Two-roll mills, while advantageous for processing high-viscosity pastes and maintaining low temperatures due to cooled rollers, have notable disadvantages. The primary drawbacks include limited reduction capabilities due to large roll diameters and the roll flattening effect, which reduces efficiency. Additionally, the vast exposed surface area of the paste on the rollers leads to significant volatile loss, which can compromise the quality and consistency of the processed material. These factors make two-roll mills less suitable for applications requiring precise control over material properties or minimal volatile loss.
Key Points Explained:
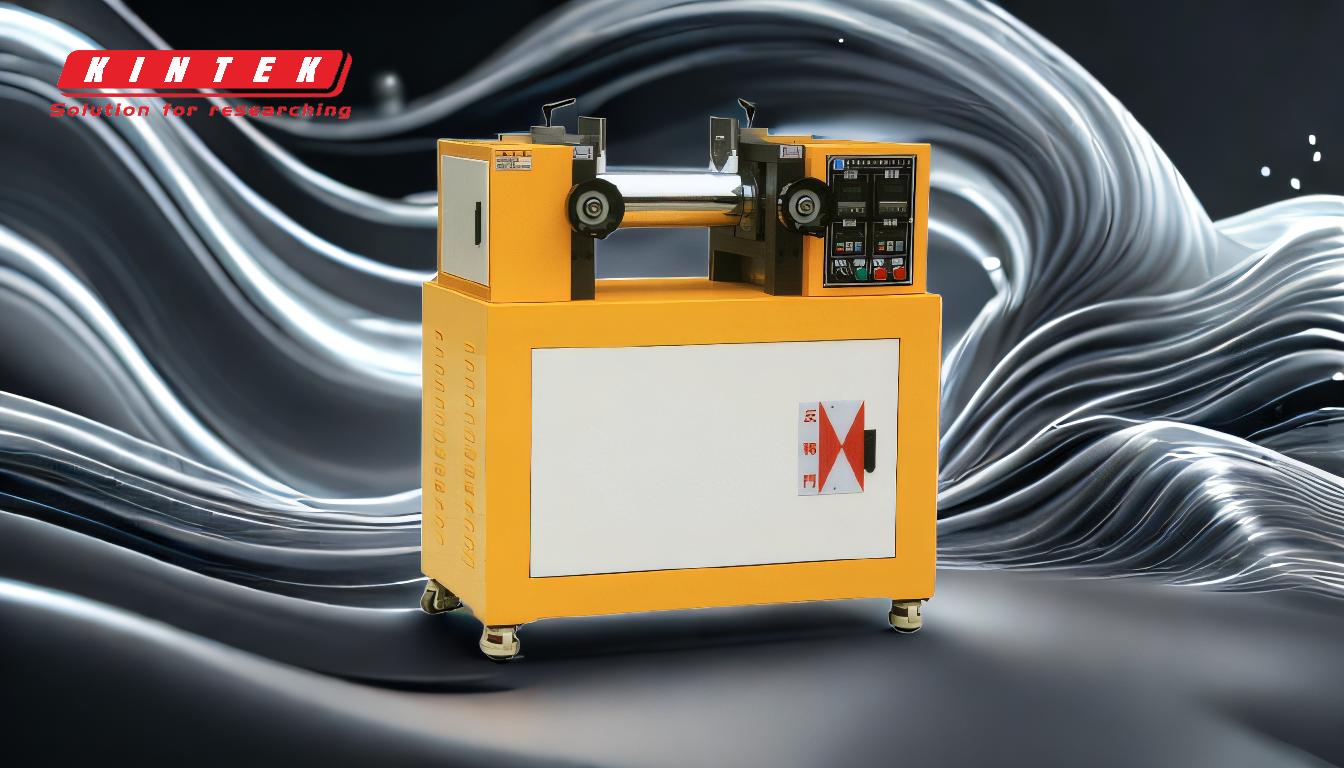
-
Limited Reduction Capability:
- Two-roll mills use large-diameter rolls, which inherently limit the amount of material reduction achievable in a single pass.
- The roll flattening effect occurs when the rolls deform under the high separating pressure applied during the milling process. This deformation increases the contact area between the rolls and the material, reducing the effective reduction capability.
- This limitation can be problematic for applications requiring significant material thickness reduction or fine particle dispersion.
-
Volatile Loss Due to Exposed Surface Area:
- The vast exposed surface area of the paste on the rollers is a significant disadvantage.
- Volatile components in the paste, such as solvents or low-boiling-point additives, can evaporate or degrade when exposed to air and heat during the milling process.
- This loss of volatiles can alter the material's properties, such as viscosity, consistency, and chemical composition, leading to inconsistent product quality.
-
Comparison with Three-Roll Mills:
- While three-roll mills also suffer from volatile loss due to exposed paste surfaces, they offer better control over material reduction and dispersion.
- Two-roll mills, in contrast, are less efficient for applications requiring minimal volatile loss or precise material processing.
-
Impact on Material Properties:
- The combination of limited reduction and volatile loss can negatively affect the final product's characteristics.
- For example, in industries like rubber or polymer processing, volatile loss can lead to poor curing properties or reduced mechanical strength in the final product.
-
Operational Considerations:
- The disadvantages of two-roll mills may necessitate additional processing steps or equipment to achieve the desired material properties.
- Operators may need to compensate for volatile loss by adjusting formulations or using supplementary cooling systems, increasing operational complexity and costs.
In summary, while two-roll mills are effective for certain applications, their limitations in reduction capability and susceptibility to volatile loss make them less suitable for processes requiring precise control over material properties or minimal volatile loss. These factors should be carefully considered when selecting laboratory mill equipment for specific applications.
Summary Table:
Disadvantage | Explanation | Impact |
---|---|---|
Limited Reduction Capability | Large roll diameters and roll flattening reduce material reduction efficiency. | Problematic for applications requiring fine particle dispersion or thickness reduction. |
Volatile Loss | Exposed surface area leads to evaporation of volatile components in the paste. | Alters material properties, causing inconsistent quality and performance. |
Operational Complexity | Requires additional steps or equipment to compensate for limitations. | Increases costs and processing time. |
Need help choosing the right milling equipment for your application? Contact us today for expert advice!