Sputtering and physical vapor deposition (PVD) are both techniques used to deposit thin films onto substrates, but they differ significantly in their mechanisms and applications. Sputtering is a subset of PVD, which encompasses various methods like thermal evaporation and electron-beam evaporation. The primary distinction lies in how the material is converted into a vapor for deposition. Sputtering uses energetic ions to physically dislodge atoms from a target material, while other PVD methods typically rely on heating the material to its vaporization point. This fundamental difference makes sputtering more versatile, especially for temperature-sensitive materials like plastics and organics, as it operates at lower temperatures compared to other PVD techniques.
Key Points Explained:
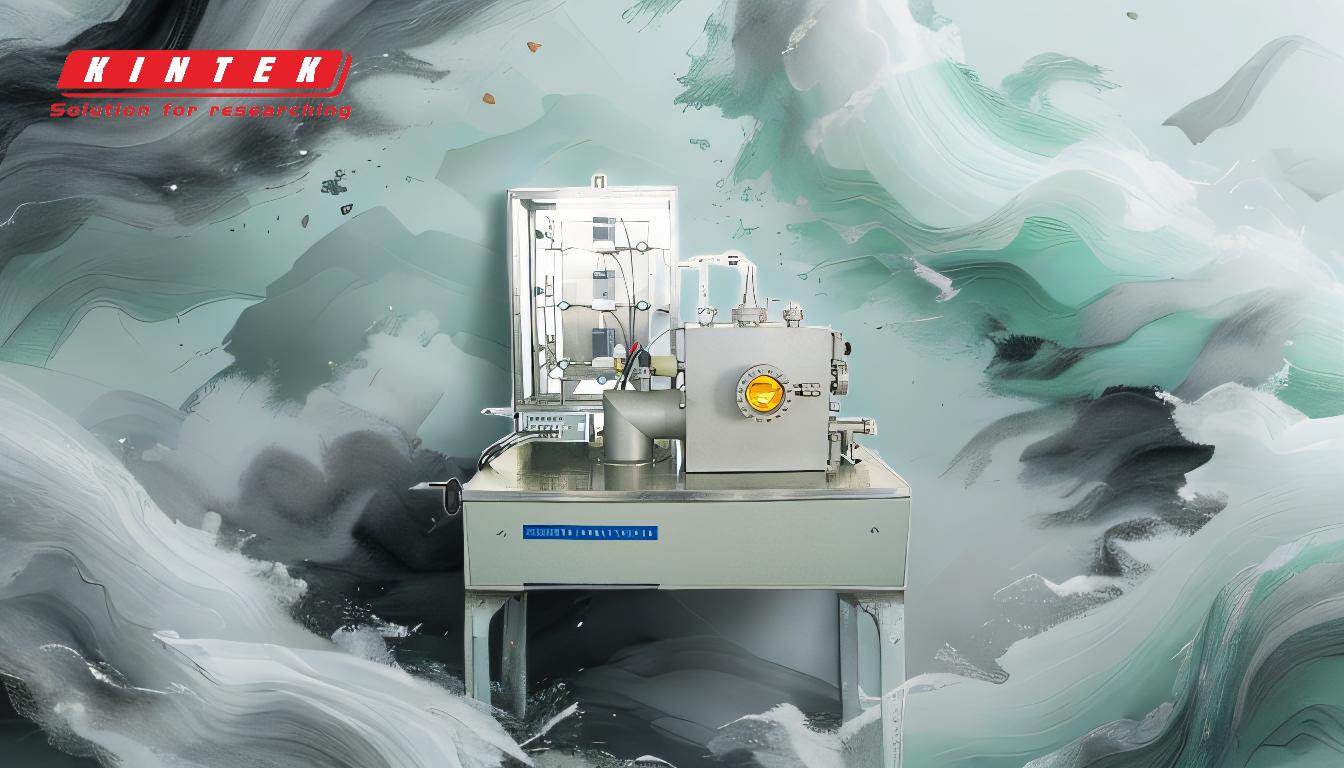
-
Mechanism of Material Vaporization:
- Sputtering: In sputtering, a plasma is generated between the target material and the substrate. Energetic ions from the plasma collide with the target, physically knocking out (sputtering) atoms from the target surface. These atoms then travel to the substrate and form a thin film.
- Other PVD Methods (e.g., Thermal or E-beam Evaporation): These methods rely on heating the target material to its vaporization temperature, creating a vapor that condenses on the substrate. The material is typically melted or sublimated to achieve this.
-
Energy Source:
- Sputtering: Uses electrical energy to generate a plasma, which produces energetic ions. These ions transfer their momentum to the target material, ejecting atoms without the need for high temperatures.
- Other PVD Methods: Rely on thermal energy to vaporize the target material. This often requires high temperatures, which can limit the types of substrates that can be coated.
-
Process Temperature:
- Sputtering: Operates at lower temperatures compared to other PVD methods. This makes it suitable for coating temperature-sensitive materials such as plastics, organics, and certain types of glass.
- Other PVD Methods: Typically require higher temperatures to achieve vaporization, which can be detrimental to heat-sensitive substrates.
-
Material Compatibility:
- Sputtering: Can deposit a wide range of materials, including metals, alloys, and ceramics, without melting the target material. This is because the process relies on momentum transfer rather than thermal energy.
- Other PVD Methods: May struggle with materials that have high melting points or are sensitive to thermal degradation, as they require the material to be heated to high temperatures.
-
Film Quality and Uniformity:
- Sputtering: Often produces films with better adhesion and uniformity, especially for complex geometries. The process allows for precise control over the deposition rate and film thickness.
- Other PVD Methods: While still capable of producing high-quality films, they may face challenges in achieving uniform coatings on complex shapes due to line-of-sight deposition issues.
-
Applications:
- Sputtering: Widely used in industries requiring precise, low-temperature deposition, such as semiconductor manufacturing, optical coatings, and flexible electronics.
- Other PVD Methods: Commonly used in applications where high-temperature processing is acceptable, such as in the deposition of metals for decorative coatings or in high-temperature resistant films.
In summary, while both sputtering and other PVD methods are used for thin film deposition, sputtering stands out due to its ability to operate at lower temperatures and its reliance on momentum transfer rather than thermal energy. This makes it particularly advantageous for coating temperature-sensitive materials and achieving high-quality, uniform films across various applications.
Summary Table:
Aspect | Sputtering | Other PVD Methods |
---|---|---|
Mechanism | Uses energetic ions to dislodge atoms from a target material. | Relies on heating the material to its vaporization point. |
Energy Source | Electrical energy generates plasma for ion bombardment. | Thermal energy heats the material to vaporize it. |
Process Temperature | Operates at lower temperatures, ideal for heat-sensitive materials. | Requires higher temperatures, limiting use with heat-sensitive substrates. |
Material Compatibility | Deposits metals, alloys, and ceramics without melting the target. | May struggle with high-melting-point or thermally sensitive materials. |
Film Quality | Produces uniform films with better adhesion, even on complex geometries. | May face challenges in achieving uniform coatings on complex shapes. |
Applications | Used in semiconductor manufacturing, optical coatings, and flexible electronics. | Suitable for decorative coatings and high-temperature-resistant films. |
Need help choosing the right thin film deposition method? Contact our experts today for personalized guidance!