Isostatic pressing is a manufacturing process used to produce ceramic products by applying uniform hydrostatic pressure to powdered materials sealed in a flexible mold. This method, which includes both cold isostatic pressing (CIP) and hot isostatic pressing (HIP), ensures consistent density and minimal defects in the final product. CIP, in particular, is widely used for large or complex-shaped components that do not require high precision after sintering. The process involves loading powder into a flexible mold, sealing it, and applying pressure via a liquid medium in a pressure vessel. This technique is versatile and finds applications in industries such as aerospace, automotive, medical devices, and energy storage technologies like lithium-ion batteries and fuel cells.
Key Points Explained:
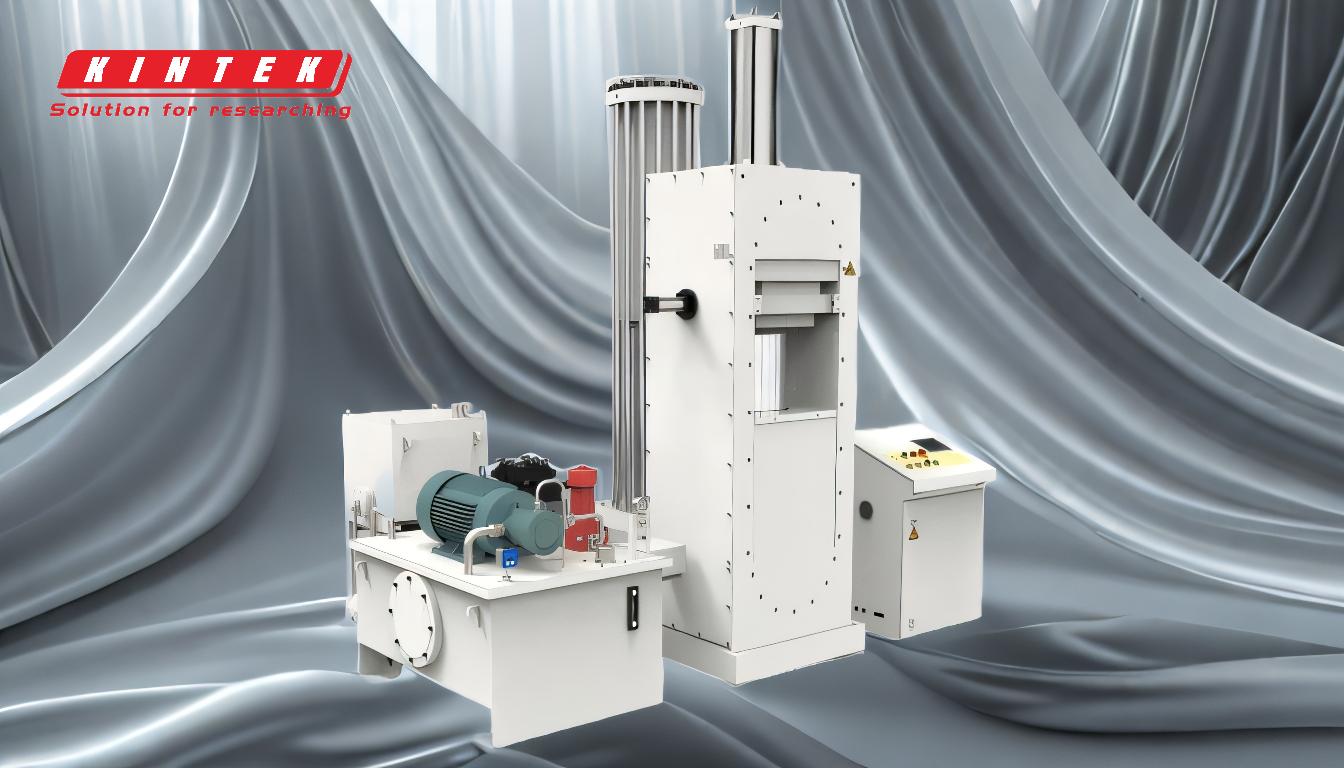
-
What is Isostatic Pressing?
