The effect of sputtering gas pressure is significant in determining the quality, uniformity, and characteristics of the deposited thin film. At higher gas pressures, sputtered ions collide with gas atoms, leading to a diffusive motion and a random walk before condensing on the substrate or chamber walls. This results in lower-energy, thermalized motion, which can improve film uniformity but may reduce deposition rates. Conversely, lower gas pressures allow for high-energy ballistic impacts, leading to faster deposition but potentially less uniform films. The gas pressure also influences the sputtering rate, which depends on factors like ion energy, target atom mass, and sputter yield. Proper control of gas pressure is crucial for achieving desired film properties, such as coverage, surface mobility, and overall deposition quality.
Key Points Explained:
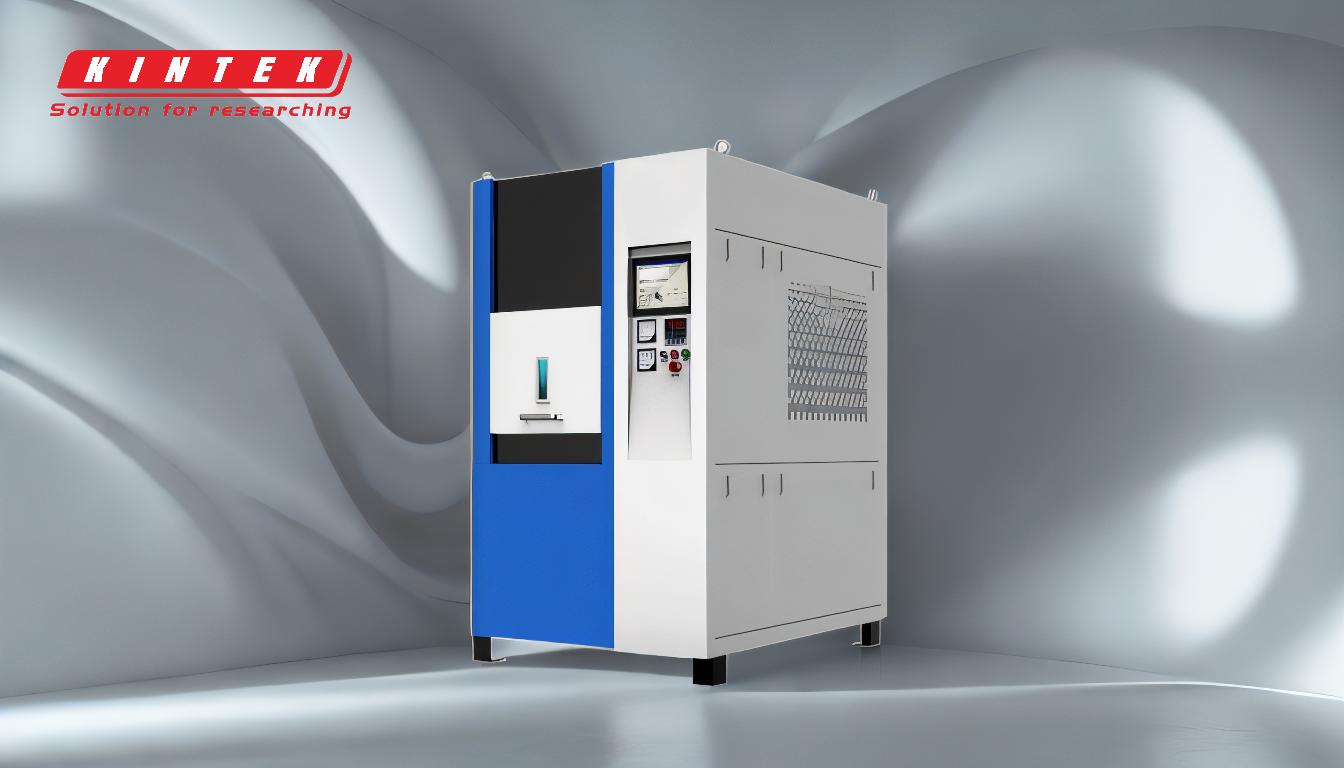
-
Impact of Gas Pressure on Ion Motion:
- At higher gas pressures, sputtered ions collide frequently with gas atoms, causing them to move diffusively. This results in a random walk before condensing on the substrate or chamber walls.
- At lower gas pressures, ions experience fewer collisions, leading to high-energy ballistic impacts on the substrate.
- This difference in ion motion affects the energy and directionality of the deposited particles, influencing film quality and uniformity.
-
Effect on Deposition Rate and Uniformity:
- Higher gas pressures reduce the kinetic energy of sputtered ions, leading to thermalized motion. This can improve film uniformity but may slow down the deposition rate.
- Lower gas pressures allow for faster deposition due to high-energy impacts but may result in less uniform films due to the directional nature of the ions.
-
Role of Gas Pressure in Sputtering Rate:
- The sputtering rate, defined as the number of monolayers per second sputtered from the target, is influenced by gas pressure.
- The sputtering rate depends on factors like sputter yield (S), molar weight of the target (M), material density (p), and ion current density (j), as described by the equation:
[ \text{Sputtering rate} = \frac{MSj}{pN_A e} ] where (N_A) is Avogadro's number and (e) is the electron charge. - Gas pressure indirectly affects these variables by altering ion energy and collision frequency.
-
Influence on Film Quality and Surface Mobility:
- Higher gas pressures can enhance surface mobility of deposited atoms, leading to better film quality and coverage.
- Lower gas pressures may result in films with higher residual stress or defects due to the high-energy impacts.
-
Trade-offs in Process Control:
- Adjusting gas pressure allows for a balance between deposition rate and film quality.
- For applications requiring uniform films, higher gas pressures are preferred, while faster deposition rates may necessitate lower gas pressures.
-
Interaction with Other Sputtering Parameters:
- Gas pressure interacts with other factors like ion energy, target material mass, and angle of incidence to determine the sputtering yield.
- The sputtering yield, or the number of target atoms ejected per incident ion, varies with gas pressure and influences the overall efficiency of the process.
-
Practical Considerations for Equipment and Consumables:
- For equipment purchasers, understanding the effect of gas pressure is crucial for selecting systems that offer precise pressure control.
- Consumables, such as target materials, must be chosen based on their compatibility with the desired gas pressure range to achieve optimal sputtering performance.
By carefully controlling gas pressure, users can tailor the sputtering process to meet specific requirements for film thickness, uniformity, and quality, making it a critical parameter in thin film deposition applications.
Summary Table:
Aspect | High Gas Pressure | Low Gas Pressure |
---|---|---|
Ion Motion | Diffusive, random walk | Ballistic, high-energy impacts |
Film Uniformity | Improved uniformity | Potentially less uniform |
Deposition Rate | Slower due to thermalized motion | Faster due to high-energy impacts |
Film Quality | Enhanced surface mobility, better coverage | Higher residual stress or defects |
Application Preference | Uniform films | Faster deposition rates |
Need help optimizing your sputtering process? Contact our experts today for tailored solutions!