A hydrogen atmosphere in an annealing furnace is a controlled environment where hydrogen gas, either in pure form or mixed with nitrogen (with a hydrogen content greater than 5%), is used to protect materials during high-temperature heat treatment processes. This atmosphere prevents oxidation and other undesirable chemical reactions, ensuring the material retains its desired properties. Hydrogen annealing furnaces are commonly used in sintering, annealing, and drying processes, particularly for materials sensitive to oxidation. The hydrogen atmosphere can also facilitate surface modifications, such as decarburization or reduction of oxides, depending on the specific application.
Key Points Explained:
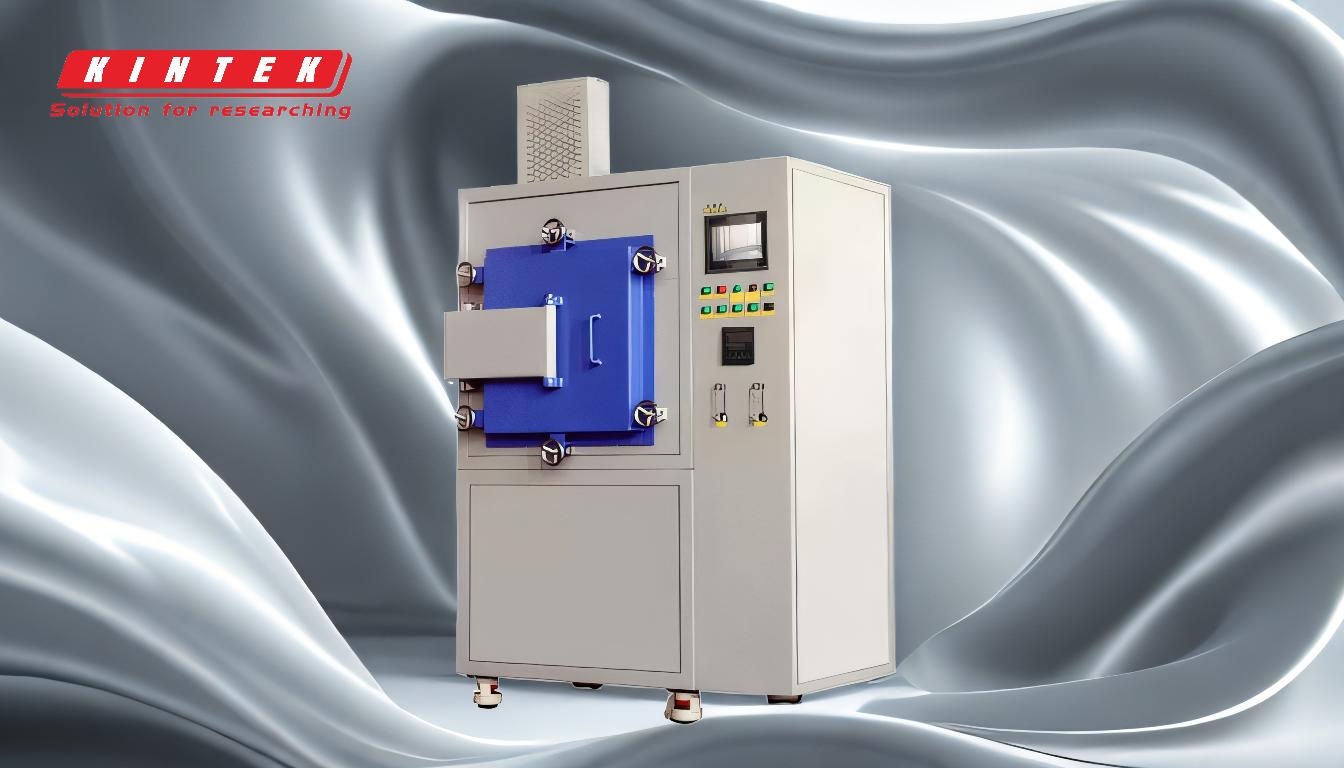
-
Purpose of a Hydrogen Atmosphere in Annealing Furnaces:
- The primary purpose of a hydrogen atmosphere in an annealing furnace is to protect the material from oxidation and other chemical reactions during high-temperature processes. This is particularly important for metals and alloys that are prone to oxidation when exposed to air at elevated temperatures.
