Refining and calcination are two distinct processes used in material processing, each serving different purposes. Refining generally involves purifying a material to remove impurities and improve its quality, often through physical or chemical methods. Calcination, on the other hand, is a thermal treatment process where materials are heated to high temperatures in the absence or limited supply of air, leading to decomposition, phase transition, or removal of volatile substances. While refining focuses on purification, calcination is primarily about thermal decomposition or transformation. Below, the key differences and applications of these processes are explained in detail.
Key Points Explained:
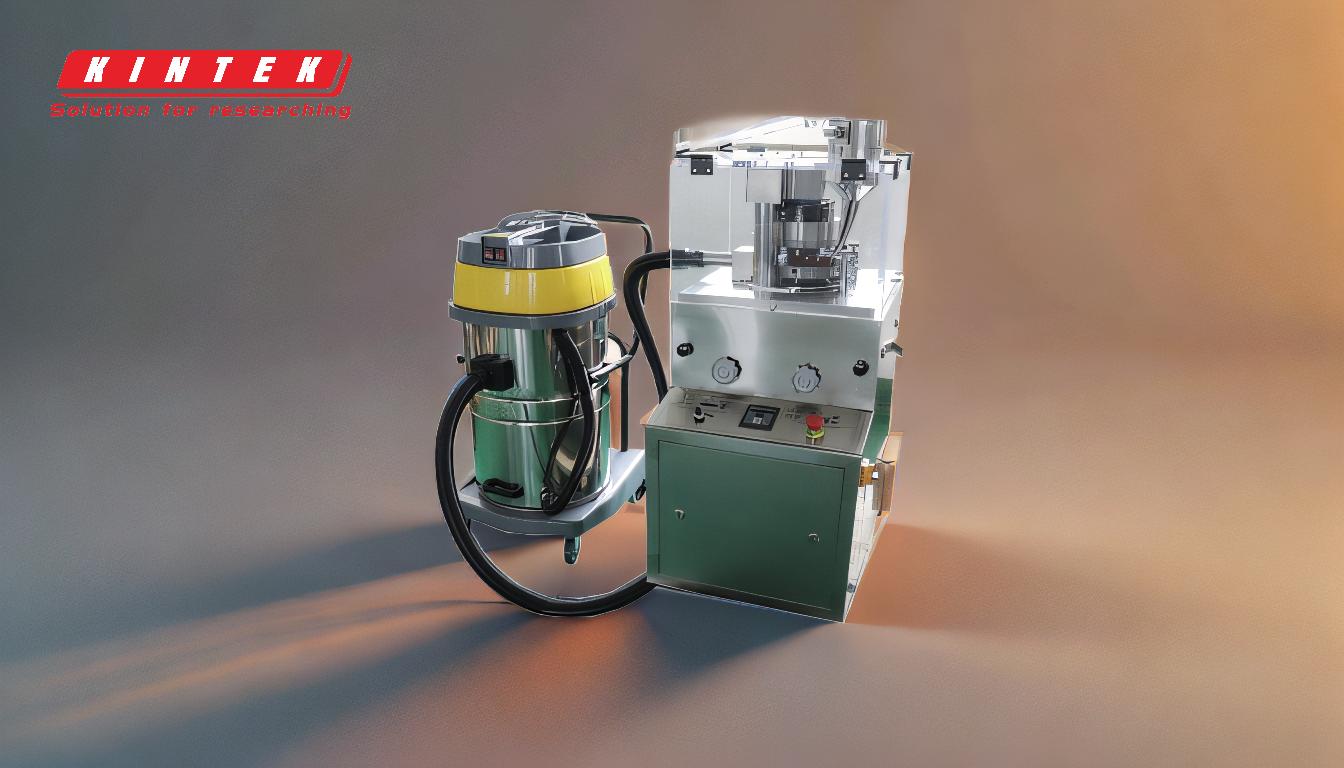
-
Definition and Purpose:
-
Refining:
- Refining is the process of purifying a material to remove impurities or unwanted elements, enhancing its quality or usability. It is commonly used in industries like metallurgy, oil, and chemicals.
- Example: Refining crude oil to produce usable petroleum products like gasoline or diesel.
-
Calcination:
- Calcination involves heating a material to high temperatures (typically below its melting point) in the absence or limited supply of air. This process is used to decompose, oxidize, or remove volatile components.
- Example: Heating limestone (CaCO₃) to produce lime (CaO) and carbon dioxide (CO₂).
-
Refining:
-
Temperature and Environment:
-
Refining:
- Refining processes often occur at varying temperatures depending on the material and method used. For example, refining metals may involve melting at high temperatures, while refining oil involves distillation at controlled temperatures.
- The environment can be open or controlled, depending on the process.
-
Calcination:
- Calcination typically requires high temperatures, often between 500°C to 1200°C, depending on the material.
- The process is carried out in the absence or limited supply of air to prevent combustion or oxidation of the material.
-
Refining:
-
Chemical and Physical Changes:
-
Refining:
- Refining focuses on physical separation (e.g., filtration, distillation) or chemical reactions (e.g., electrolysis) to remove impurities.
- The goal is to isolate the desired material in its pure form.
-
Calcination:
- Calcination induces chemical changes such as decomposition, phase transitions, or removal of volatile substances (e.g., water, carbon dioxide).
- The process often results in a change in the chemical composition of the material.
-
Refining:
-
Applications:
-
Refining:
- Widely used in metallurgy (e.g., refining gold, silver, copper), oil refining, and chemical industries.
- Essential for producing high-purity materials for industrial or commercial use.
-
Calcination:
- Used in the production of cement, lime, ceramics, and certain metals (e.g., aluminum oxide from bauxite).
- Also employed in the preparation of catalysts and adsorbents.
-
Refining:
-
Equipment Used:
-
Refining:
- Equipment varies widely depending on the material and process. Examples include distillation columns, electrolytic cells, and furnaces.
-
Calcination:
- Typically performed in calcination furnaces, rotary kilns, or muffle furnaces designed to withstand high temperatures and control the atmosphere.
-
Refining:
-
Outcome:
-
Refining:
- Results in a purified material with improved properties, such as higher conductivity, purity, or usability.
-
Calcination:
- Produces a material with altered chemical composition, often in a more stable or usable form (e.g., lime from limestone).
-
Refining:
In summary, refining and calcination are both critical processes in material science and industrial applications, but they serve different purposes and involve distinct methods. Refining focuses on purification, while calcination is centered on thermal decomposition or transformation. Understanding these differences is essential for selecting the appropriate process for a given material or application.
Summary Table:
Aspect | Refining | Calcination |
---|---|---|
Purpose | Purification to remove impurities and improve material quality. | Thermal decomposition or transformation of materials. |
Temperature | Varies; can involve melting or controlled heating. | High temperatures (500°C–1200°C) in limited air supply. |
Chemical Changes | Focuses on physical separation or chemical reactions to isolate pure material. | Induces decomposition, phase transitions, or removal of volatile substances. |
Applications | Metallurgy, oil refining, chemical industries. | Cement, lime, ceramics, catalyst preparation. |
Equipment | Distillation columns, electrolytic cells, furnaces. | Calcination furnaces, rotary kilns, muffle furnaces. |
Outcome | Purified material with improved properties. | Altered chemical composition, often in a more stable or usable form. |
Need help choosing the right process for your material? Contact our experts today!