RF and DC magnetron sputtering are two widely used physical vapor deposition (PVD) techniques, each with distinct characteristics and applications. The primary differences lie in their power sources, material compatibility, deposition rates, and operational requirements. RF magnetron sputtering uses an alternating current (AC) power source, typically at 13.56 MHz, making it suitable for both conductive and non-conductive materials. It operates at lower pressures and involves a two-cycle polarization process, but it has a lower deposition rate and higher cost. In contrast, DC magnetron sputtering uses a direct current (DC) power source, is limited to conductive materials, and offers higher deposition rates and cost-efficiency for large substrates. Both techniques utilize magnetic fields to enhance plasma confinement and deposition efficiency, but their operational mechanisms and material compatibility set them apart.
Key Points Explained:
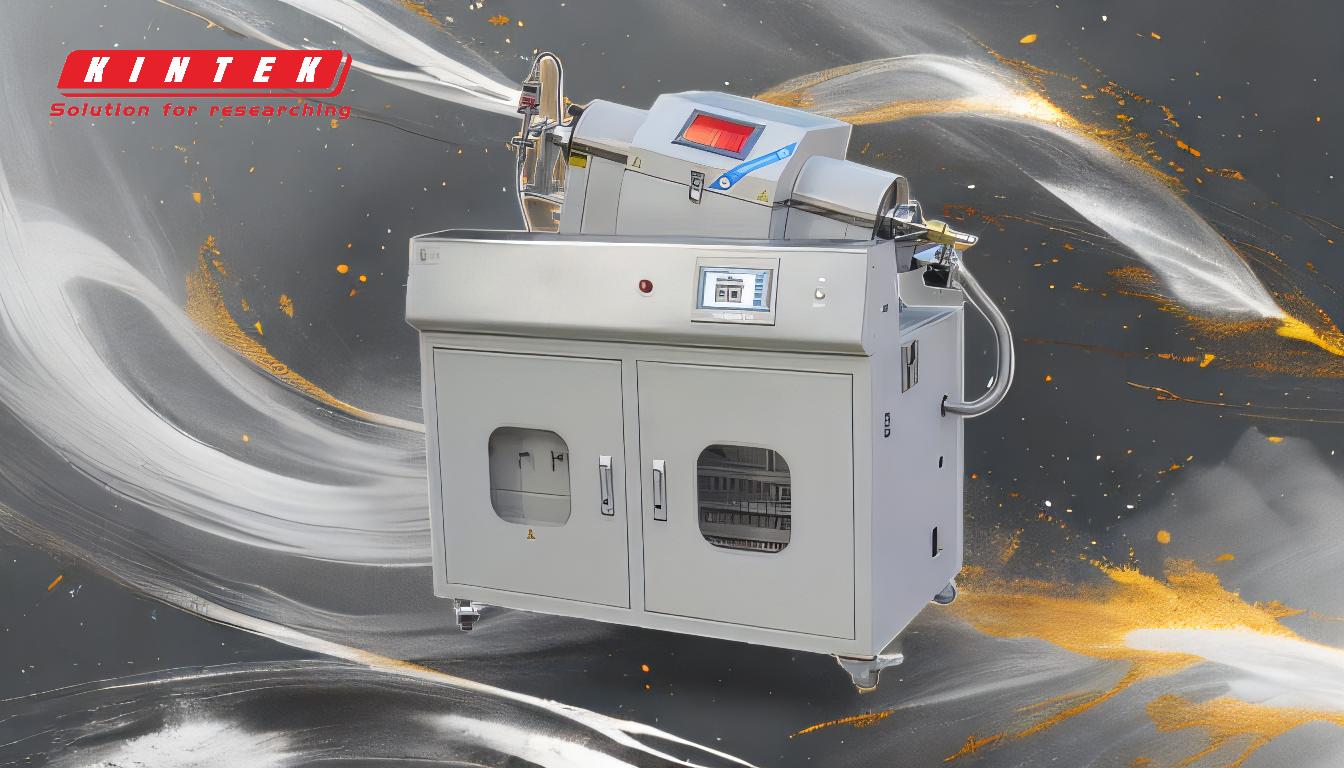
-
Power Source and Material Compatibility:
- DC Magnetron Sputtering: Uses a direct current (DC) power source and is primarily suited for conductive materials such as pure metals (e.g., Iron, Copper, Nickel). It cannot effectively sputter non-conductive or dielectric materials due to charge accumulation and arcing issues.
- RF Magnetron Sputtering: Uses an alternating current (AC) power source, typically at 13.56 MHz. This alternating charge prevents charge buildup on the target, making it suitable for both conductive and non-conductive materials, including dielectrics.
-
Deposition Rate and Cost:
- DC Magnetron Sputtering: Offers high deposition rates, making it ideal for large-scale production and cost-efficient for large substrates. The operational costs are generally lower compared to RF sputtering.
- RF Magnetron Sputtering: Has a lower deposition rate due to the alternating charge process, which reduces the efficiency of material ejection. This, combined with higher equipment and operational costs, makes it more suitable for smaller substrates or specialized applications.
-
Operational Pressure:
- DC Magnetron Sputtering: Typically operates at higher chamber pressures, ranging from 1 to 100 mTorr. Maintaining these pressures can be more challenging but is necessary for efficient sputtering of conductive materials.
- RF Magnetron Sputtering: Operates at lower pressures due to the high percentage of ionized particles in the vacuum chamber. This lower pressure environment enhances the sputtering process for both conductive and non-conductive materials.
-
Mechanism of Sputtering:
- DC Magnetron Sputtering: Involves the acceleration of positively charged gas ions toward the target material, causing atoms to be ejected and deposited onto the substrate. The process is straightforward and efficient for conductive targets.
- RF Magnetron Sputtering: Operates through a two-cycle process of polarization and reverse polarization. This alternating charge mechanism prevents charge accumulation on the target, enabling the sputtering of dielectric materials.
-
Magnetic Field Utilization:
- Both techniques use magnetic fields to enhance plasma confinement and deposition efficiency. The magnetic field causes electrons to spiral along magnetic flux lines, confining the plasma close to the target material. This prevents damage to the thin film being formed and improves the overall deposition process.
-
Applications:
- DC Magnetron Sputtering: Commonly used in industries requiring high deposition rates and cost efficiency, such as large-scale metal coating applications.
- RF Magnetron Sputtering: Preferred for specialized applications involving dielectric materials or smaller substrates, such as in the semiconductor and optics industries.
In summary, RF and DC magnetron sputtering differ significantly in their power sources, material compatibility, deposition rates, and operational requirements. The choice between the two depends on the specific application, material properties, and production scale.
Summary Table:
Aspect | DC Magnetron Sputtering | RF Magnetron Sputtering |
---|---|---|
Power Source | Direct Current (DC) | Alternating Current (AC) at 13.56 MHz |
Material Compatibility | Limited to conductive materials (e.g., Iron, Copper, Nickel) | Suitable for both conductive and non-conductive materials, including dielectrics |
Deposition Rate | High deposition rates, ideal for large-scale production | Lower deposition rates, suitable for smaller substrates or specialized applications |
Operational Pressure | Higher chamber pressures (1 to 100 mTorr) | Lower pressures due to high ionized particle percentage |
Cost | Cost-efficient for large substrates | Higher equipment and operational costs |
Applications | Large-scale metal coating applications | Semiconductor and optics industries |
Need help choosing the right sputtering technique for your application? Contact our experts today!