The frequency of the alternating current (AC) in induction heating plays a critical role in determining the depth of heat generation, efficiency, and application suitability. Higher frequencies result in shallower heat penetration due to the skin effect, making them ideal for surface heating and hardening applications. Lower frequencies, on the other hand, allow deeper heat penetration and are better suited for bulk heating or melting processes. The choice of frequency also impacts the power capacity, turbulence in molten materials, and the overall efficiency of the induction heating system. Understanding these effects is essential for selecting the appropriate frequency for specific industrial applications.
Key Points Explained:
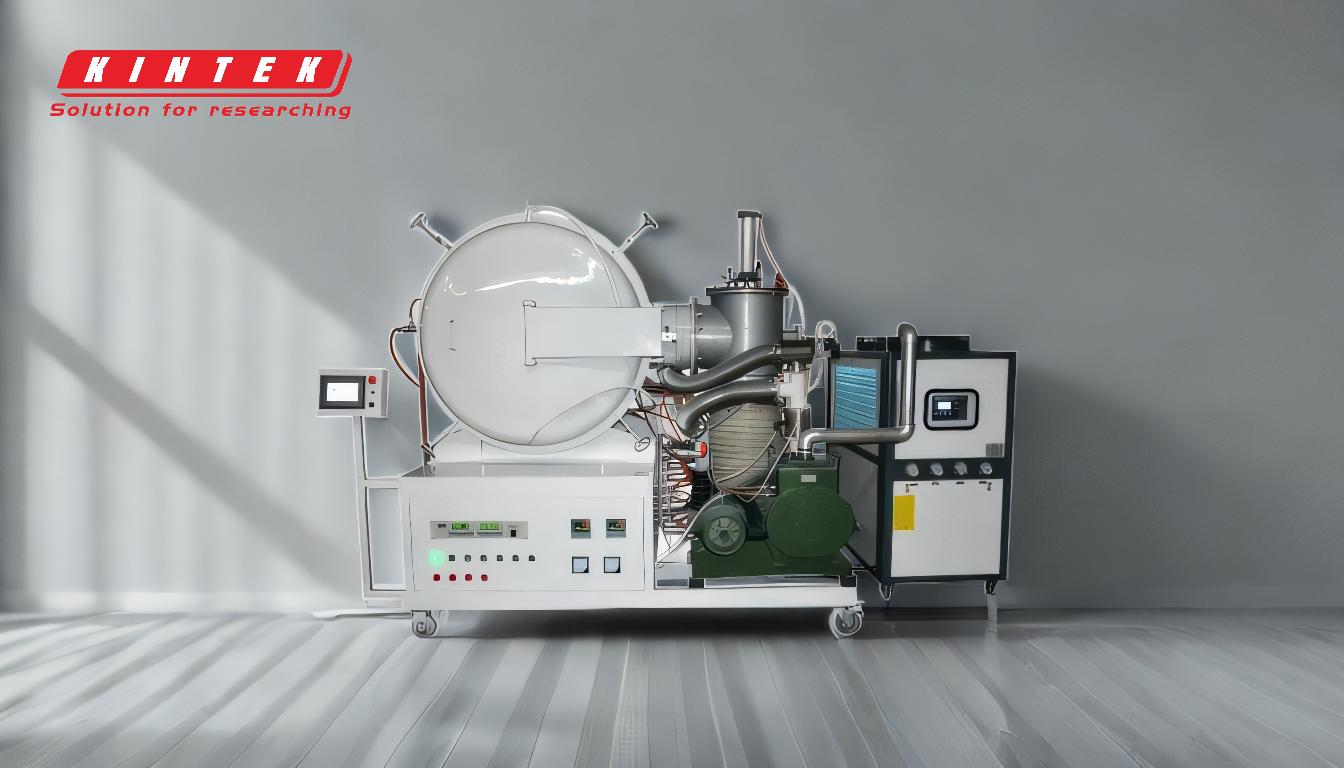
-
Frequency and Magnetic Field Dynamics:
- The frequency of the AC current determines how rapidly the magnetic field changes direction. For instance, a 60 Hz current causes the magnetic field to switch directions 60 times per second, while a 400 kHz current results in 400,000 switches per second.
- This rapid switching induces eddy currents in the workpiece, which generate heat through resistance. The frequency of the current in the coil directly controls the frequency of the induced current in the workpiece.
-
Depth of Heat Generation (Skin Effect):
- Higher frequencies (e.g., 400 kHz) create a greater current density difference between the surface and the interior of the workpiece, leading to a thinner heating layer. This phenomenon is known as the skin effect.
- Lower frequencies (e.g., 50–60 Hz) allow deeper penetration of the induced current, making them suitable for heating thicker materials or achieving uniform heating in bulk materials.
-
Applications Based on Frequency:
- High Frequencies: Ideal for surface hardening, where only the outer layer of the material needs to be heated above its critical temperature. Rapid cooling after heating achieves surface hardening.
- Low Frequencies: Suitable for melting or heating large volumes of material, as they provide deeper penetration and can induce stirring or turbulence in molten metals.
-
Power Capacity and Efficiency:
- Higher frequencies enable greater power application to a furnace of a given capacity, allowing for faster heating or melting processes.
- Lower frequencies, while less powerful for surface heating, are more efficient for bulk heating due to their deeper penetration and reduced energy loss.
-
Turbulence and Stirring in Molten Materials:
- Higher frequencies result in less turbulence in molten materials, which is beneficial for applications requiring precise control over the melt.
- Lower frequencies can generate significant turbulence, which may be advantageous for mixing or homogenizing molten metals.
-
Frequency Selection Factors:
- Material Properties: The electrical conductivity and magnetic permeability of the material influence the optimal frequency.
- Furnace Capacity: Smaller furnaces or melts typically require higher frequencies due to the skin depth effect.
- Application Requirements: The desired depth of heating, temperature uniformity, and processing speed dictate the choice of frequency.
By understanding these key points, equipment and consumable purchasers can make informed decisions about the frequency settings for induction heating systems, ensuring optimal performance and efficiency for their specific applications.
Summary Table:
Aspect | High Frequency (e.g., 400 kHz) | Low Frequency (e.g., 50–60 Hz) |
---|---|---|
Heat Penetration | Shallow (skin effect) | Deep |
Applications | Surface hardening, thin materials | Bulk heating, melting, thick materials |
Power Capacity | Higher power for faster heating | Lower power, efficient for bulk heating |
Turbulence in Molten Materials | Minimal turbulence, precise control | Significant turbulence, ideal for mixing |
Material Suitability | Thin, conductive materials | Thick, bulk materials |
Need help selecting the right frequency for your induction heating system? Contact our experts today for tailored solutions!