Electron beam evaporation is a sophisticated physical vapor deposition (PVD) technique used for thin film deposition. It involves using a high-energy electron beam to heat and evaporate a target material within a vacuum environment. The process begins with heating a tungsten filament to emit electrons, which are then accelerated and focused into a beam using a magnetic field. This electron beam strikes the target material in a water-cooled crucible, transferring kinetic energy into thermal energy, causing the material to evaporate. The vaporized material then condenses onto a substrate, forming a thin film. This method is highly efficient, capable of handling high evaporation temperatures, and can be enhanced with reactive gases to deposit non-metallic films.
Key Points Explained:
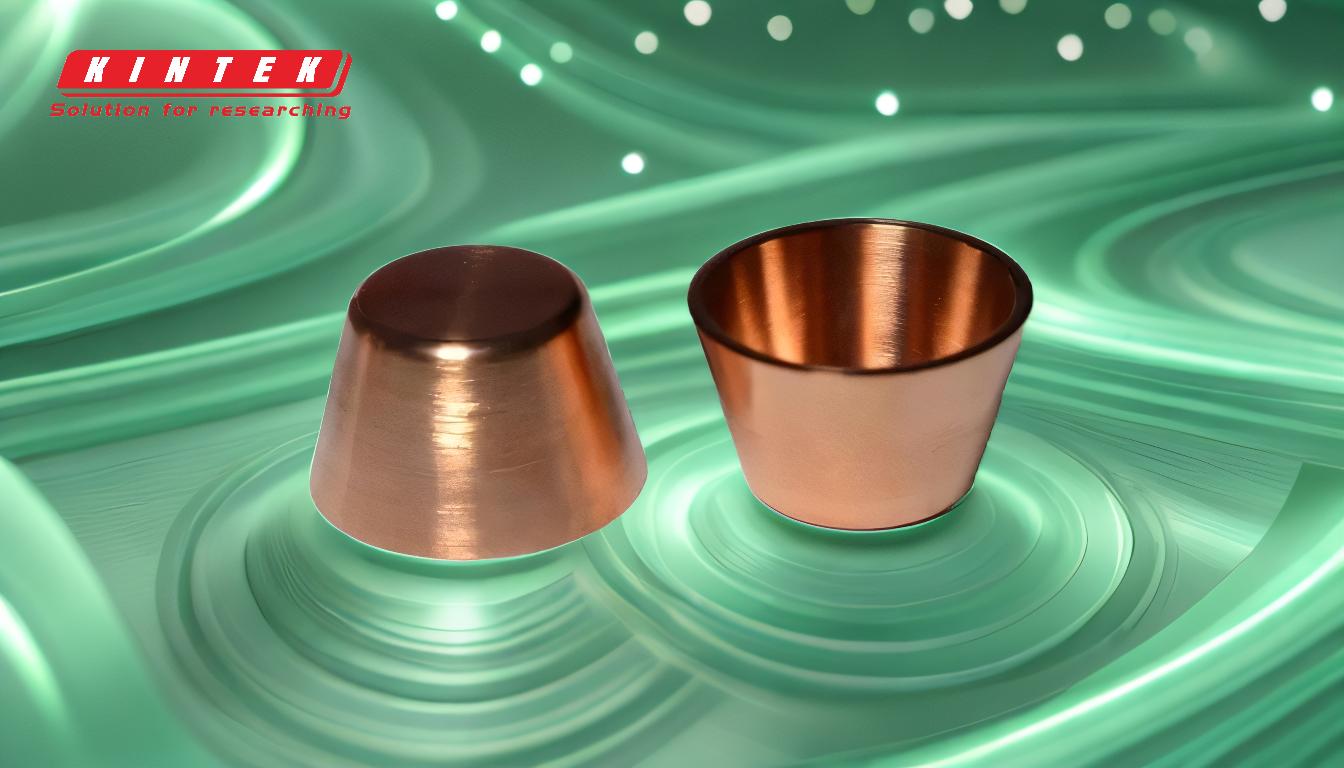
-
Vacuum Environment:
- The electron beam evaporation process occurs within a high vacuum chamber. This environment is crucial as it minimizes contamination and allows the vaporized material to travel unimpeded to the substrate, ensuring a pure and uniform thin film deposition.
-
Electron Emission:
- A tungsten filament is heated by passing an electric current through it, typically between five and ten kV. This heating causes thermionic emission, where electrons are emitted from the filament due to the high temperature.
-
Electron Beam Formation:
- The emitted electrons are accelerated by a high voltage and focused into a concentrated beam using a magnetic field. This focused electron beam is directed towards the target material contained within a water-cooled crucible.
-
Energy Transfer and Evaporation:
- When the high-energy electron beam strikes the target material, the kinetic energy of the electrons is converted into thermal energy. This rapid heating causes the material to evaporate or sublimate, turning it into a vapor phase.
-
Material Deposition:
- The vaporized material disperses within the vacuum chamber and condenses onto a substrate placed within the chamber. This results in the formation of a thin film on the substrate. The thickness and uniformity of the film can be controlled by adjusting parameters such as the electron beam intensity, duration, and substrate position.
-
Use of Reactive Gases:
- In some cases, reactive gases like oxygen or nitrogen can be introduced into the vacuum chamber. These gases react with the vaporized material to form non-metallic compounds, which then deposit onto the substrate. This allows for the deposition of oxide or nitride films, expanding the range of materials that can be deposited using this technique.
-
Advantages of Electron Beam Evaporation:
- High Purity: The vacuum environment and precise control over the electron beam ensure high-purity thin films.
- High Evaporation Temperatures: This method can handle materials with very high melting points, which are difficult to evaporate using other techniques.
- Versatility: It can be used to deposit a wide range of materials, including metals, alloys, and compounds.
- Controlled Deposition: The process allows for precise control over film thickness and uniformity.
-
Applications:
- Optical Coatings: Used in the production of anti-reflective coatings, mirrors, and filters.
- Semiconductor Devices: Essential for depositing thin films in the fabrication of integrated circuits and other semiconductor components.
- Decorative Coatings: Applied in the automotive and jewelry industries for aesthetic purposes.
- Protective Coatings: Used to enhance the durability and resistance of various materials.
In summary, electron beam evaporation is a highly effective and versatile method for depositing thin films with high precision and purity. Its ability to handle high-temperature materials and incorporate reactive gases makes it suitable for a wide range of industrial and scientific applications.
Summary Table:
Key Aspect | Details |
---|---|
Process | High-energy electron beam evaporates target material in a vacuum chamber. |
Key Components | Tungsten filament, magnetic field, water-cooled crucible, and substrate. |
Advantages | High purity, high evaporation temperatures, versatility, controlled deposition. |
Applications | Optical coatings, semiconductor devices, decorative coatings, protective coatings. |
Reactive Gases | Oxygen or nitrogen can be used to deposit non-metallic films. |
Discover how electron beam evaporation can elevate your thin film processes—contact our experts today!