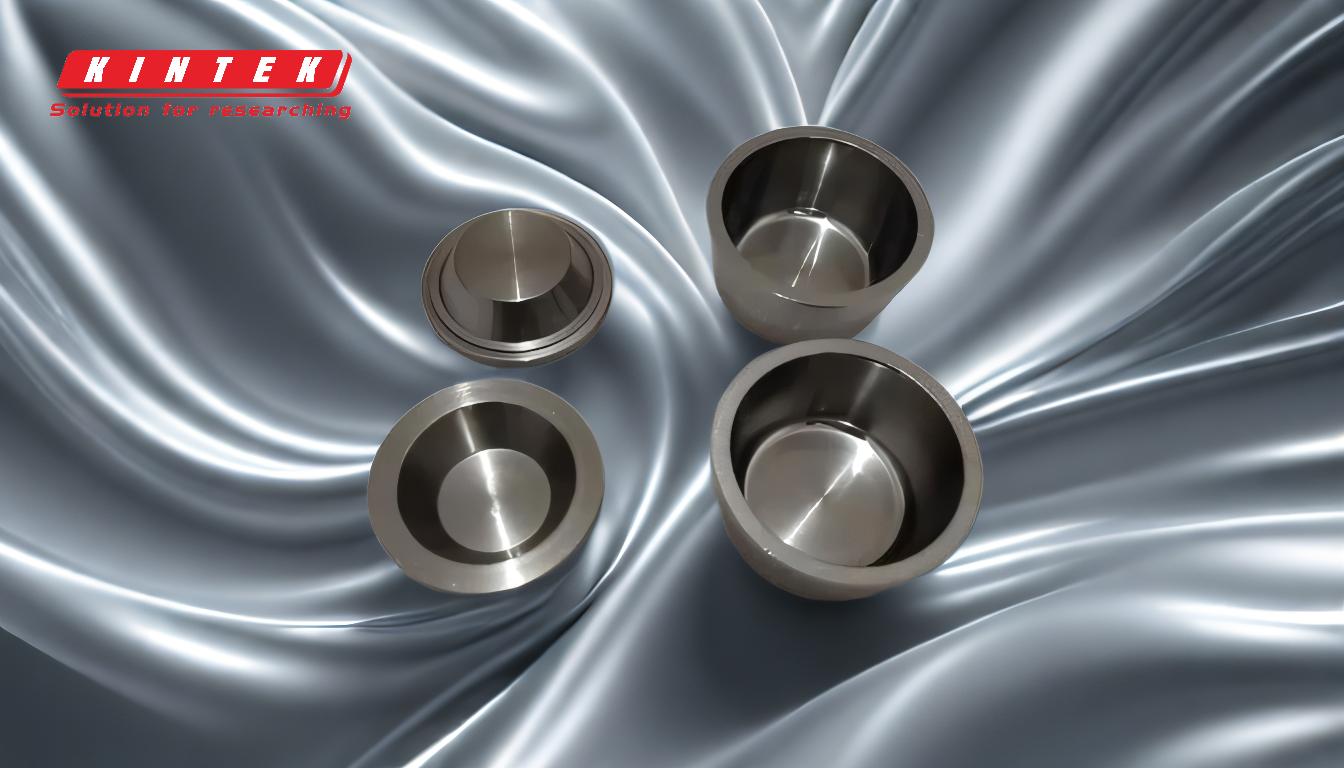
-
Process Mechanism:
-
PVD Coating:
- Occurs in a vacuum environment at high temperatures.
- Uses physical processes like sputtering or evaporation to deposit thin films of metals, alloys, or ceramics onto the substrate.
- Results in a thin, uniform layer that bonds strongly with the substrate.
-
Plating (Electroplating):
- Involves chemical reactions in an electrolyte solution.
- Uses electrical currents to deposit metal ions onto the substrate.
- Produces thicker layers, often requiring additional clear coats for protection.
-
PVD Coating:
-
Material Versatility:
-
PVD Coating:
- Can deposit a wide range of materials, including metals, alloys, and ceramics.
- Suitable for creating specialized coatings with unique properties (e.g., hardness, wear resistance).
-
Plating:
- Primarily limited to metals like brass, nickel, and gold.
- Less versatile in terms of material options compared to PVD.
-
PVD Coating:
-
Durability and Performance:
-
PVD Coating:
- Highly durable, resistant to fading, tarnishing, and corrosion.
- Does not require clear top coats, making it more robust over time.
- Superior wear resistance and ruggedness, ideal for high-performance applications.
-
Plating:
- Requires clear coats that can degrade, leading to tarnishing or corrosion.
- Less durable compared to PVD coatings, especially in harsh environments.
-
PVD Coating:
-
Environmental Impact:
-
PVD Coating:
- Environmentally friendly, as it does not release harmful chemicals into the atmosphere.
- Produces no toxic substances, making it a sustainable choice.
-
Plating:
- Often involves the use of hazardous chemicals, which can harm the environment.
- Generates waste that requires careful disposal.
-
PVD Coating:
-
Applications:
-
PVD Coating:
- Widely used in industries like aerospace, medical, and high-tech due to its durability and performance.
- Suitable for marine environments due to resistance to saltwater and UV exposure.
-
Plating:
- Commonly used for decorative purposes (e.g., jewelry, automotive trim).
- Cost-effective for applications where extreme durability is not required.
-
PVD Coating:
-
Thickness and Uniformity:
-
PVD Coating:
- Produces thin, uniform layers (also known as Thin Film Deposition).
- Less dense but faster to apply compared to CVD (Chemical Vapor Deposition).
-
Plating:
- Results in thicker, less uniform layers.
- May require additional finishing steps to achieve desired uniformity.
-
PVD Coating:
-
Cost and Maintenance:
-
PVD Coating:
- Higher initial cost but reduces long-term maintenance due to its durability.
- Increases product longevity, making it cost-effective over time.
-
Plating:
- Lower initial cost but may incur higher maintenance expenses due to degradation over time.
-
PVD Coating:
In summary, PVD coating offers superior durability, environmental safety, and material versatility, making it ideal for high-performance and specialized applications. Plating, while more traditional and cost-effective, is better suited for decorative or less demanding uses. The choice between the two depends on the specific requirements of the application, including durability, environmental impact, and budget considerations.
Summary Table:
Aspect | PVD Coating | Plating (Electroplating) |
---|---|---|
Process Mechanism | Vacuum environment, sputtering/evaporation, thin uniform layers | Chemical reactions in electrolyte, thicker layers, requires clear coats |
Material Versatility | Metals, alloys, ceramics | Primarily metals (e.g., brass, nickel, gold) |
Durability | Highly durable, corrosion-resistant, no clear coats needed | Less durable, clear coats degrade over time |
Environmental Impact | Eco-friendly, no harmful chemicals | Uses hazardous chemicals, generates waste |
Applications | Aerospace, medical, high-tech, marine environments | Decorative (e.g., jewelry, automotive trim) |
Thickness & Uniformity | Thin, uniform layers | Thicker, less uniform layers |
Cost & Maintenance | Higher initial cost, lower long-term maintenance | Lower initial cost, higher maintenance over time |
Unsure which surface treatment is best for your needs? Contact our experts today for personalized advice!