The diffusion of sintering refers to the movement of atoms within a powdered material during the sintering process, which is driven by the reduction in surface area and the minimization of energy. This atomic diffusion leads to the consolidation of powder particles, reducing local curvature and creating a denser, more unified material. Sintering is a critical process in powder metallurgy and ceramic manufacturing, where materials are heated below their melting point to form solid, durable masses without liquefaction. The diffusion mechanism is central to this process, as it enables particles to merge and densify, resulting in stronger and more cohesive structures.
Key Points Explained:
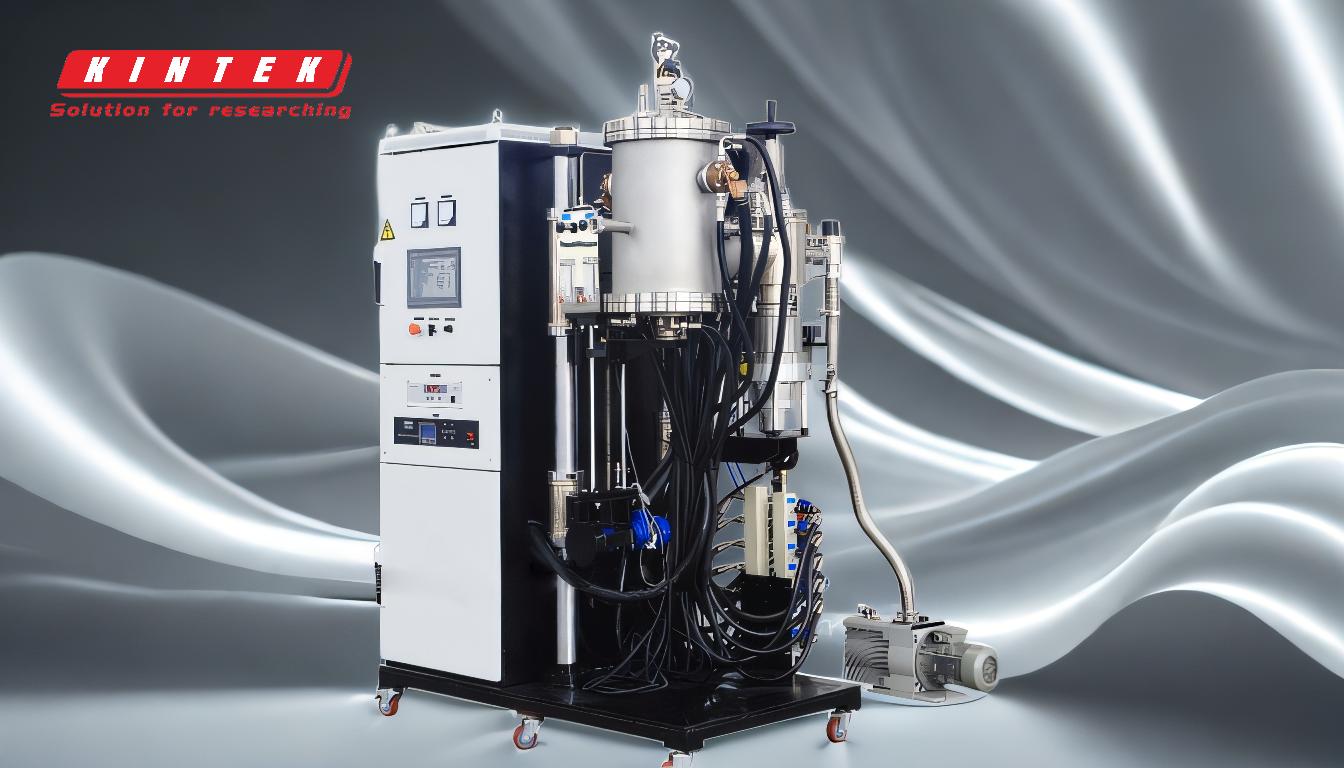
-
Definition of Sintering:
- Sintering is a manufacturing process that transforms powdery materials into dense, solid bodies by applying heat and pressure below the material's melting point. This process is widely used in powder metallurgy and ceramic production to create durable and cohesive materials.
-
Role of Diffusion in Sintering:
- Diffusion is the movement of atoms within the material, driven by the reduction in surface area and the minimization of energy. During sintering, atoms diffuse across particle boundaries, leading to the consolidation of powder particles and the formation of a unified mass.
-
Mechanism of Diffusion:
- Atomic diffusion occurs when atoms vibrate due to heat, allowing them to move through the material. This movement reduces local curvature and surface area, facilitating the merging of particles. The rate of diffusion depends on factors like temperature and the concentration gradient of atoms.
-
Stages of Sintering:
- Preparation: Powder compacts are formed using methods like cold welding, 3D printing, or pressing in a controlled atmosphere.
- Heating and Consolidation: The material is heated just below its melting point to activate crystalline microstructures.
- Particle Merging: Particles densify and merge, often accelerated by liquid phase sintering (LPS).
- Solidification: The material cools and solidifies into a cohesive mass.
-
Applications of Sintering:
- Sintering is used for materials with high melting points, such as tungsten and molybdenum, as well as in the production of pottery and metal components. It results in harder, stronger, and more durable materials.
-
Importance of Surface Area Reduction:
- The reduction in surface area during sintering is a key driver of diffusion. As particles merge, the overall surface area decreases, leading to a more stable and energy-efficient structure.
-
Liquid Phase Sintering (LPS):
- LPS accelerates the sintering process by introducing a liquid phase that enhances particle mobility and promotes faster densification. This method is particularly useful for materials that are difficult to sinter using traditional methods.
By understanding the diffusion process in sintering, manufacturers can optimize the sintering conditions to produce materials with desired properties, such as strength, durability, and density. This knowledge is crucial for industries that rely on powder metallurgy and ceramic manufacturing to create high-performance components.
Summary Table:
Key Aspect | Description |
---|---|
Definition of Sintering | A process transforming powdery materials into dense, solid bodies using heat and pressure. |
Role of Diffusion | Atoms move to reduce surface area, consolidating particles into a unified mass. |
Mechanism of Diffusion | Heat-induced atomic vibration enables particle merging, reducing local curvature. |
Stages of Sintering | Preparation, heating, particle merging, and solidification. |
Applications | Used for high-melting-point materials like tungsten and ceramics. |
Surface Area Reduction | Key driver of diffusion, leading to stable, energy-efficient structures. |
Liquid Phase Sintering (LPS) | Accelerates densification by introducing a liquid phase for faster merging. |
Optimize your sintering process for stronger materials—contact our experts today!