A rotary tablet press is a highly efficient machine designed for the mass production of tablets, widely used in industries such as pharmaceuticals, nutraceuticals, confectionery, and veterinary medicine. Its primary function is to compress powdered or granular materials into tablets of uniform size, weight, and hardness. The machine operates by filling die cavities with material, compressing it using upper and lower punches, and ejecting the finished tablets. Rotary tablet presses offer advantages such as high production output (up to 1,000,000+ tablets per hour), precise control over tablet properties, and compatibility with modern monitoring systems. They are available in single-sided and double-sided configurations, each suited for specific production needs.
Key Points Explained:
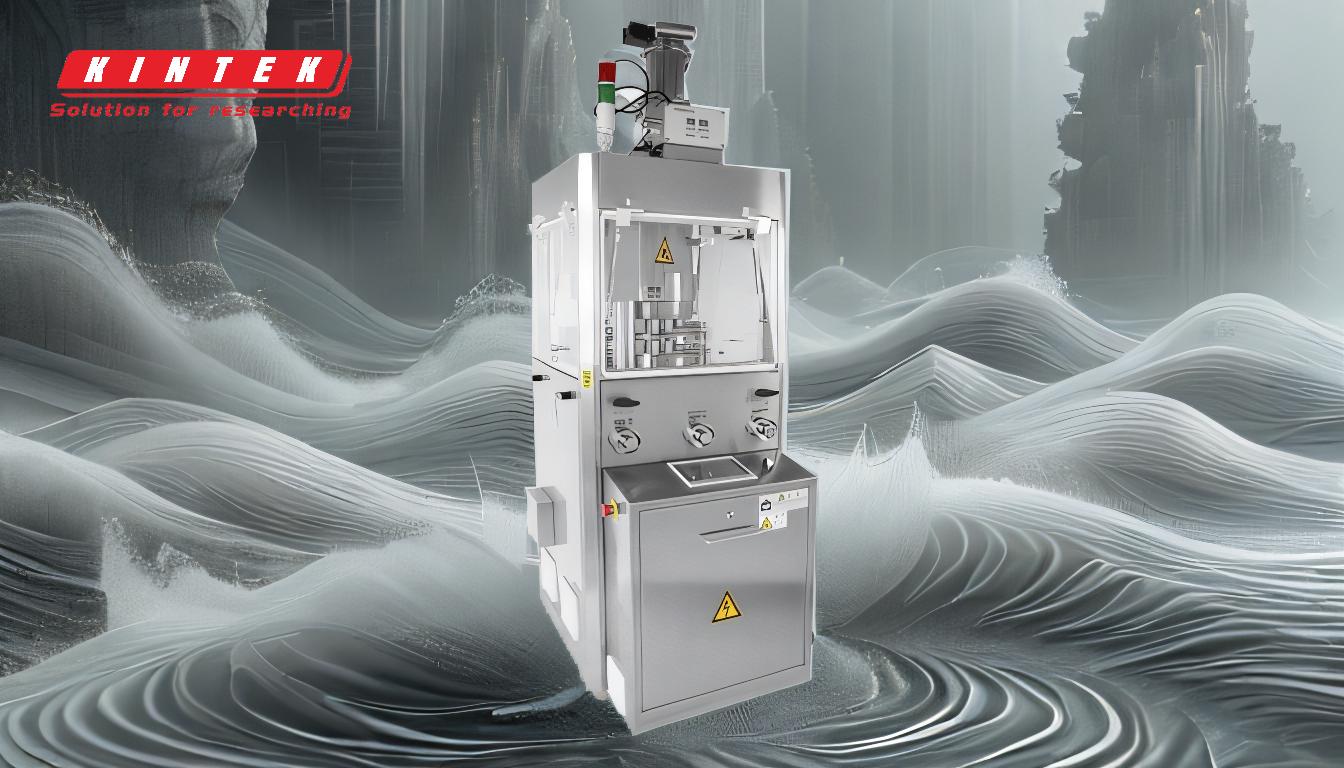
-
Core Function of a Rotary Tablet Press:
- The primary function of a rotary tablet press is to compress powdered or granular materials into tablets. This is achieved through a series of steps:
- Filling: The die cavity is filled with the material to be compressed.
- Compression: Upper and lower punches apply pressure to the material, forming it into a tablet.
- Ejection: The finished tablet is ejected from the die cavity.
- This process ensures the production of tablets with consistent size, weight, and hardness, which are critical for quality control in industries like pharmaceuticals.
- The primary function of a rotary tablet press is to compress powdered or granular materials into tablets. This is achieved through a series of steps:
-
Advantages of Rotary Tablet Presses:
- High Production Output: Rotary tablet presses can produce over 1,000,000 tablets per hour, making them ideal for large-scale manufacturing.
- Precision Control: These machines allow independent control of tablet weight, thickness, and hardness, ensuring uniformity.
- Cost Efficiency: Compared to single punch presses, rotary presses are more cost-effective for high-volume production.
- Remote Monitoring: Many rotary presses can interface with in-house network systems, enabling remote monitoring and control.
-
Types of Rotary Tablet Presses:
-
Single-sided Rotary Tablet Press:
- Uses a single set of punches and dies.
- Suitable for smaller-scale production or specialized applications.
- The process involves filling the die cavity, compressing the material, and ejecting the tablet.
-
Double-sided Rotary Tablet Press:
- Features two sets of punches and dies, allowing for higher production rates.
- Ideal for large-scale manufacturing where efficiency and speed are critical.
-
Single-sided Rotary Tablet Press:
-
Applications of Rotary Tablet Presses:
- Pharmaceutical Industry: Used to produce tablets for medications, ensuring precise dosing and uniformity.
- Nutraceuticals and Confectionery: Employed in the production of dietary supplements, vitamins, and candies.
- Veterinary Medicine: Used to create tablets for animal health products.
- Other Industries: Also utilized in the production of catalysts, ceramics, powdered metals, and other compressible materials.
-
Key Components and Mechanisms:
- Pre-compression Rollers: These provide initial compression to remove air trapped in the die cavity, ensuring better tablet quality.
- Main Compression Rollers: Apply the final compression force to form the finished tablets.
- Punches and Dies: The upper and lower punches work together with the die to shape and compress the material into tablets.
-
Comparison with Single Punch Presses:
- Rotary tablet presses are more efficient and suitable for high-volume production compared to single punch presses, which are better suited for small-scale or specialized applications.
- Single punch presses operate through a stamping process, where the upper punch exerts a hammer-like force to compress the material. This method is less efficient for large-scale production but offers simplicity and ease of use for smaller batches.
In summary, rotary tablet presses are indispensable in industries requiring high-volume, precise, and uniform tablet production. Their advanced features, such as independent control over tablet properties, high output, and remote monitoring capabilities, make them a preferred choice for modern manufacturing needs.
Summary Table:
Aspect | Details |
---|---|
Core Function | Compresses powdered/granular materials into uniform tablets. |
Key Steps | Filling, Compression, Ejection. |
Advantages | High output (1M+ tablets/hour), precise control, cost efficiency. |
Types | Single-sided (small-scale) and double-sided (large-scale). |
Applications | Pharmaceuticals, nutraceuticals, confectionery, veterinary medicine. |
Key Components | Pre-compression rollers, main compression rollers, punches, and dies. |
Comparison | More efficient than single punch presses for high-volume production. |
Ready to optimize your tablet production? Contact us today for expert guidance!