Thermal evaporation and magnetron sputtering are two widely used thin-film deposition techniques, each with distinct characteristics and applications. Thermal evaporation involves heating a material in a vacuum until it vaporizes, forming a thin film on a substrate. It offers high deposition rates and is suitable for applications like OLEDs and thin-film transistors. Magnetron sputtering, on the other hand, uses a high-energy plasma to eject atoms from a target material, depositing them onto a substrate. This method provides better film adhesion, uniformity, and versatility in color options, making it ideal for electrical and optical applications. The choice between the two depends on factors like deposition rate, film quality, and specific application requirements.
Key Points Explained:
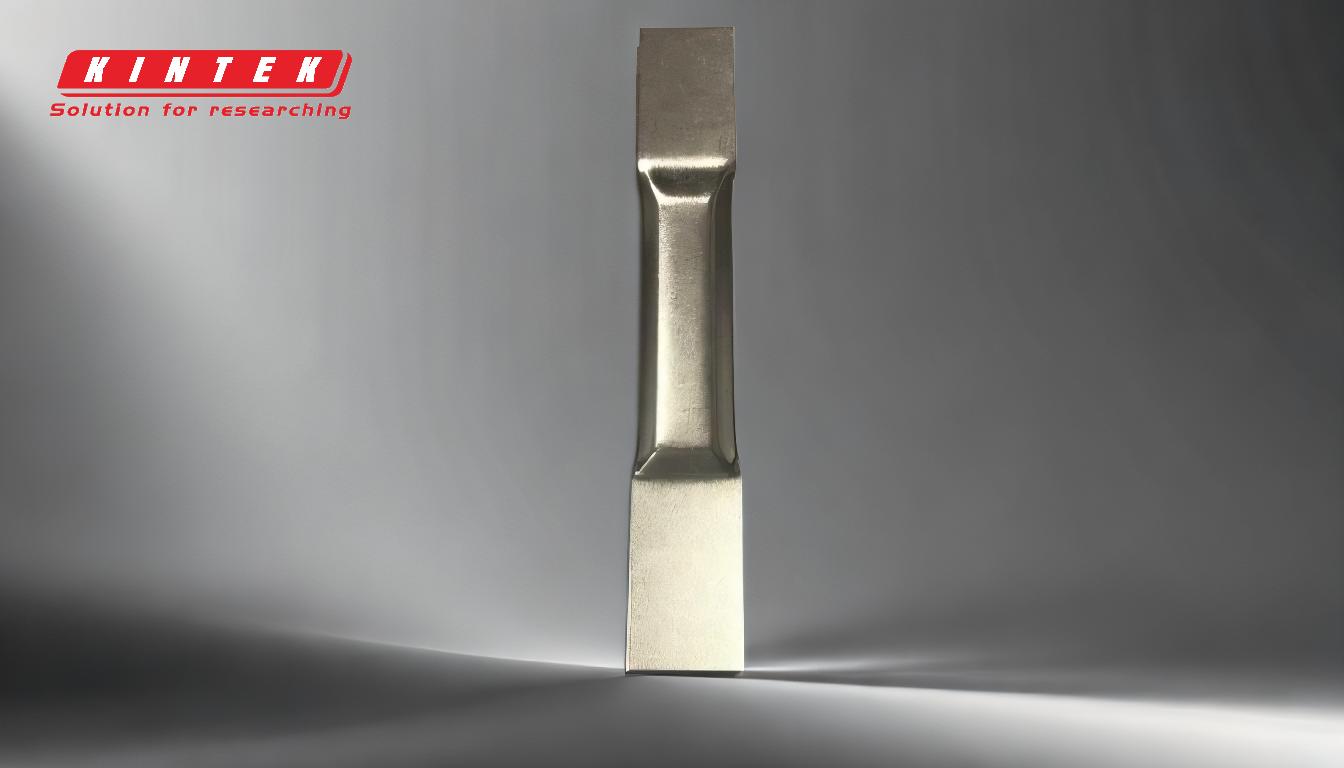
1. Mechanism of Deposition
-
Thermal Evaporation:
- Uses a resistive heat source to evaporate a solid material in a vacuum.
