Ceramics are typically fired in specialized furnaces designed to withstand high temperatures and provide controlled heating environments. One of the most common types of furnaces used for firing ceramics is the muffle furnace. This furnace is specifically designed to protect the ceramic pieces from direct exposure to flames and combustion gases, ensuring a clean and consistent firing process. The construction of a muffle furnace includes features like a stainless steel glory hole, a double insulation ceramic liner, and a vacuum-formed polycrystalline mullite fiber furnace hearth, which contribute to its efficiency and durability. These furnaces are essential for achieving the desired properties in ceramics, such as strength, durability, and aesthetic finish.
Key Points Explained:
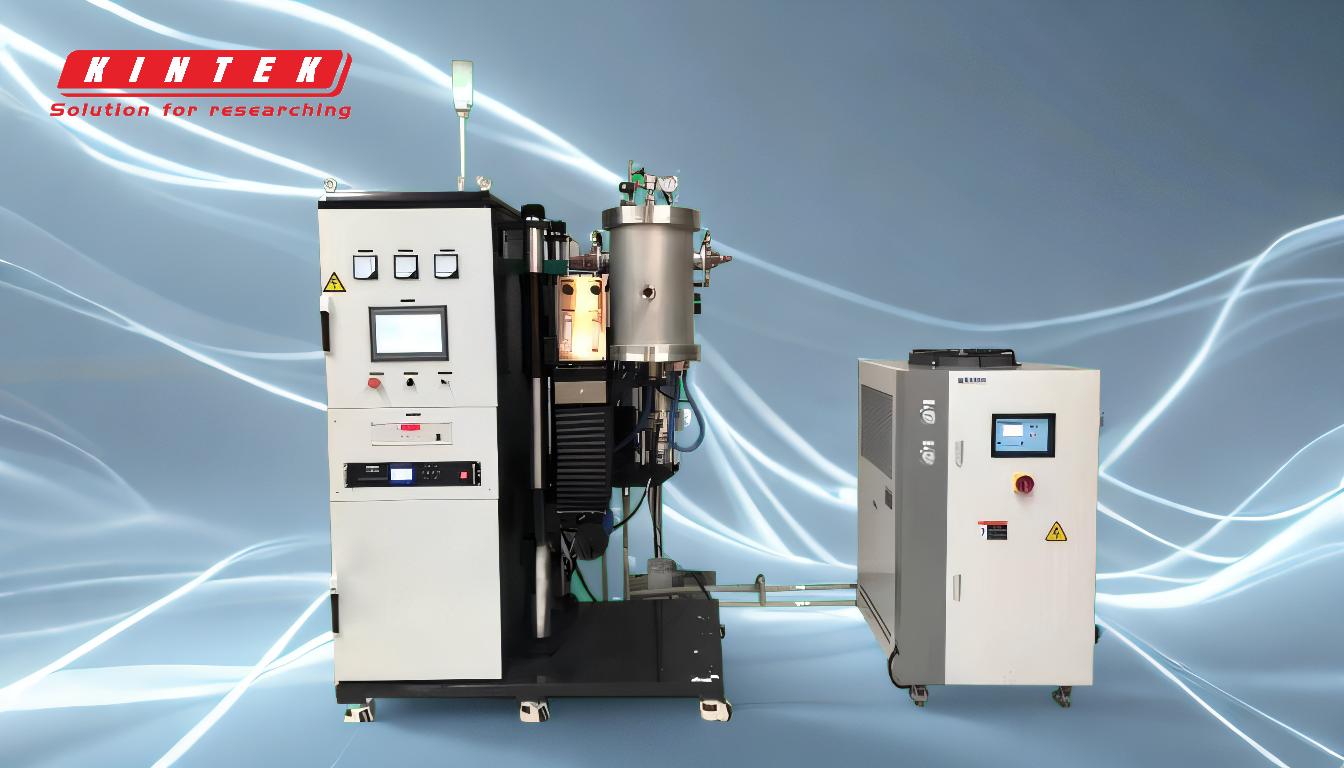
-
What is a Muffle Furnace?
- A muffle furnace is a type of furnace used primarily for high-temperature applications, including the firing of ceramics. It is designed to isolate the material being heated from direct contact with the flames and combustion gases, ensuring a clean and controlled environment.
- The furnace typically consists of a heating chamber (muffle) made from materials that can withstand extreme temperatures, such as ceramic or refractory materials.
-
Key Components of a Muffle Furnace:
- Stainless Steel Glory Hole: This component allows for easy loading and unloading of ceramic pieces while maintaining the integrity of the heating chamber.
- Double Insulation Ceramic Liner: The liner provides excellent thermal insulation, ensuring that the heat is retained within the chamber and reducing energy consumption.
- Vacuum-Formed Polycrystalline Mullite Fiber Furnace Hearth: This material is known for its high thermal stability and resistance to thermal shock, making it ideal for the high temperatures required in ceramic firing.
-
Advantages of Using a Muffle Furnace for Ceramics:
- Controlled Environment: The muffle design prevents contamination from combustion gases, ensuring that the ceramics are fired in a clean environment.
- Uniform Heating: The insulation and design of the furnace promote even heat distribution, which is crucial for achieving consistent results in ceramic firing.
- Durability: The use of high-quality materials like stainless steel and polycrystalline mullite fiber ensures that the furnace can withstand repeated use at high temperatures.
-
Applications in Ceramics:
- Bisque Firing: The initial firing of ceramic pieces to harden them before glazing.
- Glaze Firing: The final firing process where glazes are melted onto the ceramic surface to create a durable and decorative finish.
- High-Temperature Testing: Muffle furnaces are also used for testing the thermal properties of ceramic materials.
-
Considerations for Purchasing a Muffle Furnace:
- Temperature Range: Ensure the furnace can reach the temperatures required for your specific ceramic processes.
- Chamber Size: Consider the size of the chamber to accommodate the size and quantity of ceramic pieces you plan to fire.
- Energy Efficiency: Look for features like double insulation to reduce energy consumption.
- Durability and Maintenance: Choose a furnace made with high-quality materials that require minimal maintenance and have a long lifespan.
In summary, the muffle furnace is an essential piece of equipment for firing ceramics, offering a controlled, clean, and efficient environment for achieving high-quality results. Its construction with components like a stainless steel glory hole, double insulation ceramic liner, and polycrystalline mullite fiber hearth ensures durability and performance, making it a valuable investment for ceramic artists and manufacturers.
Summary Table:
Feature | Description |
---|---|
Controlled Environment | Prevents contamination from combustion gases for clean firing. |
Uniform Heating | Ensures even heat distribution for consistent ceramic results. |
Durability | Built with stainless steel and polycrystalline mullite fiber for long-term use. |
Key Components | Includes a glory hole, ceramic liner, and mullite fiber hearth for efficiency. |
Applications | Bisque firing, glaze firing, and high-temperature testing. |
Ready to elevate your ceramic firing process? Contact us today to find the perfect muffle furnace for your needs!