- Isostatic pressing is a method of compacting powdered materials into a desired shape by applying uniform pressure from all directions. This is achieved by sealing the powder in a flexible mold and subjecting it to hydrostatic pressure using a liquid medium.
- The process can be performed at room temperature (cold isostatic pressing) or at elevated temperatures (hot isostatic pressing), depending on the material and application requirements.
-
Cold Isostatic Pressing (CIP) Process
- CIP involves placing powder in a flexible mold, typically made of polyurethane or rubber, and sealing it. The mold is then submerged in a pressure vessel filled with a liquid, such as water or oil.
- Hydraulic pressure is applied uniformly to the mold, compressing the powder into a dense, uniform shape. After pressing, the pressure is released, and the compacted powder body is removed from the mold.
- CIP is particularly useful for producing large or complex-shaped components that are difficult to press using uniaxial methods. It is also effective for materials that do not require high precision after sintering.
-
Wet-Bag vs. Dry-Bag Techniques
- Wet-Bag Technique: The flexible mold containing the powder is submerged in the pressure vessel, and the entire assembly is pressurized. This method is suitable for low-volume production or prototyping.
- Dry-Bag Technique: The flexible mold is fixed inside the pressure vessel, and powder is loaded without removing the mold. This method is more efficient for high-volume production and is commonly used in industrial applications.
-
Applications of Isostatic Pressing
- Advanced Ceramics: Used in aerospace and automotive industries for components requiring high strength and thermal stability.
- Energy Storage: Applied in the production of lithium-ion batteries, fuel cells, and solid-state batteries, such as garnet-based solid electrolyte membranes.
- Medical Devices: Used to manufacture biocompatible ceramic components for implants and surgical tools.
- Industrial Tools: CIP is employed to produce wear-resistant and metal-forming tools from materials like silicon nitride, silicon carbide, and boron carbide.
-
Advantages of Cold Isostatic Pressing
- Uniform Density: Ensures consistent material properties throughout the component.
- Complex Shapes: Capable of producing intricate geometries that are difficult to achieve with other methods.
- High Green Density: Results in a dense, strong green body that reduces the risk of defects during sintering.
- Versatility: Suitable for a wide range of materials, including ceramics, graphite, and refractory materials.
-
Cold Isostatic Pressing Machine
- A cold isostatic pressing machine operates at room temperature and uses liquid as the pressure medium. It can apply high pressures (100-630 MPa) to achieve optimal compaction.
- These machines are essential for producing advanced materials, such as solid-state battery components, and are widely used in research and development for process parameter studies and sample preparation.
-
Materials Processed by CIP
- Common materials include silicon nitride, silicon carbide, boron nitride, boron carbide, titanium boride, and spinel. These materials are chosen for their exceptional mechanical, thermal, and electrical properties, making them ideal for demanding applications.
-
Future Trends and Innovations
- CIP is increasingly being used in the development of next-generation energy storage technologies, such as all-solid-state batteries and ultra-thin flexible composite solid electrolyte membranes.
- Ongoing research focuses on optimizing process parameters to improve the performance and efficiency of CIP-produced components.
In summary, isostatic pressing, particularly cold isostatic pressing, is a versatile and efficient method for producing high-quality ceramic products. Its ability to create uniform, dense, and complex-shaped components makes it indispensable in industries ranging from aerospace to energy storage. The use of advanced cold isostatic pressing machines further enhances the precision and scalability of this process.
Summary Table:
Aspect | Details |
---|---|
Process | Uniform hydrostatic pressure applied to powdered materials in a flexible mold. |
Types | Cold Isostatic Pressing (CIP) and Hot Isostatic Pressing (HIP). |
Key Advantages | Uniform density, complex shapes, high green density, and material versatility. |
Applications | Aerospace, automotive, medical devices, energy storage (e.g., lithium-ion batteries). |
Materials Processed | Silicon nitride, silicon carbide, boron carbide, and more. |
Future Trends | Focus on next-gen energy storage technologies and process optimization. |
Learn how isostatic pressing can revolutionize your ceramic production—contact our experts today!