A muffle furnace is a specialized high-temperature heating device designed to protect materials from oxidation and contamination while enabling precise temperature control. It is widely used in laboratories, industrial settings, and research facilities for applications such as ashing, annealing, calcination, sintering, and heat treatment. The furnace operates by isolating the material being heated within a chamber, ensuring uniform heat distribution and preventing exposure to external contaminants. Its versatility makes it indispensable in fields like materials science, metallurgy, ceramics, and pharmaceuticals, where high-temperature processes are required for analysis, synthesis, or quality control.
Key Points Explained:
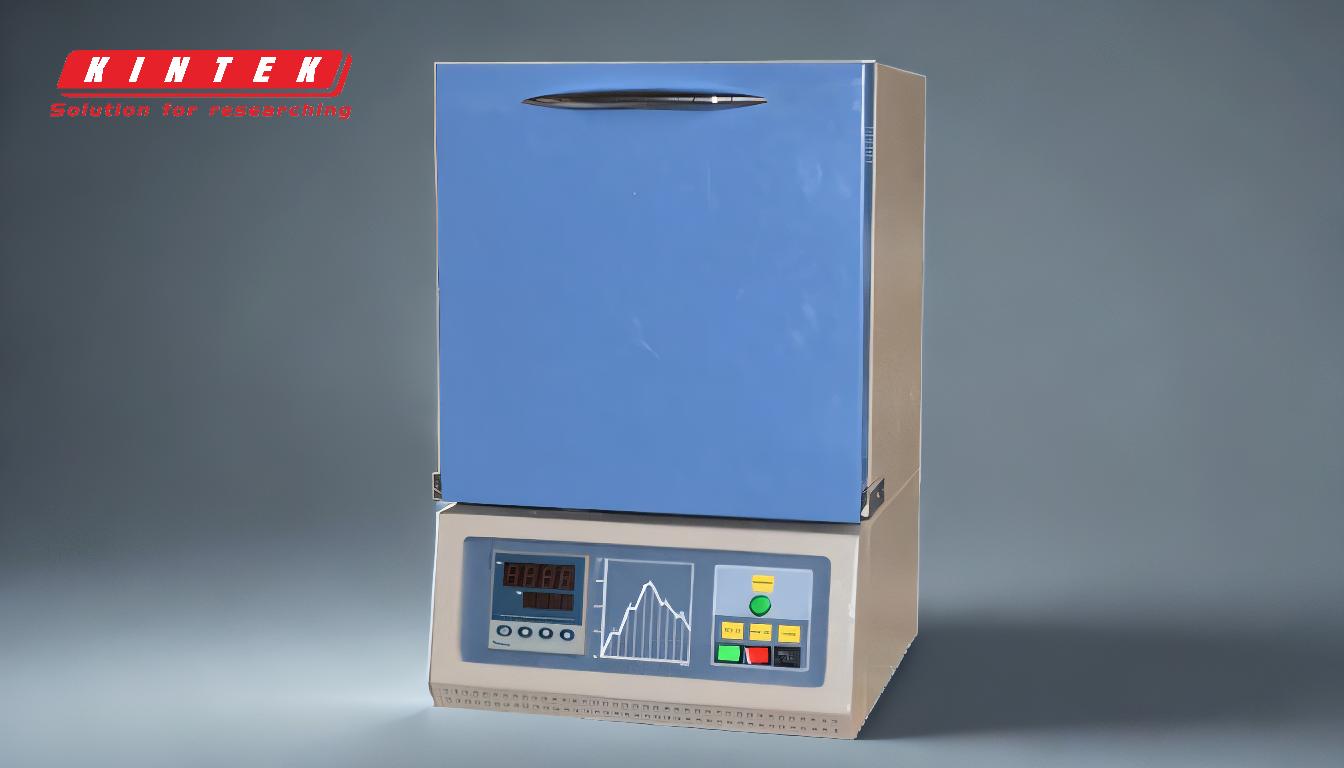
-
Primary Function of a Muffle Furnace:
- A muffle furnace is designed to heat materials to high temperatures while shielding them from oxidation, contamination, and direct exposure to flames or combustion gases. This is achieved by enclosing the material in a separate chamber (the muffle), which ensures a controlled environment.
-
Applications of a Muffle Furnace:
- Ashing: Used to determine the amount of non-combustible and non-volatile content in a sample, commonly in environmental and food testing.
- Annealing: A heat treatment process to alter the physical and chemical properties of materials, such as metals and glass, to reduce hardness and improve ductility.
- Calcination: Heating materials like ores or ceramics to high temperatures to induce thermal decomposition or phase transitions.
- Sintering: Fusing powdered materials into a solid mass without melting, often used in powder metallurgy and ceramics.
- Heat Treatment: Processes like hardening, tempering, and stress relief for metals and alloys.
- Brazing and Soldering: Joining metals using filler materials at high temperatures.
- Glass Fusing and Enamel Coating: Creating glass art or applying enamel coatings to metals.
- Loss on Ignition Analysis: Measuring the mass loss of a sample when heated to determine volatile content.
- Thermogravimetric Analysis: Studying material properties as a function of temperature.
-
Design and Features:
- High-Temperature Capability: Muffle furnaces can reach temperatures up to 1800°C, making them suitable for demanding applications.
- Controlled Atmosphere: Some models allow operation under inert or reducing atmospheres to prevent oxidation or enable specific chemical reactions.
- Uniform Heating: Advanced designs ensure even heat distribution, critical for consistent results in experiments and industrial processes.
- Safety Features: Includes over-temperature protection, cooling systems, and exhaust mechanisms to vent gases safely.
-
Industries and Fields of Use:
- Laboratories: For research, quality control, and material analysis in academic, pharmaceutical, and industrial labs.
- Metallurgy: For heat treatment, sintering, and brazing of metals and alloys.
- Ceramics and Glass: For firing, co-firing, and glass formation.
- Food and Pharmaceuticals: For ash content determination, drug inspection, and medical sample pretreatment.
- Environmental Testing: For water quality analysis and ash melting point determination.
- Nuclear Industry: For nuclear fuel disposal and materials research.
-
Advantages of Using a Muffle Furnace:
- Precision: Offers precise temperature control and uniform heating, essential for reproducible results.
- Versatility: Suitable for a wide range of applications across multiple industries.
- Safety: Protects users from exposure to harmful fumes and gases, often eliminating the need for a fume hood.
- Durability: Built with high-quality materials like ceramic chambers and high-temperature alloys for long-term reliability.
-
Choosing the Right Muffle Furnace:
- Consider temperature range, chamber size, heating rate, and atmosphere control based on your specific application.
- Evaluate safety features, energy efficiency, and ease of maintenance.
- Ensure compatibility with your laboratory or industrial setup.
In summary, a muffle furnace is an essential tool for high-temperature processes, offering precision, safety, and versatility. Its ability to protect materials from contamination and oxidation makes it invaluable in research, manufacturing, and quality control across diverse industries.
Summary Table:
Aspect | Details |
---|---|
Primary Function | Heats materials while shielding them from oxidation and contamination. |
Key Applications | Ashing, annealing, calcination, sintering, heat treatment, and more. |
Temperature Range | Up to 1800°C for demanding applications. |
Industries Served | Laboratories, metallurgy, ceramics, pharmaceuticals, and environmental testing. |
Advantages | Precision, versatility, safety, and durability. |
Discover how a muffle furnace can enhance your lab or industrial processes—contact us today for expert advice!