- Hydrogen is a reducing gas, which means it can react with oxides on the surface of the material, effectively removing them and preventing further oxidation. This is especially useful in processes like annealing, where the goal is to soften the material and improve its ductility without compromising its surface integrity.
-
Composition of the Atmosphere:
- The hydrogen atmosphere can be either pure hydrogen or a mixture of hydrogen and nitrogen. The hydrogen content in the mixture must be greater than 5% to ensure effective protection and reduction of oxides.
- The choice between pure hydrogen and a hydrogen-nitrogen mixture depends on the specific requirements of the material being processed and the desired outcome of the heat treatment. Pure hydrogen offers the most aggressive reduction potential, while a hydrogen-nitrogen mixture provides a more controlled environment with less risk of excessive reduction.
-
Applications of Hydrogen Atmosphere Furnaces:
- Annealing: Hydrogen atmosphere furnaces are widely used in the annealing of metals and alloys. The hydrogen environment prevents oxidation and decarburization, which are common issues in conventional annealing processes.
- Sintering: In powder metallurgy, hydrogen atmosphere furnaces are used for sintering metal powders. The hydrogen atmosphere helps in reducing surface oxides on the powder particles, leading to better bonding and densification during sintering.
- Drying: Some materials, particularly those that are sensitive to moisture, are dried in a hydrogen atmosphere to prevent oxidation and ensure a clean, oxide-free surface.
-
Advantages of Using Hydrogen Atmosphere:
- Oxidation Prevention: The most significant advantage of using a hydrogen atmosphere is its ability to prevent oxidation, which is crucial for maintaining the material's surface quality and mechanical properties.
- Surface Cleaning: Hydrogen can reduce existing oxides on the material's surface, leading to a cleaner and more uniform surface finish.
- Improved Material Properties: By preventing oxidation and reducing surface oxides, hydrogen annealing can improve the material's ductility, toughness, and overall mechanical properties.
-
Safety Considerations:
- Hydrogen is a highly flammable gas, and its use in annealing furnaces requires strict safety measures. Proper ventilation, gas detection systems, and explosion-proof equipment are essential to ensure safe operation.
- The furnace design must also account for the potential risks associated with hydrogen, such as leaks or buildup of explosive concentrations. Safety protocols, including regular maintenance and inspection, are critical to prevent accidents.
-
Furnace Design and Operation:
- Hydrogen atmosphere furnaces are specially designed to handle the unique requirements of hydrogen gas. This includes features like gas-tight seals, efficient gas circulation systems, and precise temperature control.
- The furnace must be capable of maintaining a consistent hydrogen atmosphere throughout the heating and cooling cycles to ensure uniform treatment of the material.
In summary, a hydrogen atmosphere in an annealing furnace is a critical component in various heat treatment processes, offering protection against oxidation and enabling surface modifications. The use of hydrogen, either in pure form or as a mixture with nitrogen, provides a controlled environment that enhances the material's properties while ensuring safety and efficiency in the furnace operation.
Summary Table:
Aspect | Details |
---|---|
Purpose | Protects materials from oxidation during high-temperature processes. |
Composition | Pure hydrogen or hydrogen-nitrogen mix (≥5% hydrogen). |
Applications | Annealing, sintering, drying of oxidation-sensitive materials. |
Advantages | Prevents oxidation, cleans surfaces, improves ductility and toughness. |
Safety Considerations | Requires ventilation, gas detection, and explosion-proof equipment. |
Furnace Design | Gas-tight seals, efficient gas circulation, precise temperature control. |
Discover how a hydrogen atmosphere furnace can optimize your heat treatment processes—contact us today for expert advice!