The sintering temperature of zirconia significantly impacts its microstructure and properties. Optimal sintering occurs around 1500℃, maximizing strength and stability. Deviations of 150℃ above or below this temperature can lead to grain growth, reduced strength, and other adverse effects such as cracking, uncontrolled transformation, and decreased translucency. Adhering to the manufacturer’s recommended sintering schedule is crucial to achieving the desired physical, mechanical, and aesthetic properties of zirconia.
Key Points Explained:
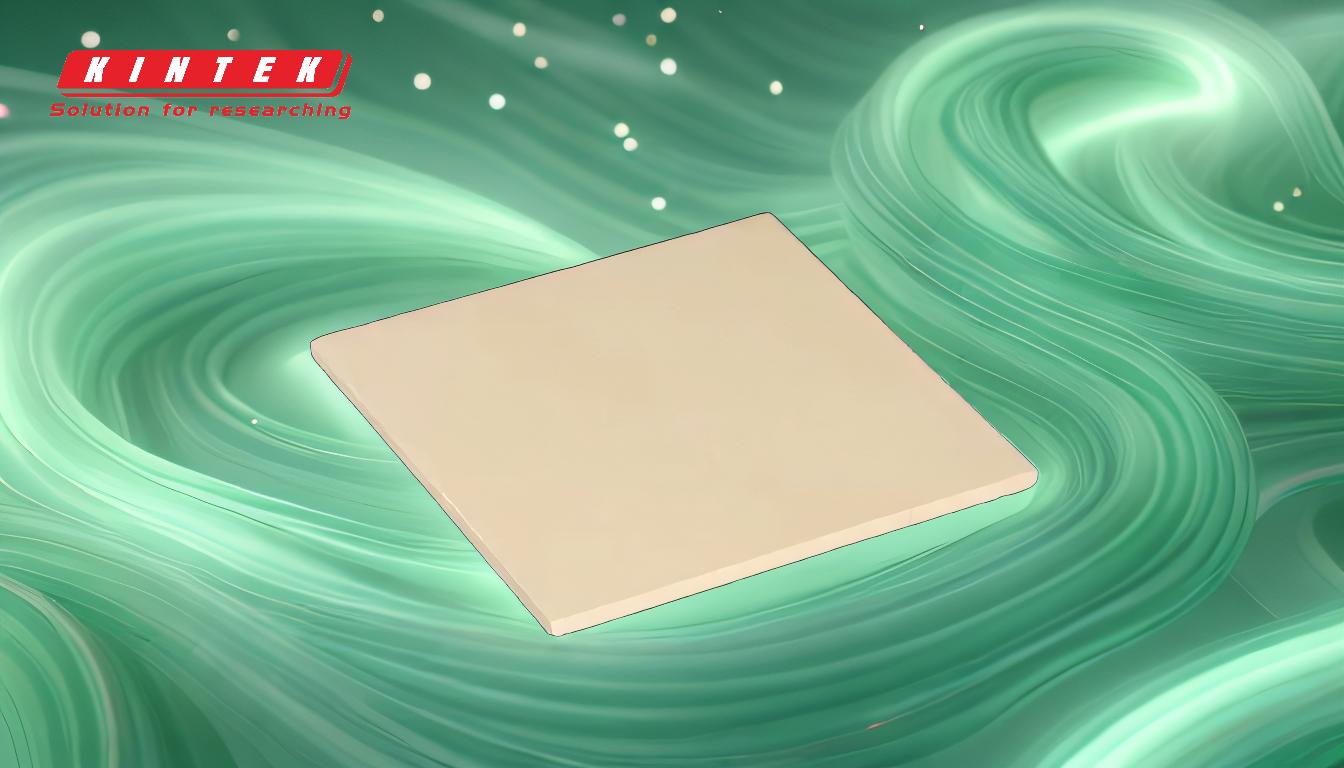
-
Optimal Sintering Temperature:
- 1500℃: Recent studies indicate that sintering zirconia at approximately 1500℃ maximizes its strength. This temperature is considered optimal for achieving a balance between mechanical properties and stability.
- Deviation Effects: Deviating by just 150℃ above or below this temperature can significantly reduce the strength of zirconia. This reduction is primarily due to grain growth, which negatively impacts the material's structural integrity.
-
Microstructural Changes:
- Grain Size and Pore Size: The sintering process directly affects the grain size and pore size within the zirconia microstructure. Optimal sintering conditions lead to a fine and uniform grain structure, which enhances the material's strength and durability.
- Grain Boundary Shape and Distribution: Proper sintering also influences the shape and distribution of grain boundaries. Well-defined grain boundaries contribute to the overall stability and mechanical performance of zirconia.
-
Adverse Effects of High Temperatures:
- Lowered Stability: Sintering at excessively high temperatures can compromise the stability of zirconia, making it more prone to uncontrolled phase transformations.
- Uncontrolled Transformation: High temperatures can induce uncontrolled transformations in the zirconia structure, leading to defects and reduced performance.
- Cracking: Excessive sintering temperatures increase the risk of cracking, which can severely compromise the material's integrity and longevity.
- Reduced Translucency: High sintering temperatures can also diminish the translucency of zirconia, affecting its aesthetic properties. This is particularly important in applications where appearance is a critical factor.
-
Importance of Manufacturer’s Recommendations:
- Firing Schedule: Adhering to the manufacturer’s recommended firing schedule is essential for achieving the ideal physical, mechanical, and aesthetic properties of zirconia. This schedule is designed to optimize the sintering process and ensure consistent quality.
- Consistency and Quality: Following the recommended sintering parameters helps maintain consistency in the material's properties and ensures high-quality outcomes. Deviations from these guidelines can lead to suboptimal results and potential failures in application.
In summary, the sintering temperature of zirconia is a critical factor that influences its microstructure and properties. Optimal sintering at around 1500℃ ensures maximum strength and stability, while deviations can lead to adverse effects such as grain growth, cracking, and reduced translucency. Adhering to the manufacturer’s recommended sintering schedule is essential for achieving the desired performance and aesthetic qualities in zirconia products.
Summary Table:
Key Aspect | Details |
---|---|
Optimal Sintering Temperature | 1500℃ maximizes strength and stability. |
Deviation Effects | ±150℃ can cause grain growth, reduced strength, cracking, and poor aesthetics. |
Microstructural Changes | Fine grain structure, uniform pores, and well-defined grain boundaries. |
Adverse Effects of High Temperatures | Uncontrolled transformations, cracking, and reduced translucency. |
Manufacturer’s Recommendations | Follow recommended firing schedules for consistent quality and performance. |
Ensure your zirconia achieves optimal strength and aesthetics—contact our experts today for guidance!