Resistance furnaces and induction furnaces are both used for heating materials, but they operate on fundamentally different principles. Resistance furnaces use electrical resistance to generate heat, which is then transferred to the material through conduction, convection, or radiation. Induction furnaces, on the other hand, use electromagnetic induction to generate heat directly within the material itself. This key difference leads to variations in efficiency, heating speed, control, and applications. Resistance furnaces are generally simpler and more cost-effective for steady-state heating, while induction furnaces offer faster heating, better energy efficiency, and precise temperature control, making them ideal for applications requiring rapid or localized heating.
Key Points Explained:
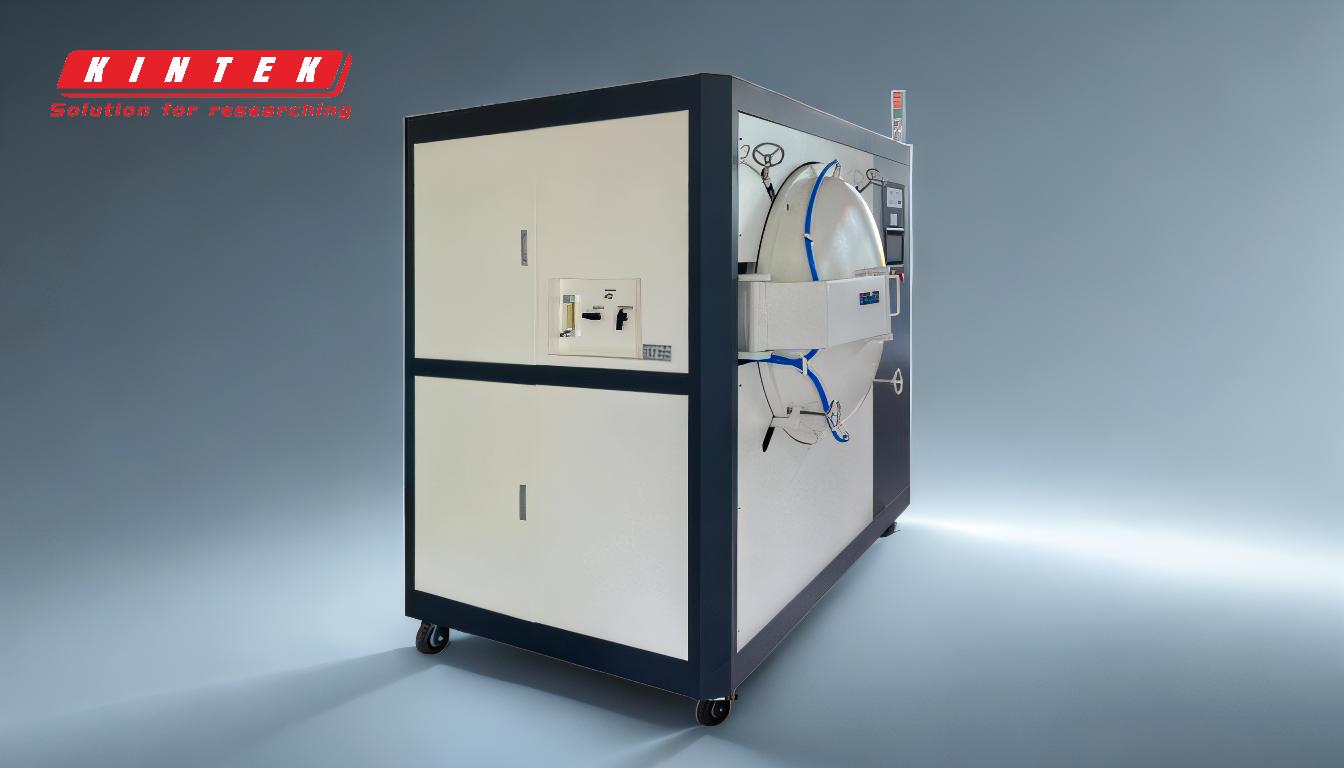
-
Heating Mechanism:
- Resistance Furnace: Heat is generated by passing an electric current through a resistive element, such as a coil or heating wire. The heat is then transferred to the material through conduction, convection, or radiation. This method is indirect, as the material is heated by an external source.
- Induction Furnace: Heat is generated directly within the material using electromagnetic induction. An alternating current passes through a coil, creating a magnetic field that induces eddy currents in the material, causing it to heat up. This method is direct and highly efficient.
-
Energy Efficiency:
- Resistance Furnace: Less energy-efficient compared to induction furnaces because heat is generated externally and then transferred to the material, leading to energy losses.
- Induction Furnace: More energy-efficient as heat is generated directly within the material, minimizing energy losses. This is particularly beneficial for high-temperature applications.
-
Heating Speed and Control:
- Resistance Furnace: Slower heating rates and less precise temperature control. Suitable for applications where steady-state heating is required.
- Induction Furnace: Faster heating rates and precise temperature control, making it ideal for processes requiring rapid or localized heating. The use of IGBT induction furnace technology further enhances control and efficiency.
-
Applications:
- Resistance Furnace: Commonly used in applications like annealing, tempering, and drying, where uniform heating over a large area is needed.
- Induction Furnace: Used in applications like melting, forging, and surface hardening, where rapid, localized, or high-temperature heating is required.
-
Cost and Complexity:
- Resistance Furnace: Generally simpler in design and more cost-effective for basic heating applications. Maintenance is straightforward.
- Induction Furnace: More complex and expensive due to the need for advanced components like induction coils and power supplies. However, the higher initial cost is often offset by energy savings and improved performance.
-
Material Compatibility:
- Resistance Furnace: Can handle a wide range of materials, including metals, ceramics, and glass. However, it may not be suitable for materials that require rapid or localized heating.
- Induction Furnace: Primarily used for conductive materials like metals. Non-conductive materials cannot be heated using induction.
-
Environmental Impact:
- Resistance Furnace: Higher energy consumption and heat loss can lead to a larger environmental footprint.
- Induction Furnace: Lower energy consumption and reduced heat loss make it a more environmentally friendly option.
By understanding these key differences, purchasers can make informed decisions based on their specific heating requirements, material types, and operational goals.
Summary Table:
Aspect | Resistance Furnace | Induction Furnace |
---|---|---|
Heating Mechanism | Indirect heating via electrical resistance (conduction, convection, or radiation). | Direct heating via electromagnetic induction within the material. |
Energy Efficiency | Less efficient due to external heat generation and transfer losses. | More efficient as heat is generated directly within the material. |
Heating Speed/Control | Slower heating, less precise control; ideal for steady-state heating. | Faster heating, precise control; ideal for rapid or localized heating. |
Applications | Annealing, tempering, drying (uniform heating over large areas). | Melting, forging, surface hardening (rapid or localized heating). |
Cost & Complexity | Simpler design, cost-effective for basic heating; straightforward maintenance. | More complex, higher initial cost; offset by energy savings and improved performance. |
Material Compatibility | Wide range (metals, ceramics, glass); not ideal for rapid/localized heating. | Primarily conductive materials (metals); non-conductive materials cannot be heated. |
Environmental Impact | Higher energy consumption and heat loss; larger environmental footprint. | Lower energy consumption, reduced heat loss; more environmentally friendly. |
Need help choosing the right furnace for your application? Contact our experts today for personalized advice!