Sintering and vitrification are two distinct processes used in materials science and manufacturing, each with unique mechanisms, applications, and outcomes. Sintering involves bonding particles together at temperatures below their melting point, using pressure and heat to create a solid structure without liquefaction. This process is energy-efficient and allows for precise control over material properties. Vitrification, on the other hand, involves heating materials to a temperature where they melt and then cool to form a glass-like, amorphous solid. This process requires higher temperatures and results in a non-crystalline structure, often used in ceramics and glass production. Below, we explore the key differences between these two processes in detail.
Key Points Explained:
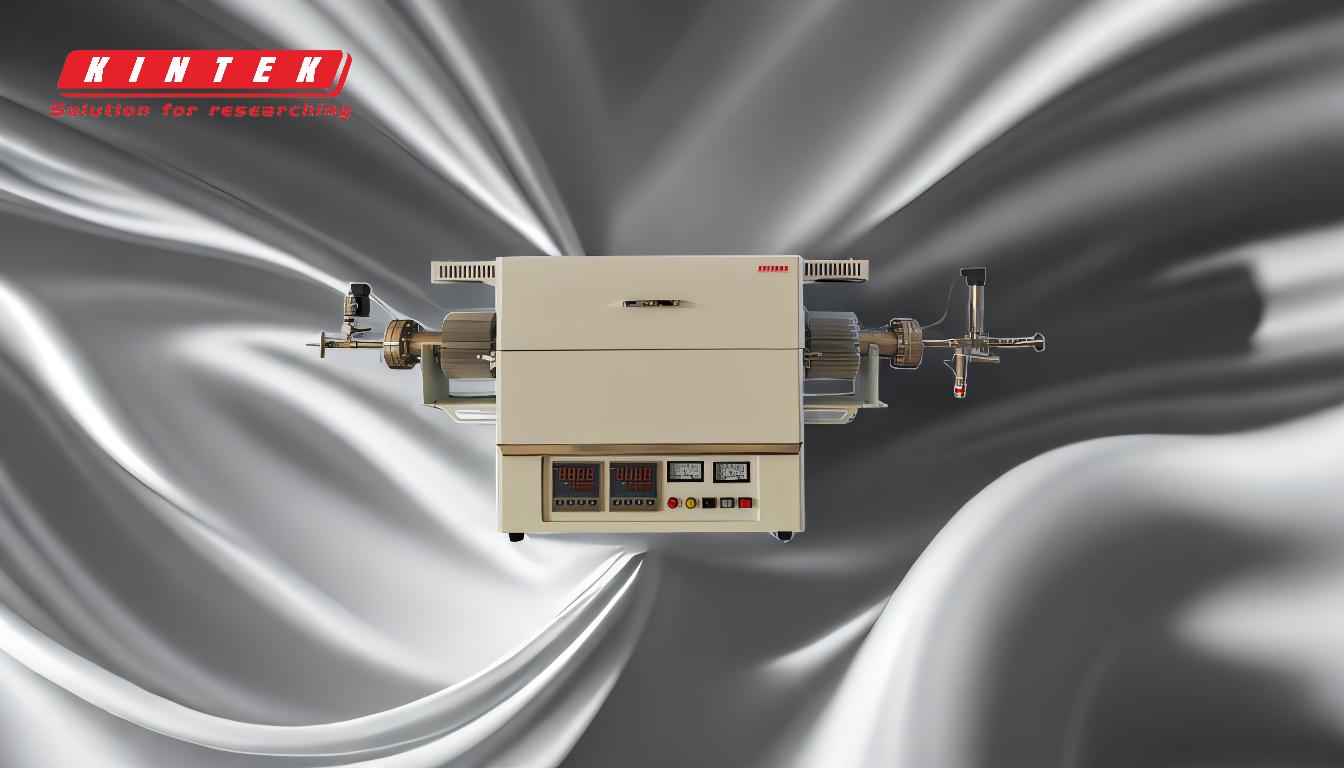
-
Definition and Mechanism:
- Sintering: Sintering is a process where powdered materials are compacted and heated to a temperature below their melting point. The particles bond through diffusion, forming a solid structure without undergoing a complete phase change. This process often involves the application of pressure to enhance bonding.
