The drying zone in a rotary kiln is a critical section located near the raw material entrance, where the primary function is to remove moisture from the materials before they proceed to higher-temperature zones for further processing. In traditional cement rotary kilns, the drying zone operates at material temperatures of approximately 20℃~150℃ and gas temperatures of 250℃~400℃. However, in modern dry process cement rotary kilns, the drying zone is often minimized or eliminated due to advancements in pre-drying technologies. The drying zone ensures that materials are adequately prepared for subsequent thermal processing, which is essential for maintaining the quality and efficiency of the final product.
Key Points Explained:
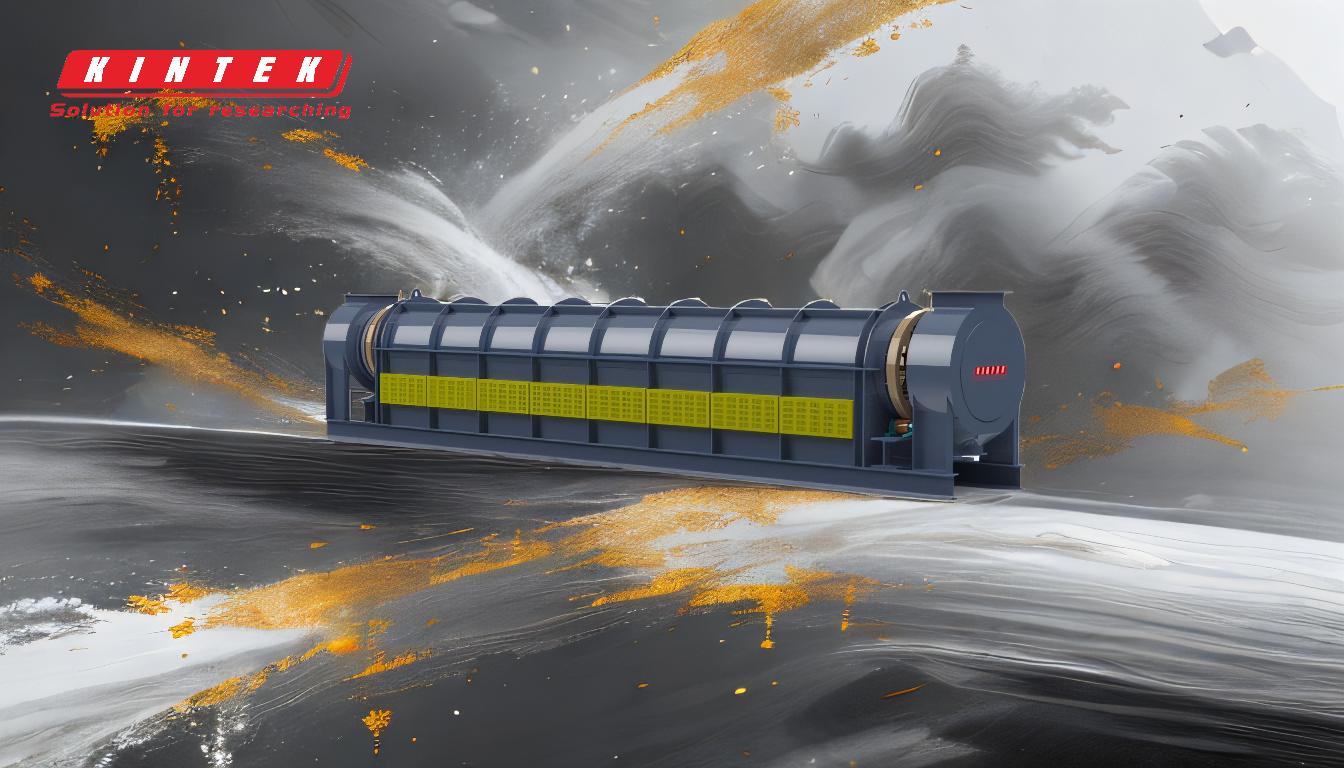
-
Definition and Location of the Drying Zone:
- The drying zone is a specific section of the rotary kiln, typically located near the raw material entrance.
- Its primary role is to remove moisture from the materials, preparing them for higher-temperature processing in subsequent zones.
-
Temperature Ranges in the Drying Zone:
- In traditional cement rotary kilns, the material temperature in the drying zone ranges from 20℃ to 150℃.
- The gas temperature in this zone is higher, typically between 250℃ and 400℃, to facilitate effective moisture removal.
-
Modern vs. Traditional Rotary Kilns:
- In modern dry process cement rotary kilns, the drying zone is often minimized or eliminated. This is due to the use of pre-drying technologies that remove moisture before the materials enter the kiln.
- Traditional rotary kilns, on the other hand, rely more heavily on the drying zone within the kiln itself.
-
Importance of the Drying Zone:
- The drying zone is crucial for ensuring that materials are adequately dried before they enter higher-temperature zones. This prevents issues such as thermal shock and ensures uniform heating.
- Proper drying also contributes to the overall efficiency of the kiln and the quality of the final product.
-
Role in Clinker Quality:
- The drying zone indirectly affects clinker quality by ensuring that materials are properly prepared for the firing process.
- High-quality clinker is essential for producing high-quality cement, which is directly related to the efficiency and profitability of the enterprise.
-
Specific Heat and Drying Efficiency:
- The specific heat of materials plays a role in the drying process. Materials with high specific heat require more energy to heat, which can affect the efficiency of the drying zone.
- Understanding the specific heat of materials helps in optimizing the drying process to ensure efficient moisture removal.
-
Electric Rotary Kilns:
- In the context of electric rotary kilns, the drying zone can be more precisely controlled due to the ability to regulate temperature and atmosphere more accurately.
- This precision is particularly beneficial in laboratory settings, where consistent and controlled conditions are essential for accurate testing and research.
-
Applications Beyond Cement:
- While the drying zone is most commonly discussed in the context of cement production, it is also relevant in other industries such as mining, metallurgy, and chemical processing.
- In these industries, the drying zone serves a similar purpose of preparing materials for high-temperature processing.
By understanding the drying zone's role and characteristics, operators can optimize the performance of rotary kilns, ensuring efficient and high-quality production across various industries.
Summary Table:
Aspect | Details |
---|---|
Definition | Section near the raw material entrance that removes moisture. |
Material Temperature | 20℃~150℃ (traditional kilns). |
Gas Temperature | 250℃~400℃ (traditional kilns). |
Modern Kilns | Drying zone minimized or eliminated due to pre-drying technologies. |
Importance | Prevents thermal shock, ensures uniform heating, and improves efficiency. |
Role in Clinker Quality | Ensures proper material preparation for firing, impacting cement quality. |
Applications | Cement production, mining, metallurgy, and chemical processing. |
Discover how the drying zone enhances rotary kiln efficiency—contact our experts today for tailored solutions!