Magnetron sputtering is a highly versatile and efficient coating technology that has evolved significantly since its inception. Its development has been driven by the need for high-quality, uniform, and durable coatings across various industries. The process involves using a magnetron to create a high-density plasma near the target material, enabling the deposition of thin films with excellent adhesion, purity, and uniformity. Over time, advancements such as high power pulsed magnetron sputtering (HiPIMS) have further enhanced its capabilities, making it a cornerstone in applications ranging from integrated circuits to optical coatings and solar cells.
Key Points Explained:
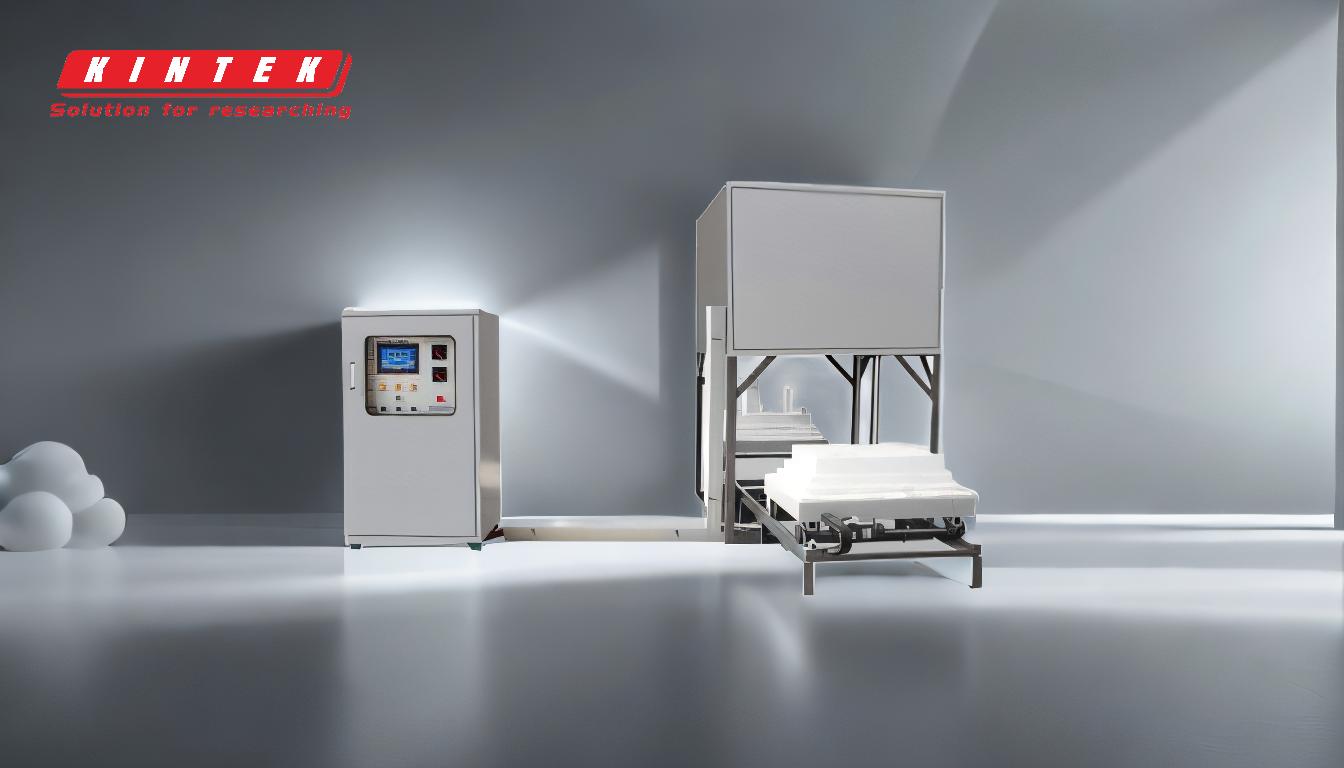
-
Origins and Early Development:
- Magnetron sputtering originated in the mid-20th century as an improvement over traditional sputtering techniques. The introduction of magnetic fields to confine electrons near the target surface significantly increased plasma density and deposition rates.
- Early applications focused on creating thin films for electronic components, where precision and uniformity were critical.
-
Core Principles of Magnetron Sputtering:
- A magnetron sputtering source uses strong magnets to trap electrons, creating a high-density plasma near the target. This plasma generates positive ions that bombard the target, ejecting atoms that deposit onto the substrate.
- The process is material-independent, allowing for the deposition of metals, alloys, and oxides with high purity and adhesion.
-
Advantages of Magnetron Sputtering:
- High Deposition Rates: The confined plasma enables faster deposition compared to conventional sputtering.
- Low Substrate Damage: The substrate remains relatively cool, minimizing thermal stress and damage.
- Versatility: Almost any material can be sputtered, provided it can be formed into a target.
- Uniformity and Repeatability: The process produces films with consistent thickness and properties, even over large areas.
- Controlled Film Properties: Parameters such as power, pressure, and magnetic field strength can be adjusted to control film grain size and composition.
-
Industrial Applications:
- Magnetron sputtering is widely used in industries such as:
- Electronics: For metallization in integrated circuits and semiconductor devices.
- Optics: For anti-reflective and protective coatings on lenses and mirrors.
- Architectural Glass: For energy-efficient and decorative coatings.
- Solar Cells: For thin-film photovoltaic applications.
- Displays: For transparent conductive coatings in screens.
- Magnetron sputtering is widely used in industries such as:
-
Technological Advancements:
- High Power Pulsed Magnetron Sputtering (HiPIMS): This innovation uses short, high-power pulses to achieve higher ionization of sputtered material, resulting in denser and more adherent films.
- Reactive Sputtering: Allows the deposition of compound films (e.g., oxides, nitrides) by introducing reactive gases into the sputtering process.
- Improved Target Utilization: Advances in magnetron design have increased target material usage efficiency, reducing waste and costs.
-
Challenges and Ongoing Development:
- Target Poisoning: In reactive sputtering, the target surface can react with gases, reducing sputtering efficiency. Solutions include pulsed power and optimized gas flow.
- Electrical Instabilities: Arcing and other instabilities can damage films. Modern systems incorporate advanced power supplies and control mechanisms to mitigate these issues.
- Cost Reduction: Efforts are ongoing to lower operating costs through improved energy efficiency and target utilization.
-
Future Prospects:
- Magnetron sputtering continues to evolve, with research focused on enhancing film properties, expanding material compatibility, and enabling new applications in nanotechnology and renewable energy.
- The integration of magnetron sputtering with other deposition techniques, such as atomic layer deposition (ALD), is opening new possibilities for hybrid thin-film systems.
In conclusion, magnetron sputtering has a rich history of innovation and remains a critical technology in modern materials science and industrial applications. Its ability to produce high-quality, uniform coatings with precise control over film properties ensures its continued relevance in advancing technology and industry.
Summary Table:
Key Aspect | Details |
---|---|
Origins | Mid-20th century, improved traditional sputtering with magnetic fields. |
Core Principles | Uses magnets to create high-density plasma for precise thin-film deposition. |
Advantages | High deposition rates, low substrate damage, versatility, and uniformity. |
Applications | Electronics, optics, solar cells, architectural glass, and displays. |
Advancements | HiPIMS, reactive sputtering, improved target utilization. |
Future Prospects | Enhanced film properties, nanotechnology, and renewable energy applications. |
Learn how magnetron sputtering can benefit your industry—contact our experts today!