The hot forging process is widely recognized for its ability to produce high-strength, durable metal components with superior mechanical properties. This process involves heating metal to a temperature above its recrystallization point, making it more malleable and easier to shape. The primary advantage of hot forging lies in its ability to refine the grain structure of the metal, enhancing its strength, toughness, and resistance to wear and fatigue. Additionally, hot forging allows for the creation of complex shapes with minimal material waste, making it a cost-effective and efficient manufacturing method for industries such as automotive, aerospace, and heavy machinery.
Key Points Explained:
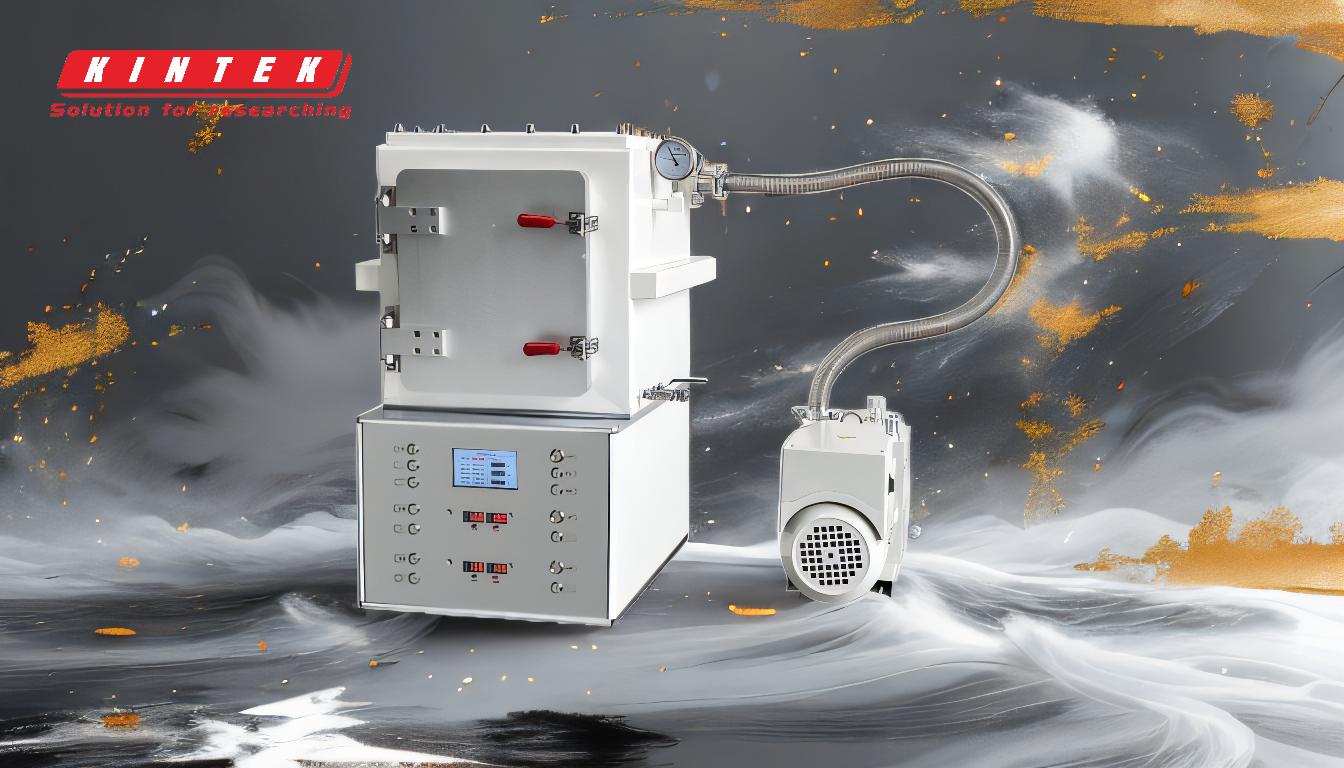
-
Enhanced Mechanical Properties:
- Hot forging significantly improves the mechanical properties of metals. By heating the metal above its recrystallization temperature, the process allows for the rearrangement of the metal's grain structure. This results in a finer, more uniform grain size, which enhances the material's strength, toughness, and resistance to impact and fatigue. These improved properties are crucial for components subjected to high stress and demanding operational conditions.
-
Complex Shape Formation:
- The malleability of heated metal in the hot forging process enables the creation of intricate and complex shapes that would be difficult or impossible to achieve with cold forging or machining. This capability is particularly valuable in industries where components must meet precise specifications and tight tolerances, such as in aerospace and automotive manufacturing.
-
Material Efficiency and Cost-Effectiveness:
- Hot forging minimizes material waste by allowing manufacturers to shape metal with high precision. The process often produces near-net-shape components, reducing the need for extensive machining and finishing. This efficiency translates to lower material costs and reduced production time, making hot forging an economically attractive option for large-scale manufacturing.
-
Improved Flow and Uniformity:
- The high temperatures used in hot forging ensure that the metal flows more uniformly during the shaping process. This uniformity reduces the likelihood of defects such as cracks, voids, or inclusions, which can compromise the integrity of the final product. As a result, hot-forged components are known for their reliability and consistency.
-
Versatility Across Materials:
- Hot forging is applicable to a wide range of metals and alloys, including steel, aluminum, titanium, and copper. This versatility makes it a preferred method for producing components across various industries, from automotive parts to heavy machinery and tools.
-
Reduction of Residual Stresses:
- The high temperatures used in hot forging help to relieve internal stresses within the metal, resulting in a more stable and durable final product. This reduction in residual stresses is particularly important for components that will be subjected to cyclic loading or extreme conditions.
In summary, the hot forging process offers a combination of superior mechanical properties, the ability to create complex shapes, material efficiency, and versatility, making it a highly advantageous manufacturing method for producing high-performance metal components.
Summary Table:
Key Advantage | Description |
---|---|
Enhanced Mechanical Properties | Refines grain structure for superior strength, toughness, and fatigue resistance. |
Complex Shape Formation | Enables intricate designs with high precision and tight tolerances. |
Material Efficiency | Minimizes waste and reduces machining needs, lowering costs. |
Improved Flow and Uniformity | Ensures defect-free, reliable, and consistent components. |
Versatility Across Materials | Suitable for steel, aluminum, titanium, and copper alloys. |
Reduction of Residual Stresses | Produces stable, durable components for extreme conditions. |
Unlock the potential of hot forging for your manufacturing needs—contact our experts today!