Sintering is a critical process in materials science and manufacturing, where powdered materials are compacted and heated below their melting points to form a solid, cohesive mass. This process is widely used across various industries due to its cost-effectiveness, energy efficiency, and ability to produce complex shapes with high precision. The primary function of a sintering furnace is to facilitate this process by providing controlled high temperatures and, in some cases, pressure and specific atmospheric conditions. Sintering is particularly valuable for materials with high melting points, such as metals and ceramics, and is extensively used in applications ranging from automotive components to 3D printing.
Key Points Explained:
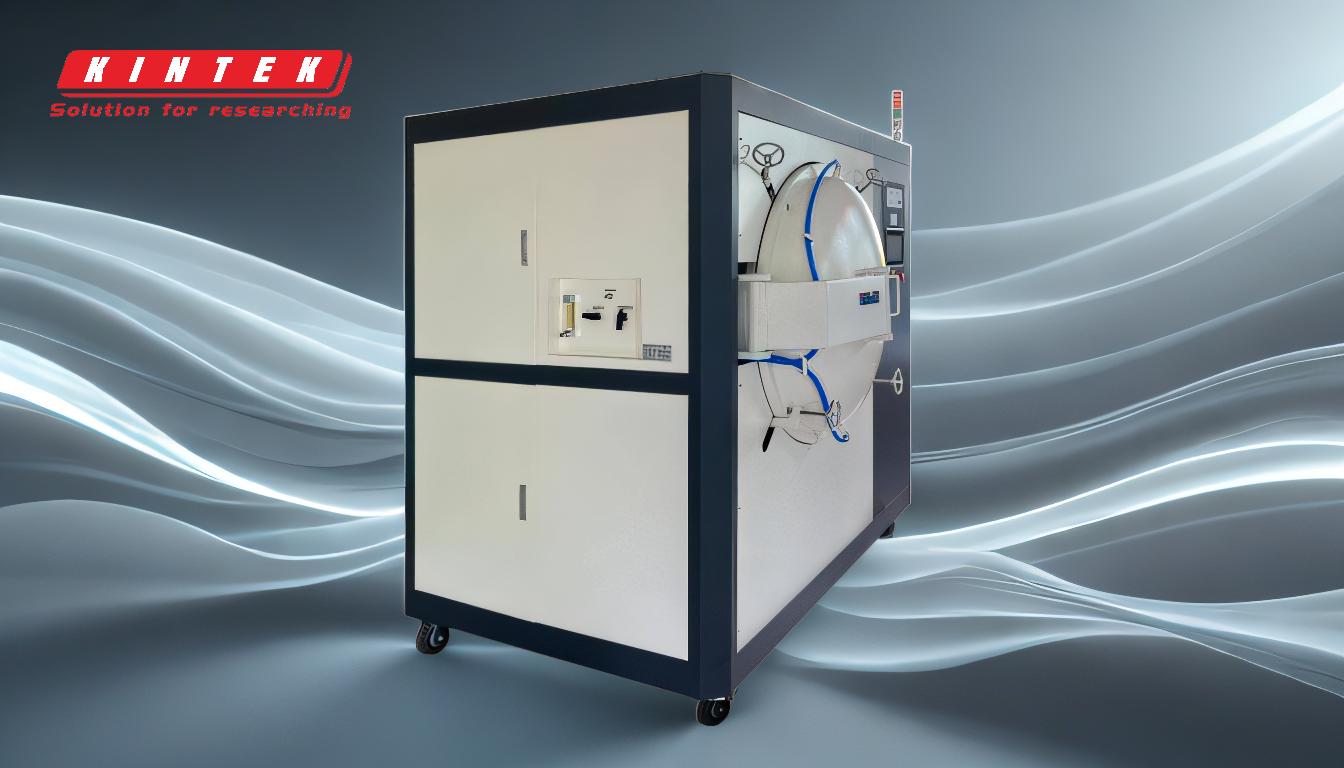
-
Definition and Purpose of Sintering:
- Sintering is a process that compacts and fuses powdered materials into a solid mass without melting them. This is achieved by heating the material below its melting point, allowing atomic diffusion to bond the particles together.
- The primary purpose of sintering is to create strong, dense, and complex parts from powdered materials, which is especially useful for metals and ceramics with high melting points.
-
Applications of Sintering:
- Sintering is used in a wide range of industries, including automotive, aerospace, electronics, and manufacturing. Common products include gears, bearings, pulleys, rotors, and electrical contacts.
- In 3D printing, sintering allows for the creation of custom metal shapes with high precision and consistency, while saving energy compared to traditional melting processes.
-
Types of Sintering Furnaces:
- Hot Press Sintering Furnace: This type of furnace combines high temperature and high pressure in a vacuum environment to sinter ceramic powders. It includes components like a furnace body, heater, pressure system, and vacuum system. The process involves loading the powder, evacuating the furnace, heating, applying pressure, and cooling.
- Atmosphere Sintering Furnace: This furnace controls the atmosphere (e.g., nitrogen, argon) to achieve sintering and hardening of ceramic materials. It includes heating devices, pressure mechanisms, sintering chambers, and gas control systems. The controlled atmosphere helps in material migration, grain boundary movement, pore elimination, and shrinkage, resulting in a dense and strong ceramic body.
-
Stages of the Sintering Process:
- Compaction: The first stage involves compressing the powdered material into a desired shape, resulting in a weak and oversize component.
- Thermal Fusion: The second stage involves heating the compacted shape to a temperature below the melting point of the material. This causes the particles to bond together through thermal fusion, expelling any binder material and forming a full-strength part.
-
Advantages of Sintering:
- Cost-Effectiveness: Sintering is a cost-effective method for producing complex parts, as it requires less energy compared to melting processes.
- Versatility: The process can be applied to a wide range of materials, including metals, ceramics, and composites.
- Improved Material Properties: Sintering reduces porosity, leading to stronger and more durable materials with enhanced properties.
-
Key Components and Mechanisms:
- Heating Elements: Essential for providing the high temperatures required for sintering.
- Pressure Systems: Used in hot press sintering to apply high pressure, aiding in the compaction and fusion of materials.
- Vacuum and Atmosphere Control: Critical for maintaining the desired environment, whether it be a vacuum or a specific gas atmosphere, to ensure proper sintering conditions.
-
Material Transformation During Sintering:
- The process involves the diffusion of atoms across particle boundaries, leading to the elimination of pores and the formation of a dense, solid structure.
- The final product has improved mechanical properties, such as increased strength, hardness, and wear resistance, due to the reduction in porosity and the formation of strong inter-particle bonds.
In conclusion, the sintering furnace plays a pivotal role in the sintering process by providing the necessary conditions for bonding powdered materials into solid, functional parts. Its applications are vast, and its advantages make it an indispensable tool in modern manufacturing and materials science.
Summary Table:
Aspect | Details |
---|---|
Primary Function | Provides controlled high temperatures, pressure, and atmospheric conditions for sintering. |
Applications | Automotive, aerospace, electronics, 3D printing, and more. |
Types of Furnaces | Hot Press Sintering Furnace, Atmosphere Sintering Furnace. |
Key Components | Heating elements, pressure systems, vacuum/atmosphere control. |
Advantages | Cost-effective, versatile, improves material properties like strength and durability. |
Process Stages | Compaction and thermal fusion. |
Learn how a sintering furnace can optimize your manufacturing process—contact our experts today!