Vacuum brazing and diffusion bonding are two advanced joining techniques used in high-performance applications, particularly in industries like aerospace, automotive, and electronics. While both processes occur in a vacuum environment to prevent oxidation and contamination, they differ significantly in their mechanisms, applications, and outcomes. Vacuum brazing uses a filler metal to join materials, while diffusion bonding relies on atomic diffusion to create a solid-state bond without melting the base materials. Understanding these differences is crucial for selecting the right process for specific industrial needs.
Key Points Explained:
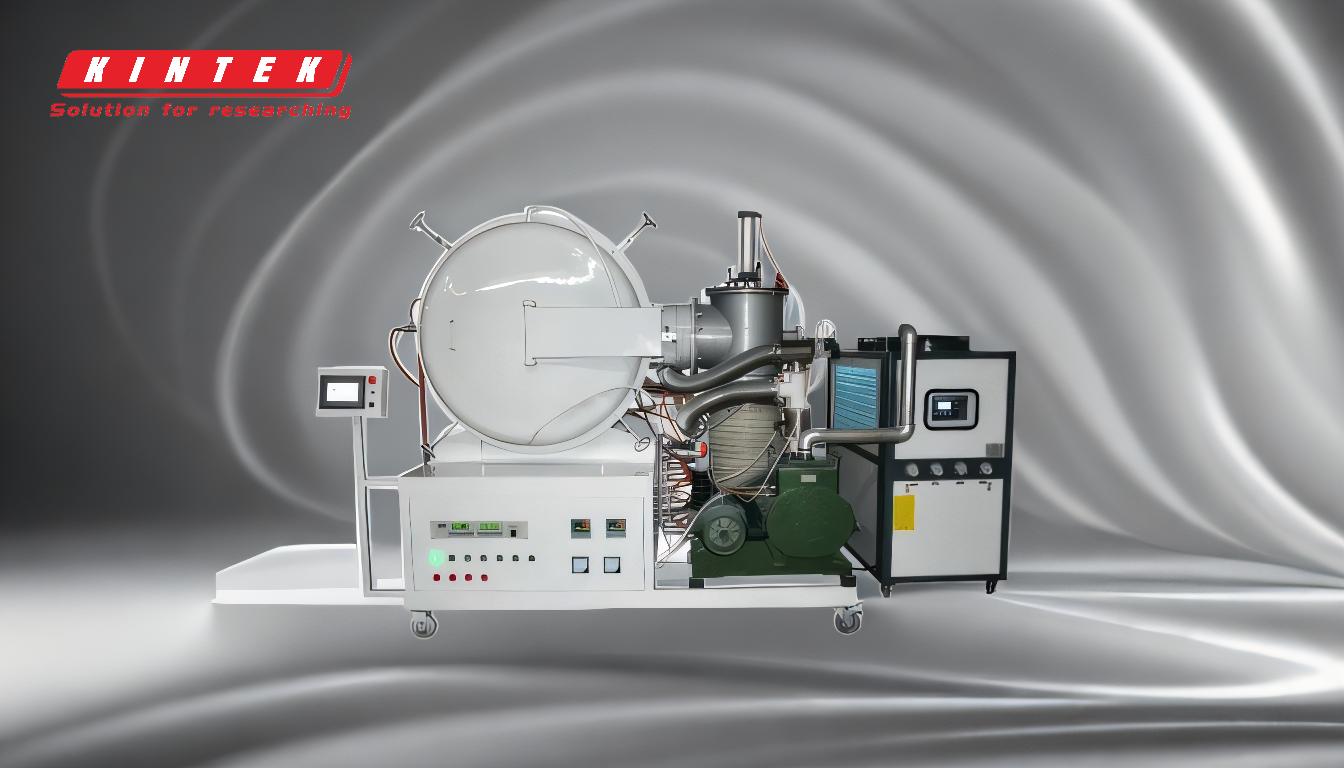
-
Mechanism of Joining:
- Vacuum Brazing: This process involves melting a filler metal (with a lower melting point than the base materials) to join two or more materials. The filler metal flows into the joint by capillary action, creating a strong bond upon solidification. The process is typically carried out in a vacuum brazing furnace to ensure a clean, oxidation-free environment.
- Diffusion Bonding: This is a solid-state welding process where two surfaces are joined by applying heat and pressure, causing atomic diffusion across the interface. No filler material is used, and the base materials do not melt. The bond forms due to the migration of atoms across the joint interface.
-
Temperature and Pressure Requirements:
- Vacuum Brazing: Operates at temperatures slightly above the melting point of the filler metal but below the melting point of the base materials. Pressure is generally not required, as capillary action drives the filler metal into the joint.
- Diffusion Bonding: Requires higher temperatures, often close to the melting point of the base materials, and significant pressure to ensure atomic diffusion. The process is slower and more controlled compared to vacuum brazing.
-
Applications:
- Vacuum Brazing: Ideal for joining dissimilar materials, such as metals to ceramics or composites, and for complex geometries. It is widely used in the aerospace industry for turbine blades, heat exchangers, and electronic components.
- Diffusion Bonding: Suited for applications requiring high structural integrity and no intermediate filler material, such as in the fabrication of titanium components for aerospace or medical implants.
-
Equipment:
- Vacuum Brazing: Requires a vacuum brazing furnace to maintain a controlled environment. These furnaces can be point-type (for localized brazing) or continuous (for large-scale production).
- Diffusion Bonding: Utilizes specialized presses or autoclaves capable of applying high pressure and temperature in a vacuum or inert gas environment.
-
Advantages and Limitations:
-
Vacuum Brazing:
- Advantages: Faster process, ability to join dissimilar materials, and lower equipment costs compared to diffusion bonding.
- Limitations: The presence of a filler metal can introduce weaknesses, and the process is less suitable for high-stress applications.
-
Diffusion Bonding:
- Advantages: Produces joints with near-parent material properties, no filler material required, and excellent for high-stress applications.
- Limitations: Longer processing times, higher equipment costs, and limited to materials with compatible diffusion properties.
-
Vacuum Brazing:
-
Quality and Strength of Joints:
- Vacuum Brazing: Joints are strong but may have lower mechanical properties compared to the base materials due to the presence of the filler metal.
- Diffusion Bonding: Joints exhibit mechanical properties similar to the base materials, making them ideal for critical applications.
By understanding these differences, manufacturers can choose the most appropriate joining method based on material compatibility, application requirements, and desired joint properties. Both processes have their unique advantages, and the choice often depends on the specific needs of the project.
Summary Table:
Aspect | Vacuum Brazing | Diffusion Bonding |
---|---|---|
Mechanism | Uses filler metal to join materials via capillary action. | Relies on atomic diffusion without melting base materials. |
Temperature | Slightly above filler metal melting point. | Close to base material melting point. |
Pressure | Not required. | High pressure required. |
Applications | Joining dissimilar materials, complex geometries (e.g., aerospace, electronics). | High-stress applications, no filler material (e.g., titanium components, implants). |
Equipment | Vacuum brazing furnace. | Specialized presses or autoclaves. |
Advantages | Faster process, lower cost, suitable for dissimilar materials. | Near-parent material properties, no filler, ideal for high-stress applications. |
Limitations | Filler metal may weaken joints, less suitable for high-stress applications. | Longer processing times, higher costs, limited to compatible materials. |
Need help choosing the right joining technique for your project? Contact our experts today for tailored solutions!