The double sintering method is a specialized sintering technique primarily used in the production of advanced ceramics and certain metal alloys. It involves two distinct sintering stages to achieve optimal material properties such as high density, improved mechanical strength, and reduced porosity. In the first stage, the material is sintered at a lower temperature to achieve partial densification and stabilize the structure. The second stage involves sintering at a higher temperature to fully densify the material and enhance its mechanical and thermal properties. This method is particularly useful for materials that are difficult to sinter in a single step due to their complex composition or sensitivity to thermal gradients.
Key Points Explained:
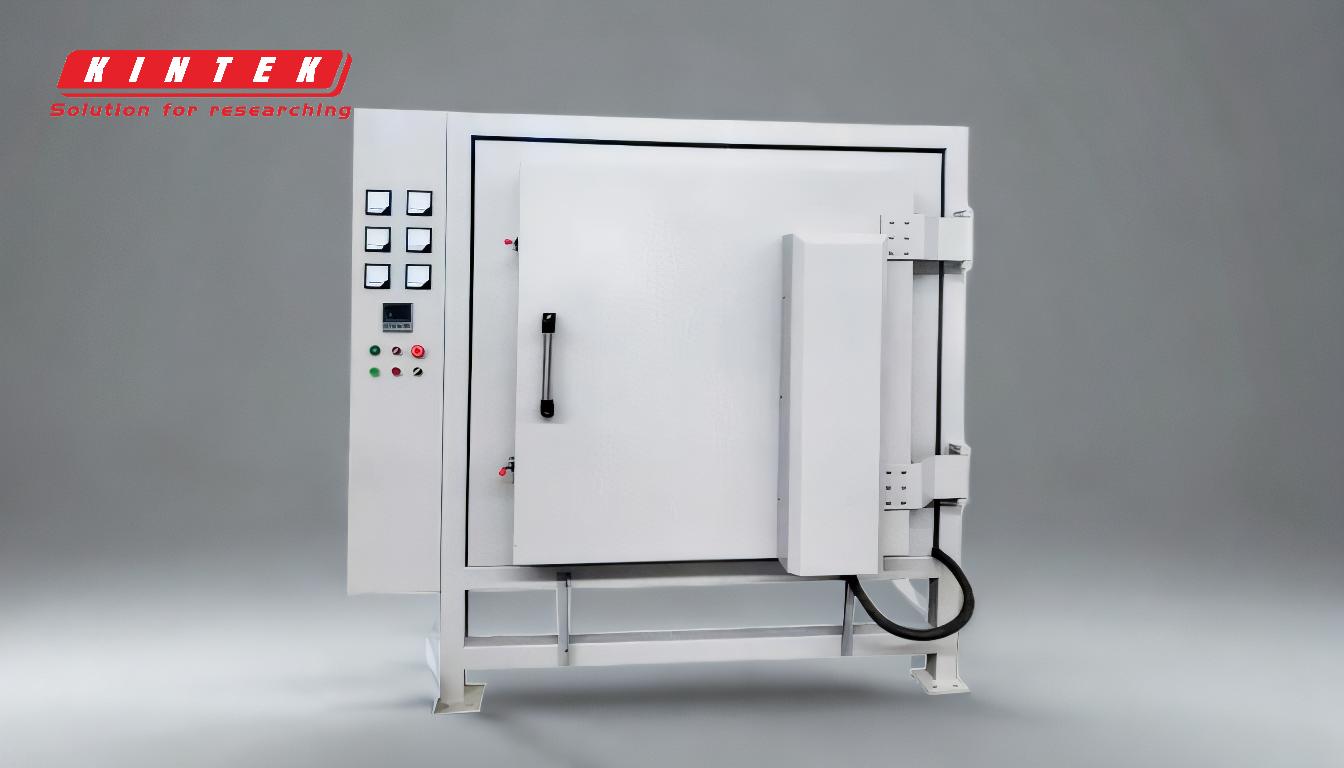
-
Definition of Double Sintering:
- Double sintering is a two-stage sintering process designed to optimize the densification and mechanical properties of materials, particularly ceramics and metal alloys.
- The first stage involves sintering at a lower temperature to achieve partial densification and structural stability.
- The second stage involves sintering at a higher temperature to fully densify the material and enhance its properties.
-
Purpose and Benefits:
- Enhanced Densification: The two-stage process allows for better control over the densification process, reducing the risk of defects such as cracks or voids.
- Improved Mechanical Properties: By fully densifying the material in the second stage, the final product exhibits higher strength, toughness, and wear resistance.
- Reduced Porosity: The double sintering method effectively minimizes porosity, which is crucial for applications requiring high density and low permeability.
-
Applications:
- Advanced Ceramics: Used in the production of high-performance ceramics for applications in electronics, aerospace, and medical devices.
- Metal Alloys: Employed in the manufacturing of complex metal components that require high strength and durability.
- Specialized Materials: Suitable for materials that are difficult to sinter in a single step due to their complex composition or sensitivity to thermal gradients.
-
Comparison with Single Sintering:
- Single Sintering: Involves a single heating cycle, which may not be sufficient for achieving full densification in complex materials.
- Double Sintering: Provides a more controlled and gradual approach, allowing for better management of thermal stresses and material properties.
-
Process Details:
- First Stage: The material is heated to a temperature just below its melting point to achieve partial densification. This stage stabilizes the material structure and reduces initial porosity.
- Second Stage: The material is then heated to a higher temperature to achieve full densification. This stage enhances the material's mechanical and thermal properties.
-
Technological Considerations:
- Temperature Control: Precise control of temperature in both stages is crucial to avoid thermal shock and ensure uniform densification.
- Atmosphere Control: The sintering process may require a controlled atmosphere (e.g., vacuum or inert gas) to prevent oxidation or contamination.
- Cooling Rate: The cooling rate after sintering can affect the final material properties, and controlled cooling is often necessary to achieve the desired microstructure.
In summary, the double sintering method is a sophisticated technique that offers significant advantages in the production of high-performance materials. By dividing the sintering process into two stages, it allows for better control over material properties, resulting in products with superior density, strength, and durability. This method is particularly valuable for advanced ceramics and complex metal alloys, where achieving optimal properties in a single sintering step is challenging.
Summary Table:
Aspect | Details |
---|---|
Definition | Two-stage sintering process for ceramics and metal alloys. |
First Stage | Lower temperature for partial densification and structural stability. |
Second Stage | Higher temperature for full densification and enhanced properties. |
Key Benefits | Improved density, strength, and reduced porosity. |
Applications | Advanced ceramics, metal alloys, and specialized materials. |
Comparison | Superior to single sintering for complex materials. |
Technological Factors | Precise temperature, atmosphere control, and cooling rate management. |
Interested in optimizing your material production? Contact our experts today to learn more about the double sintering method!