PVD stands for Physical Vapor Deposition, a widely used industrial process for coating materials at an atomic level. It is a vaporization technique that involves transferring material in a vacuum environment, often used as an alternative to electroplating. The process consists of four key stages: evaporation, transportation, reaction, and deposition. PVD is employed in various industries to enhance the durability, wear resistance, and aesthetic qualities of surfaces. It is particularly valued for its ability to produce thin, uniform, and high-performance coatings on a variety of substrates.
Key Points Explained:
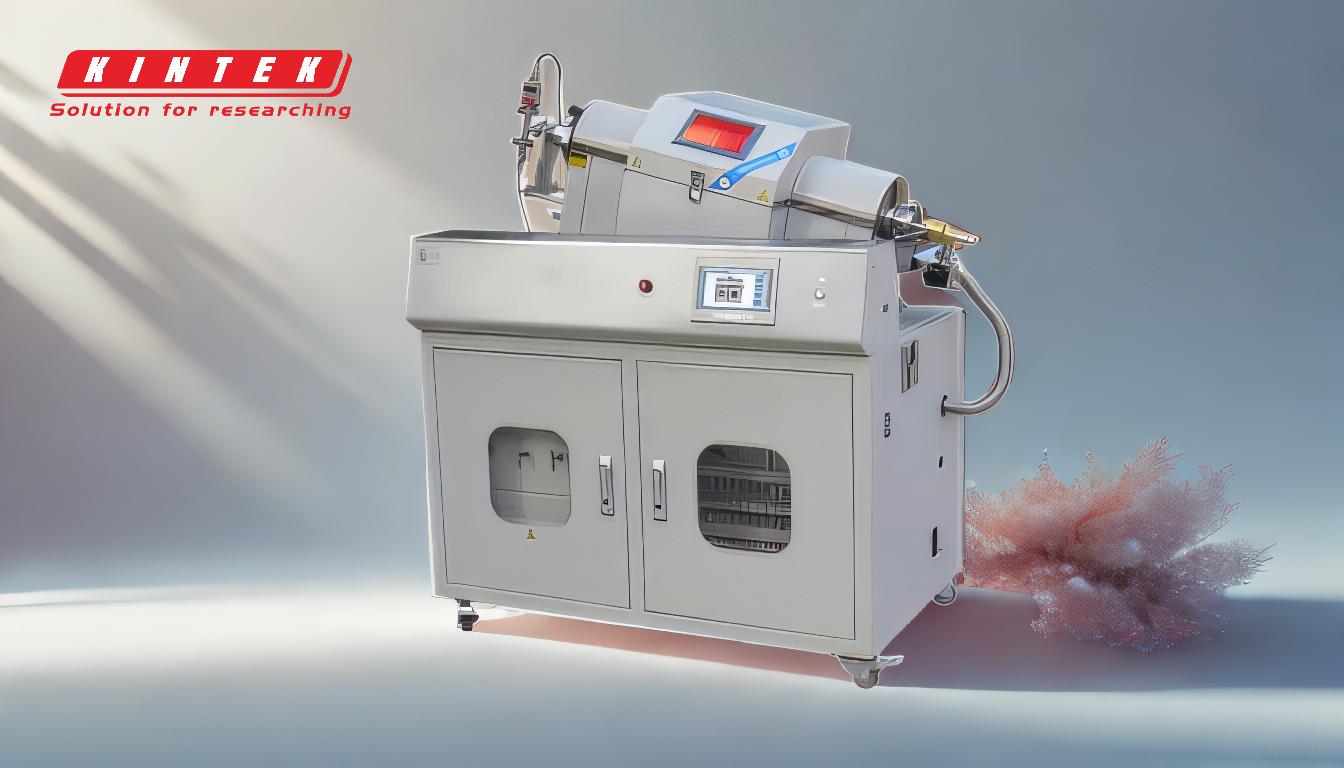
-
Definition of PVD:
- PVD stands for Physical Vapor Deposition. It is a process where materials are vaporized in a vacuum and then deposited onto a substrate to form a thin, uniform coating. This technique is used to improve surface properties such as hardness, wear resistance, and corrosion resistance.
-
Stages of the PVD Process:
- Evaporation: The target material is vaporized using methods like sputtering or thermal evaporation. This step involves converting the solid material into a vapor state.
- Transportation: The vaporized material is transported through a vacuum or low-pressure environment to the substrate.
- Reaction: In some cases, the vaporized material reacts with gases (e.g., nitrogen or oxygen) introduced into the chamber to form compounds like nitrides or oxides.
- Deposition: The vaporized material condenses onto the substrate, forming a thin, adherent coating.
-
Applications of PVD:
- PVD is used in industries such as aerospace, automotive, medical devices, and electronics. It is commonly applied to tools, components, and decorative finishes to enhance performance and longevity.
-
Advantages of PVD:
- Provides high-quality, durable coatings with excellent adhesion.
- Environmentally friendly compared to electroplating, as it produces fewer hazardous byproducts.
- Allows for precise control over coating thickness and composition.
-
Comparison to Electroplating:
- PVD is considered a superior alternative to electroplating due to its ability to produce thinner, more uniform coatings with better mechanical and chemical properties. It is also more environmentally sustainable.
By understanding the full form and process of PVD, industries can make informed decisions about its application to improve product performance and durability.
Summary Table:
Aspect | Details |
---|---|
Definition | PVD stands for Physical Vapor Deposition, a vacuum-based coating process. |
Process Stages | 1. Evaporation |
- Transportation
- Reaction
- Deposition | | Applications | Aerospace, automotive, medical devices, electronics, and decorative finishes. | | Advantages | - High-quality, durable coatings
- Environmentally friendly
- Precise control | | Comparison | Superior to electroplating for thinner, uniform, and sustainable coatings. |
Enhance your product's performance with PVD coatings—contact us today to learn more!