The dry bag process, specifically dry bag isostatic pressing, is a manufacturing technique used to produce high-quality ceramic bodies, particularly for small, axisymmetric parts like spark plugs. In this process, a pressurized rubber mold is pre-placed within a cylinder and remains there throughout the operation. The powder material is either loaded directly into the forming rubber mold or fed through a hopper into the pressurized rubber mold. Notably, the forming rubber mold does not come into contact with the liquid medium, distinguishing it from the wet bag process. This method is valued for its efficiency and ability to produce uniform, high-density components.
Key Points Explained:
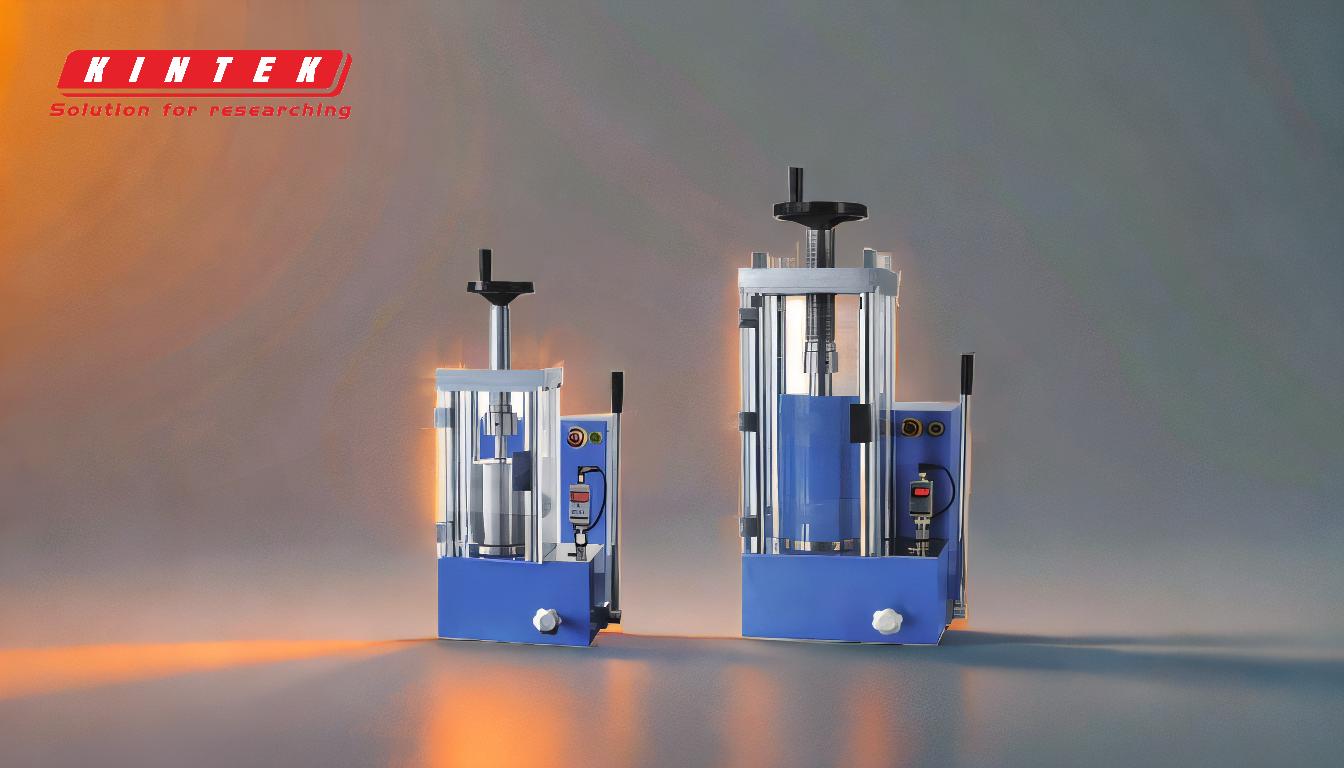
-
Definition and Purpose of Dry Bag Isostatic Pressing:
- Dry bag isostatic pressing is a specialized manufacturing process used to create high-quality ceramic components, particularly for small, axisymmetric parts such as spark plugs.
- The process is designed to achieve uniform density and high structural integrity in the final product.
-
Process Overview:
- A pressurized rubber mold is placed inside a cylinder and remains there throughout the entire process.
- The powder material is either loaded directly into the forming rubber mold or introduced through a feeding hopper from above.
- The forming rubber mold is isolated from the liquid medium, which is a key difference from the wet bag process.
-
Key Components and Their Roles:
- Pressurized Rubber Mold: This mold is pre-placed within the cylinder and is responsible for shaping the powder material under pressure.
- Forming Rubber Mold: This mold holds the powder material and is placed inside the pressurized rubber mold. It does not come into contact with the liquid medium.
- Feeding Hopper: Used to introduce the powder material into the pressurized rubber mold from above, ensuring a controlled and efficient filling process.
-
Advantages of Dry Bag Isostatic Pressing:
- Efficiency: The process is faster compared to wet bag isostatic pressing because the mold does not need to be removed and replaced after each cycle.
- Uniform Density: The method ensures a uniform distribution of pressure, leading to consistent density and quality in the final product.
- High-Quality Output: Ideal for producing small, axisymmetric parts with high precision and structural integrity.
-
Applications:
- Primarily used in the production of ceramic components, such as spark plugs, where high density and uniformity are critical.
- Suitable for manufacturing small parts that require precise shaping and high structural performance.
-
Comparison with Wet Bag Isostatic Pressing:
- Dry Bag: The forming rubber mold does not come into contact with the liquid medium, making the process more efficient and suitable for continuous production.
- Wet Bag: The mold is submerged in a liquid medium, which can be more time-consuming and less efficient for high-volume production.
By understanding these key points, one can appreciate the efficiency and precision of the dry bag isostatic pressing process, making it a valuable technique in the production of high-quality ceramic components.
Summary Table:
Aspect | Details |
---|---|
Definition | A manufacturing process for high-quality ceramic components like spark plugs. |
Key Components | Pressurized rubber mold, forming rubber mold, feeding hopper. |
Advantages | Efficiency, uniform density, high-quality output. |
Applications | Ceramic components, spark plugs, small axisymmetric parts. |
Comparison with Wet Bag | Dry bag is faster and more efficient; wet bag involves liquid medium. |
Interested in leveraging dry bag isostatic pressing for your manufacturing needs? Contact our experts today to learn more!