- Produces a robust vapor stream, enabling higher deposition rates.
- Suitable for creating alloys and sequential coatings.
-
Magnetron Sputtering:
- Involves colliding positively charged ions with a negatively charged target material.
- Ejects single atoms or clusters, resulting in better film uniformity and adhesion.
- Operates within a closed magnetic field, allowing for higher scalability and automation.
2. Film Characteristics
-
Adhesion:
- Thermal evaporation coatings exhibit relatively weaker adhesion due to lower energy deposition.
- Sputtered films have better substrate adhesion because of the high-energy process involved.
-
Uniformity:
- Thermal evaporation provides superior film uniformity.
- Sputtering may contain particles, leading to slightly lower uniformity but better overall film quality.
-
Grain Size:
- Sputtering produces smaller grain sizes, enhancing film properties like hardness and durability.
- Thermal evaporation results in larger grain sizes, which may affect the film's mechanical properties.
3. Deposition Rate and Efficiency
-
Thermal Evaporation:
- Higher deposition rates, making it suitable for applications requiring quick coating.
- Shorter run times due to the robust vapor stream.
-
Magnetron Sputtering:
- Lower deposition rates, except for pure metals.
- Longer run times but offers better control over film properties.
4. Color and Material Versatility
-
Thermal Evaporation:
- Limited to the true color of aluminum.
- Requires additional spray painting for other colors.
-
Magnetron Sputtering:
- Offers greater color versatility through modulation.
- Can produce a more realistic and uniform metal effect.
5. Applications
-
Thermal Evaporation:
- Commonly used for creating OLEDs and thin-film transistors.
- Effective for applications requiring high deposition rates and simple coatings.
-
Magnetron Sputtering:
- Ideal for electrical or optical production.
- Suitable for applications requiring high-quality films with excellent adhesion and uniformity.
6. Vacuum and Environmental Conditions
-
Thermal Evaporation:
- Requires a high vacuum environment.
- Less absorbed gas in the film, leading to purer coatings.
-
Magnetron Sputtering:
- Operates at lower vacuum levels.
- Higher absorbed gas content, which can affect film properties but also provides better adhesion.
7. Energy and Particle Dynamics
-
Thermal Evaporation:
- Deposited species have lower energy, resulting in less dense films.
- Atomized particles are more dispersed, leading to less directional deposition.
-
Magnetron Sputtering:
- Deposited species have higher energy, resulting in denser and more durable films.
- Atomized particles are more directional, allowing for better control over film thickness and uniformity.
8. Scalability and Automation
-
Thermal Evaporation:
- Less scalable and harder to automate due to the nature of the process.
-
Magnetron Sputtering:
- Highly scalable and can be automated for many applications, making it suitable for large-scale production.
In summary, the choice between thermal evaporation and magnetron sputtering depends on the specific requirements of the application, including factors like deposition rate, film quality, adhesion, and color versatility. Each method has its unique advantages and limitations, making them suitable for different types of projects and industries.
Summary Table:
Feature | Thermal Evaporation | Magnetron Sputtering |
---|---|---|
Mechanism | Resistive heating in a vacuum | High-energy plasma ejects atoms from a target |
Deposition Rate | High | Lower (except for pure metals) |
Film Adhesion | Weaker | Stronger |
Film Uniformity | Superior | Slightly lower but better overall quality |
Grain Size | Larger | Smaller |
Color Versatility | Limited to aluminum | Greater color options |
Applications | OLEDs, thin-film transistors | Electrical and optical production |
Vacuum Requirements | High vacuum | Lower vacuum |
Scalability | Less scalable | Highly scalable and automatable |
Still unsure which thin-film deposition technique fits your needs? Contact our experts today for personalized guidance!