- Vitrification: Vitrification involves heating materials to a temperature where they melt completely, forming a liquid phase. Upon cooling, the material solidifies into a glass-like, amorphous structure without crystallizing. This process requires higher temperatures than sintering.
-
Temperature Requirements:
- Sintering: Occurs at temperatures below the melting point of the material, making it more energy-efficient. The exact temperature depends on the material but is typically 70-90% of the melting point.
- Vitrification: Requires temperatures high enough to melt the material completely, often exceeding the melting point. This makes vitrification more energy-intensive compared to sintering.
-
Microstructure and Properties:
- Sintering: Results in a porous or dense structure, depending on the conditions. The final product retains some crystalline properties and can exhibit controlled porosity, which is useful in applications like filters or catalysts.
- Vitrification: Produces a non-crystalline, glassy structure. The material becomes homogeneous and often transparent, with properties like high strength, chemical resistance, and thermal stability.
-
Applications:
- Sintering: Commonly used in powder metallurgy, ceramics, and additive manufacturing. It is ideal for creating complex shapes, controlling porosity, and producing materials with specific mechanical properties.
- Vitrification: Widely used in the production of glass, ceramics, and certain types of coatings. It is also employed in waste immobilization, where hazardous materials are encapsulated in a glass matrix to prevent leaching.
-
Advantages and Limitations:
-
Sintering:
- Advantages: Lower energy consumption, precise control over material properties, ability to produce complex shapes, and cost-effectiveness for large-scale production.
- Limitations: Limited to materials that can withstand the sintering process without degrading, and the final product may have residual porosity.
-
Vitrification:
- Advantages: Produces materials with high strength, chemical resistance, and thermal stability. Ideal for creating transparent or glass-like products.
- Limitations: High energy consumption, limited to materials that can form a glassy phase, and potential for thermal stress during cooling.
-
Sintering:
-
Process Control and Consistency:
- Sintering: Offers greater control over the final product's properties, such as density, porosity, and mechanical strength. The process is highly reproducible, making it suitable for industrial applications.
- Vitrification: Requires precise control over cooling rates to avoid crystallization and thermal stress. The process can be more challenging to standardize, especially for large or complex shapes.
-
Material Compatibility:
- Sintering: Compatible with a wide range of materials, including metals, ceramics, and composites. The process can be tailored to suit specific material requirements.
- Vitrification: Primarily used for materials that can form a glassy phase, such as silica-based ceramics and certain polymers. Not all materials are suitable for vitrification.
-
Environmental and Economic Considerations:
- Sintering: Generally more environmentally friendly due to lower energy consumption and reduced emissions. It is also cost-effective for mass production.
- Vitrification: While energy-intensive, it is often used for specialized applications where the unique properties of vitrified materials are required. The process can be more expensive but is justified in high-value applications.
In summary, sintering and vitrification are distinct processes with different mechanisms, temperature requirements, and applications. Sintering is ideal for creating solid structures with controlled properties, while vitrification is used to produce glass-like materials with high strength and chemical resistance. Understanding these differences is crucial for selecting the appropriate process for a given application.
Summary Table:
Aspect | Sintering | Vitrification |
---|---|---|
Definition | Bonds particles below melting point using heat and pressure. | Melts materials completely to form a glass-like, amorphous structure. |
Temperature | Below melting point (70-90% of melting point). | Above melting point, often exceeding it. |
Microstructure | Porous or dense, retains crystalline properties. | Non-crystalline, glassy, and homogeneous. |
Applications | Powder metallurgy, ceramics, additive manufacturing. | Glass production, ceramics, waste immobilization. |
Advantages | Energy-efficient, precise control, cost-effective for mass production. | High strength, chemical resistance, thermal stability. |
Limitations | Residual porosity, limited material compatibility. | High energy consumption, thermal stress, limited to glass-forming materials. |
Material Compatibility | Metals, ceramics, composites. | Silica-based ceramics, certain polymers. |
Environmental Impact | Lower energy consumption and emissions. | Higher energy consumption but justified for specialized applications. |
Need help choosing the right process for your application? Contact our experts today for personalized guidance!