The effect of pressure on hydraulic fluid is a critical aspect of hydraulic system performance and efficiency. Pressure influences the fluid's viscosity, compressibility, and ability to transmit power. At high pressures, hydraulic fluids may experience changes in viscosity, which can affect flow rates and system responsiveness. Additionally, pressure impacts the fluid's compressibility, potentially leading to energy losses or reduced system efficiency. Understanding these effects is essential for selecting the right hydraulic fluid and maintaining optimal system performance under varying operating conditions.
Key Points Explained:
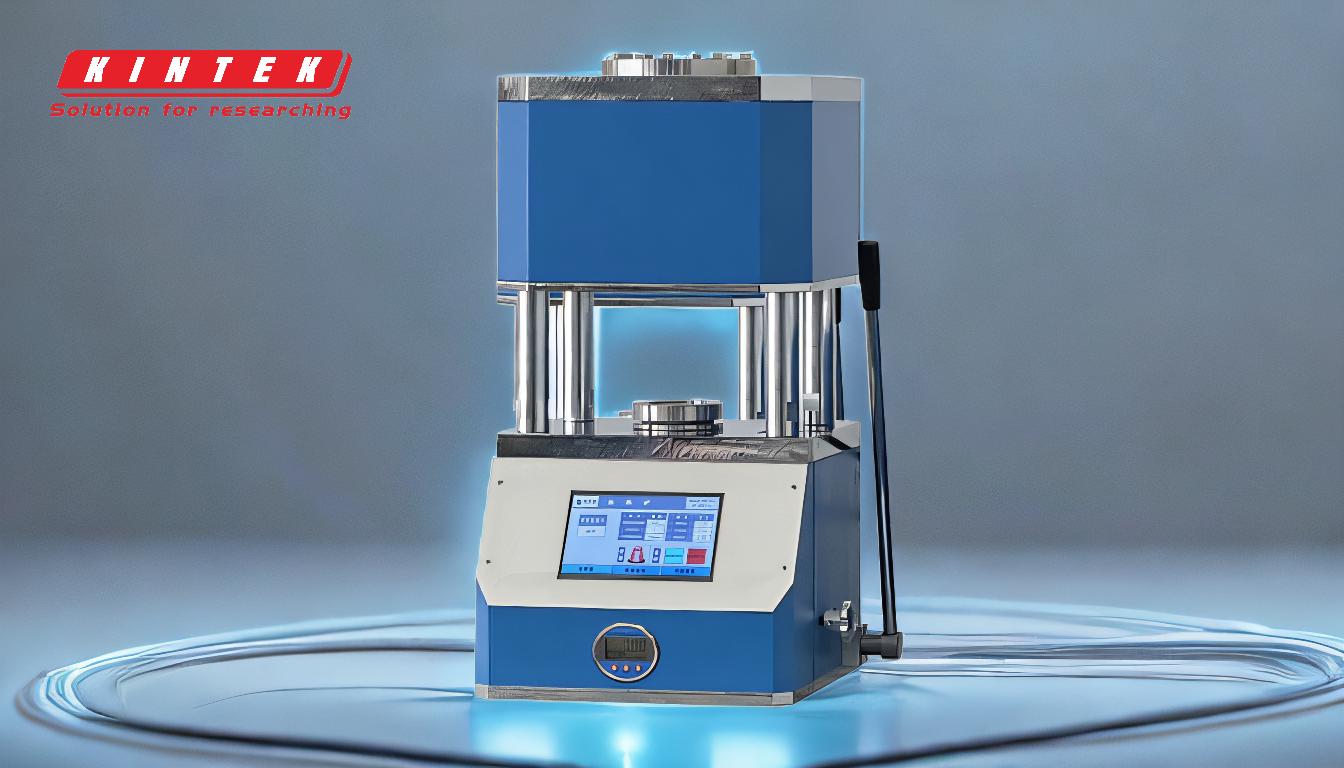
-
Viscosity Changes Under Pressure:
- Hydraulic fluids are designed to maintain consistent viscosity under varying pressures. However, as pressure increases, the viscosity of the fluid can also increase. This phenomenon, known as pressure-viscosity dependence, can affect the fluid's flow characteristics.
