Biomass energy efficiency varies depending on the type of biomass, conversion technology, and application. Biomass is a renewable energy source derived from organic materials like wood, agricultural residues, and waste. Its energy efficiency is influenced by factors such as moisture content, combustion or conversion technology, and the end-use application. For example, direct combustion of dry biomass can achieve efficiencies of 20-30% for electricity generation and up to 90% for thermal applications. Advanced technologies like gasification and pyrolysis can improve efficiency by converting biomass into higher-energy-density fuels. Overall, biomass offers a sustainable energy option with relatively low emissions, but its efficiency depends on proper management of feedstock and conversion processes.
Key Points Explained:
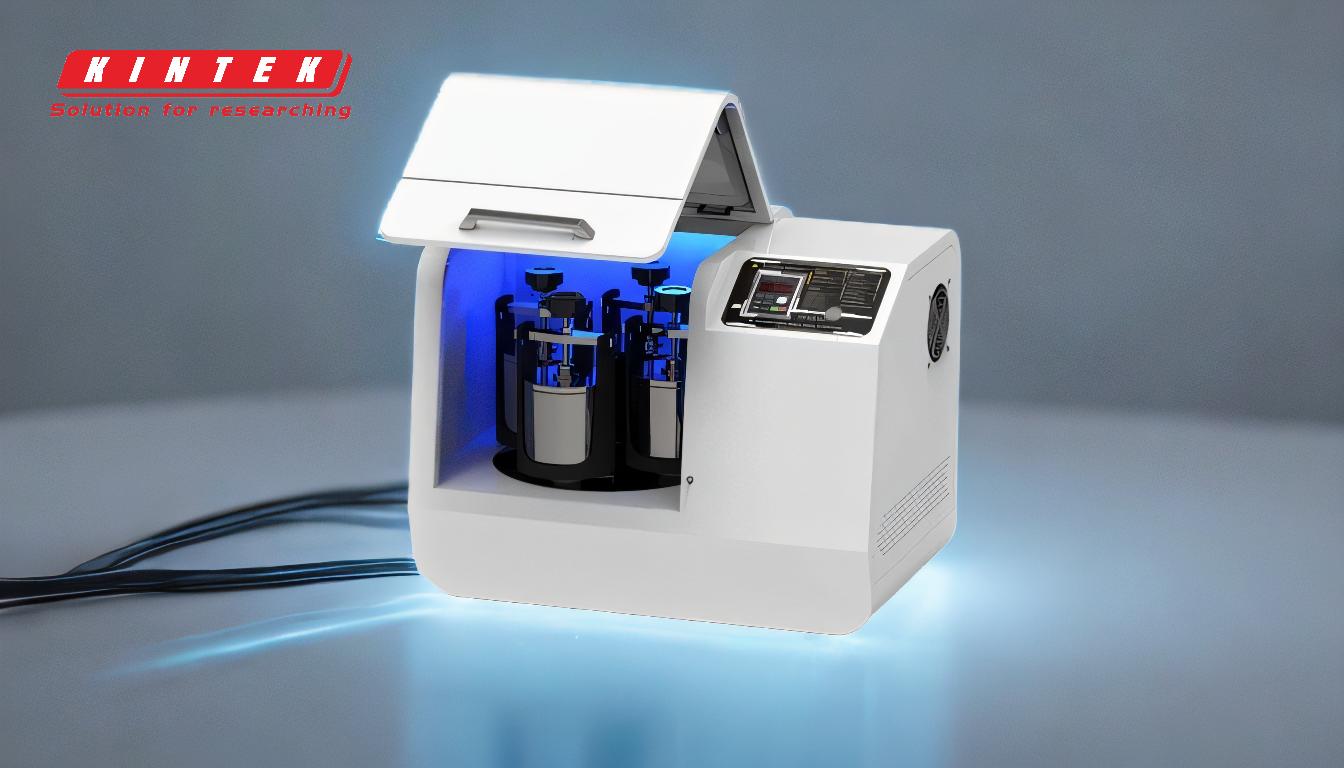
-
Definition and Sources of Biomass:
- Biomass refers to organic materials derived from plants, animals, and waste. Common sources include wood, agricultural residues, algae, and municipal solid waste.
- It is considered renewable because it can be replenished through natural processes or human activities like farming and forestry.
-
Energy Efficiency of Biomass:
- The energy efficiency of biomass depends on the conversion technology and the end-use application.
- Direct combustion, the most common method, typically achieves 20-30% efficiency for electricity generation and up to 90% for thermal applications like heating.
- Advanced technologies, such as gasification and pyrolysis, can improve efficiency by converting biomass into syngas or bio-oil, which have higher energy densities and can be used in more efficient systems.
-
Factors Affecting Biomass Energy Efficiency:
- Moisture Content: High moisture content reduces the energy efficiency of biomass because energy is wasted in evaporating water. Dry biomass is more efficient for combustion and conversion processes.
- Temperature and Residence Time: In pyrolysis and gasification, optimal temperature and residence time are critical for maximizing energy output and producing high-quality end products.
- Feedstock Type: Different biomass materials have varying energy contents. For example, woody biomass generally has a higher energy content than agricultural residues.
-
Environmental Impact and Sustainability:
- Biomass is considered a low-carbon energy source because the carbon dioxide released during combustion is offset by the carbon absorbed during the growth of the biomass feedstock.
- Proper management of biomass resources is essential to ensure sustainability and minimize environmental impacts, such as deforestation or soil degradation.
-
Applications of Biomass Energy:
- Biomass is used for electricity generation, heating, and as a feedstock for biofuels like ethanol and biodiesel.
- In developing countries, biomass is a primary energy source for cooking and heating, while in developed countries, it is increasingly used for renewable energy production.
-
Challenges and Future Prospects:
- Challenges include the variability of biomass feedstock, the need for efficient conversion technologies, and competition with food production for agricultural land.
- Ongoing research and technological advancements aim to improve the efficiency and sustainability of biomass energy systems, making it a more viable option for the global energy transition.
In summary, biomass energy efficiency is influenced by multiple factors, including feedstock type, moisture content, and conversion technology. While it offers a sustainable and renewable energy option, proper management and technological advancements are crucial for maximizing its potential and minimizing environmental impacts.
Summary Table:
Factor | Impact on Efficiency |
---|---|
Moisture Content | High moisture reduces efficiency; dry biomass is more efficient. |
Conversion Technology | Advanced methods like gasification and pyrolysis improve energy output. |
Feedstock Type | Woody biomass has higher energy content than agricultural residues. |
Temperature/Time | Optimal conditions in pyrolysis and gasification maximize energy output. |
Application | Efficiency ranges: 20-30% for electricity, up to 90% for thermal applications. |
Discover how to maximize biomass energy efficiency for your projects—contact our experts today!