Sintering and melting are two distinct processes used to combine or transform materials, but they differ fundamentally in terms of temperature requirements, mechanisms, and outcomes. Sintering involves bonding particles together using heat and pressure without reaching the material's melting point, while melting requires heating a material to or above its melting temperature to transition it from a solid to a liquid state. Sintering is often used to create solid structures from powdered materials, particularly for metals with high melting points, and it enhances properties like strength and hardness. Melting, on the other hand, is typically used for casting or reshaping materials in their liquid state. The key difference lies in the material's state during the process: sintering avoids liquefaction, whereas melting relies on it.
Key Points Explained:
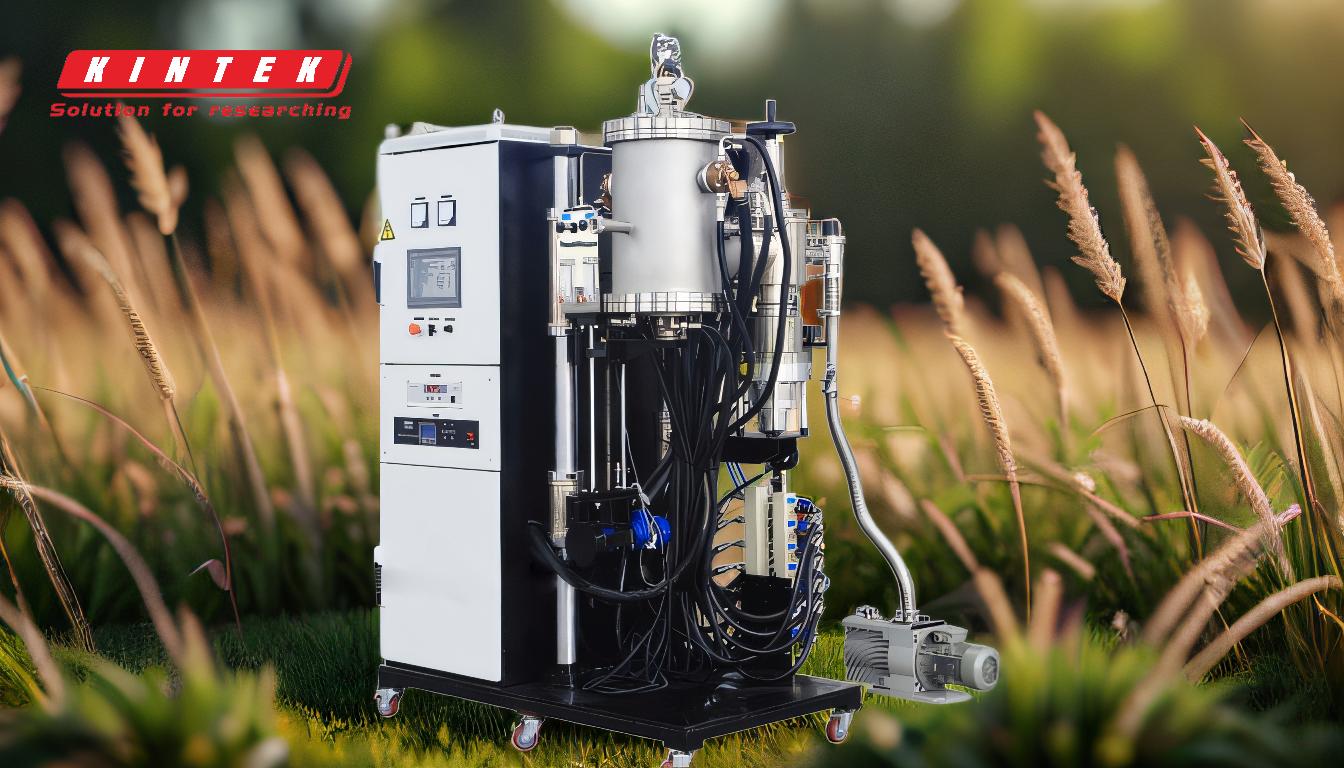
-
Temperature Requirements:
- Sintering: Occurs at temperatures below the material's melting point. The process relies on a combination of heat and pressure to bond particles together without liquefying the material.
- Melting: Requires temperatures at or above the material's melting point to transition it from a solid to a liquid state. The energy threshold for melting is significantly higher than that for sintering.
-
Mechanism of Action:
- Sintering: Involves the diffusion of atoms across particle boundaries, leading to bonding and densification. The material remains in a solid state throughout the process.
- Melting: Involves breaking the atomic bonds within the material, allowing it to flow as a liquid. This process requires overcoming the material's latent heat of fusion.
-
Material State:
- Sintering: The material remains solid, with particles bonding at their interfaces. This avoids the challenges associated with handling liquids, such as flow control and solidification defects.
- Melting: The material transitions to a liquid state, which is necessary for processes like casting, molding, or alloying.
-
Applications:
- Sintering: Commonly used in powder metallurgy to create complex shapes from metal powders, especially for materials with high melting points. It is also used in ceramics and composites to enhance mechanical properties.
- Melting: Used in processes like casting, welding, and alloy production, where the material must be in a liquid state to fill molds or combine with other materials.
-
Advantages and Limitations:
-
Sintering:
- Advantages: Enables the production of parts with high strength, hardness, and dimensional accuracy. It is particularly useful for materials that are difficult to melt or cast.
- Limitations: Requires precise control of temperature and pressure, and the process can be slower compared to melting.
-
Melting:
- Advantages: Allows for the creation of homogeneous mixtures and the reshaping of materials into new forms. It is essential for processes like casting and alloying.
- Limitations: Requires high energy input and careful handling of molten materials to avoid defects like porosity or cracks during solidification.
-
Sintering:
-
Material Properties:
- Sintering: Enhances properties like strength, hardness, and wear resistance by creating a dense, cohesive structure from powdered materials.
- Melting: Can alter material properties depending on the cooling rate and solidification process. Rapid cooling may lead to increased hardness but reduced ductility.
-
Energy Efficiency:
- Sintering: Generally more energy-efficient than melting because it operates at lower temperatures and does not require the material to reach its melting point.
- Melting: Energy-intensive due to the high temperatures required to achieve and maintain the liquid state.
By understanding these key differences, equipment and consumable purchasers can make informed decisions about which process is best suited for their specific applications, balancing factors like material properties, energy consumption, and production requirements.
Summary Table:
Aspect | Sintering | Melting |
---|---|---|
Temperature | Below material's melting point | At or above material's melting point |
Mechanism | Diffusion of atoms across particle boundaries; solid-state bonding | Breaking atomic bonds; transitions to liquid state |
Material State | Remains solid | Transitions to liquid |
Applications | Powder metallurgy, ceramics, composites | Casting, welding, alloy production |
Advantages | High strength, hardness, dimensional accuracy | Homogeneous mixtures, reshaping materials |
Limitations | Requires precise control; slower process | High energy input; handling molten materials |
Energy Efficiency | More energy-efficient | Energy-intensive |
Need help choosing the right process for your materials? Contact our experts today for personalized advice!