- Higher viscosity at elevated pressures may lead to reduced flow rates, increased friction, and higher energy consumption. Conversely, if the viscosity drops too low, it can result in inadequate lubrication and increased wear on system components.
- Selecting a hydraulic fluid with the appropriate viscosity index is crucial to ensure stable performance across a range of operating pressures.
-
Compressibility of Hydraulic Fluids:
- Hydraulic fluids are generally considered incompressible, but they do exhibit slight compressibility under high pressures. This compressibility can lead to energy losses in the form of heat and reduced system efficiency.
- In high-pressure systems, the compressibility of the fluid can cause delays in system response, known as "hydraulic lag." This can be particularly problematic in precision applications where rapid and accurate movements are required.
- To mitigate these effects, hydraulic systems often incorporate accumulators or other components to compensate for fluid compressibility.
-
Power Transmission Efficiency:
- Pressure is a key factor in the ability of hydraulic fluids to transmit power. Higher pressures enable greater force generation, but they also increase the stress on system components and the fluid itself.
- Excessive pressure can lead to fluid degradation, cavitation, and increased wear on seals and other components. It is essential to operate within the recommended pressure range for both the fluid and the system to ensure longevity and reliability.
- Regular monitoring and maintenance of hydraulic systems are necessary to detect and address pressure-related issues before they lead to system failure.
-
Thermal Effects and Pressure:
- Pressure and temperature are interrelated in hydraulic systems. As pressure increases, the fluid's temperature may also rise due to internal friction and energy losses. Elevated temperatures can further affect the fluid's viscosity and performance.
- High temperatures can accelerate fluid degradation, leading to the formation of sludge, varnish, and other contaminants. This can compromise system performance and increase maintenance requirements.
- Proper cooling and temperature control are essential to maintain the stability of hydraulic fluids under high-pressure conditions.
-
Selection of Hydraulic Fluids for High-Pressure Applications:
- When selecting hydraulic fluids for high-pressure systems, it is important to consider factors such as viscosity, compressibility, and thermal stability. Fluids with a high viscosity index and good thermal stability are better suited for high-pressure applications.
- Synthetic hydraulic fluids, which are engineered to withstand extreme conditions, are often preferred for high-pressure systems due to their superior performance and longer service life.
- Regular fluid analysis and testing can help ensure that the selected fluid continues to meet the system's requirements under varying pressure conditions.
In conclusion, pressure has a significant impact on the performance and efficiency of hydraulic fluids. By understanding the effects of pressure on viscosity, compressibility, power transmission, and thermal stability, users can make informed decisions when selecting and maintaining hydraulic fluids for their systems. Proper fluid selection, system design, and maintenance practices are essential to ensure optimal performance and longevity in high-pressure hydraulic applications.
Summary Table:
Aspect | Effect of Pressure | Impact on System |
---|---|---|
Viscosity | Increases under high pressure, affecting flow rates and energy consumption. | Reduced flow rates, increased friction, or inadequate lubrication. |
Compressibility | Slight compressibility leads to energy losses and hydraulic lag. | Delayed system response, reduced efficiency. |
Power Transmission | Higher pressures enable greater force but increase stress on components. | Fluid degradation, cavitation, and wear on seals. |
Thermal Effects | Pressure increases temperature, affecting viscosity and fluid stability. | Fluid degradation, sludge formation, and increased maintenance needs. |
Fluid Selection | High-pressure applications require fluids with high viscosity index and thermal stability. | Ensures stable performance and longer service life. |
Need help selecting the right hydraulic fluid for your high-pressure system? Contact our experts today for personalized advice!