Heat treatment in a muffle furnace involves controlled heating and cooling processes to alter the physical and chemical properties of materials, particularly metals and ceramics. This process is widely used in industries such as pharmaceuticals, analytical chemistry, and metallurgy for tasks like ashing, annealing, and tempering. The muffle furnace's design ensures uniform heat distribution and protection of materials from direct exposure to flames, making it ideal for precise and controlled heat treatment. Its versatility, durability, and ability to reach high temperatures quickly make it a valuable tool in laboratory and industrial settings.
Key Points Explained:
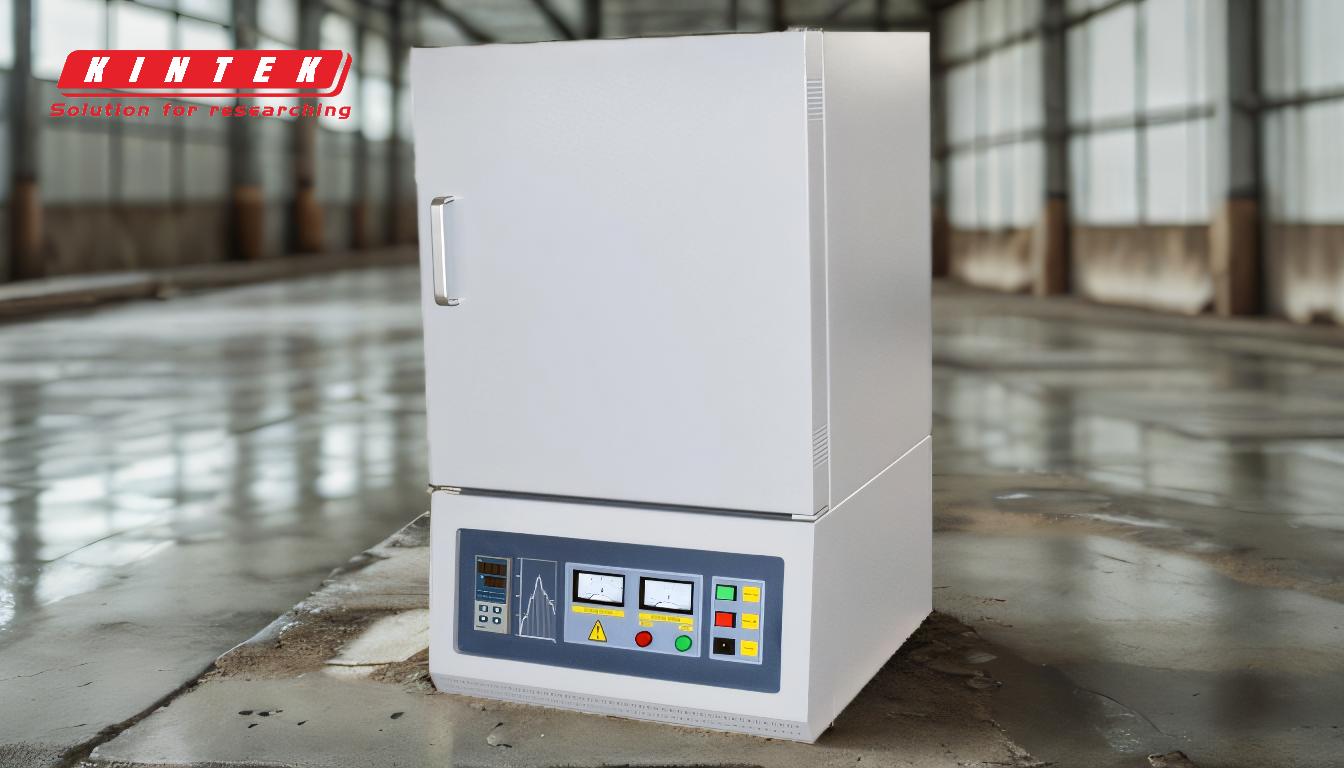
-
Purpose of Heat Treatment in a Muffle Furnace:
- Heat treatment in a muffle furnace is used to modify the properties of materials, such as hardness, strength, and ductility, through controlled heating and cooling cycles.
- It is particularly useful for metals like steel, where altering carbon content can enhance mechanical properties.
-
Applications of Muffle Furnaces in Heat Treatment:
- Ashing and Elemental Analysis: Used in laboratories for determining moisture, ash, volatile matter, and elemental composition.
- Annealing and Tempering: Processes like annealing (softening materials) and tempering (reducing brittleness) are commonly performed in muffle furnaces.
- Sample Pretreatment: Widely used in pharmaceutical and environmental industries for preparing samples for analysis.
-
Design and Functionality:
- The muffle furnace features a heat-resistant inner chamber (muffle) that protects materials from direct exposure to heat, ensuring gentle and uniform heating.
- Modern electric muffle furnaces use induction or convection heating with high-temperature coils and insulating materials to maintain efficiency and prevent heat loss.
-
Advantages of Using a Muffle Furnace:
- High-Temperature Capability: Can reach extremely high temperatures, making it suitable for a wide range of materials and processes.
- Durability and Efficiency: Known for its robust construction and ability to heat up quickly, saving time and energy.
- Versatility: Applicable in various industries, including food, pharmaceuticals, and metallurgy.
-
Comparison with Other Heat Treatment Methods:
- Unlike vacuum furnaces, which can perform advanced processes like carburizing and nitriding, muffle furnaces are better suited for smaller-scale operations and testing due to their compact size.
- They are ideal for processes requiring precise temperature control and uniform heating, such as annealing and ashing.
-
Material Considerations:
- The choice of material to be heated (e.g., borosilicate, alumina, silicon carbide) influences the type of furnace and fuel used (electric or gas-powered).
- Proper selection ensures optimal performance and prevents damage to the furnace or material.
-
Industrial and Laboratory Use:
- In industrial settings, muffle furnaces are used for processing workpieces and heat-treating metals.
- In laboratories, they are essential for sample preparation, analytical testing, and research applications.
By understanding these key points, a purchaser can make informed decisions about selecting a muffle furnace for specific heat treatment needs, ensuring efficiency, precision, and durability in their operations.
Summary Table:
Aspect | Details |
---|---|
Purpose | Modifies material properties (hardness, strength, ductility) through controlled heating/cooling. |
Applications | Ashing, annealing, tempering, sample pretreatment. |
Design | Heat-resistant inner chamber for uniform heating and material protection. |
Advantages | High-temperature capability, durability, efficiency, and versatility. |
Comparison | Better for small-scale operations and precise temperature control than vacuum furnaces. |
Material Considerations | Choice of material (e.g., borosilicate, alumina) impacts furnace performance. |
Use Cases | Industrial (metal heat treatment) and laboratory (sample preparation, testing). |
Discover how a muffle furnace can optimize your heat treatment processes—contact us today!