The frequency of an induction furnace varies significantly depending on the application, material being melted, furnace capacity, and desired melting speed. It typically ranges from utility frequency (50 or 60 Hz) to 400 kHz or higher. Lower frequencies are used for larger volumes and deeper penetration into the metal, while higher frequencies are preferred for smaller volumes and faster melting due to their shallow penetration depth. The frequency can be adjusted by modifying the coil and compensating capacitor, ensuring optimal performance based on specific requirements such as stirring effect, noise, and efficiency.
Key Points Explained:
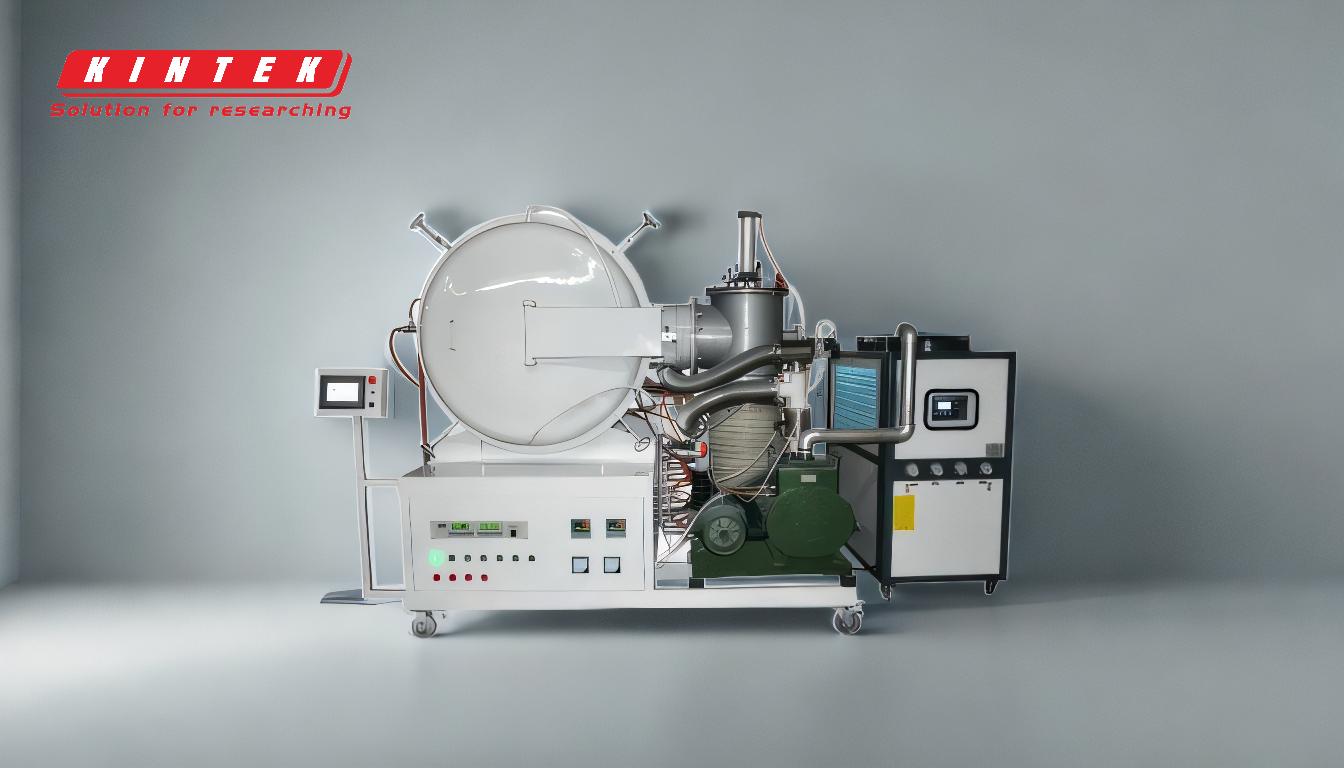
-
Range of Operating Frequencies:
- Induction furnaces operate across a wide frequency range, from utility frequency (50 Hz or 60 Hz) to 400 kHz or higher.
- The choice of frequency depends on factors like the type of material, furnace capacity, and desired melting speed.
-
Frequency Selection Based on Material and Volume:
- Smaller volumes of melts typically require higher frequencies (e.g., 400 kHz) due to the skin depth effect, which ensures efficient heating with shallow penetration.
- Larger volumes benefit from lower frequencies (e.g., 50 Hz or 60 Hz), which allow deeper penetration and can generate stirring or turbulence in the metal.
-
Skin Depth Effect:
- Skin depth refers to how deeply an alternating current can penetrate a conductor.
- Higher frequencies result in shallower penetration, making them ideal for smaller volumes and faster heating.
- Lower frequencies penetrate deeper, suitable for larger volumes and creating a stirring effect in the molten metal.
-
Adjustability of Frequency:
- The frequency of an induction furnace can be designed or adjusted by changing the coil and compensating capacitor.
- This flexibility allows customization based on factors like melting material, quantity, desired stirring effect, noise levels, and melting efficiency.
-
Applications and Benefits of Different Frequencies:
-
High Frequencies (e.g., 400 kHz):
- Ideal for small-scale melting and precise heating.
- Provide uniform temperature distribution and faster melting times.
-
Low Frequencies (e.g., 50 Hz or 60 Hz):
- Suitable for large-scale melting and industrial applications.
- Enable deeper penetration and magnetic stirring, improving composition uniformity and scum removal.
-
High Frequencies (e.g., 400 kHz):
-
Frequency and Melting Efficiency:
- Higher frequencies are more energy-efficient for small volumes, as they reduce heat loss and ensure rapid heating.
- Lower frequencies are better for larger volumes, as they provide consistent heating and stirring, reducing the risk of uneven melting.
-
Practical Considerations:
- The frequency choice impacts the design of the furnace, including the inductor, capacitor, and power supply.
- Modern induction furnaces often feature automatic frequency scanning and adjustment, ensuring smooth and stable operation.
-
Examples of Frequency Use in Real-World Applications:
- Small-scale laboratory furnaces often operate at higher frequencies (e.g., 400 kHz) for precise melting of small quantities.
- Industrial-scale furnaces for steel or aluminum production typically use lower frequencies (e.g., 50 Hz or 60 Hz) for bulk melting and stirring.
-
Frequency and Furnace Design:
- The frequency influences the design of the furnace's power supply, inductor, and cooling systems.
- Advanced induction furnaces use solid-state IGBT technology for frequency conversion, ensuring precise control and energy efficiency.
-
Frequency and Environmental Impact:
- Higher frequencies are often more energy-efficient and environmentally friendly for small-scale operations.
- Lower frequencies, while requiring more energy, are essential for large-scale industrial processes, where their benefits outweigh the energy costs.
By understanding these key points, a purchaser can make informed decisions about the frequency requirements of an induction furnace based on their specific needs, such as the type of material, volume, and desired operational efficiency.
Summary Table:
Frequency Range | Applications | Benefits |
---|---|---|
50 Hz - 60 Hz | Large-scale melting, industrial processes | Deep penetration, stirring effect, uniform composition |
400 kHz | Small-scale melting, precise heating | Shallow penetration, faster melting, energy efficiency |
Adjustable | Custom applications | Tailored performance for material, volume, and efficiency |
Need help selecting the right induction furnace frequency? Contact our experts today for personalized guidance!