The main purpose of the solid-state sintering process is to transform powdered materials into dense, strong, and functional components by bonding particles together under high temperatures below their melting point. This process enhances the material's mechanical properties, such as strength and structural integrity, while reducing porosity and achieving desired microstructures. Sintering is widely used in industries like metallurgy, ceramics, and glass manufacturing due to its cost-effectiveness, versatility, and ability to produce complex shapes without requiring melting. It also allows for precise control over material properties and dimensions, making it a critical step in creating end-use parts like gears, bearings, and electrical components.
Key Points Explained:
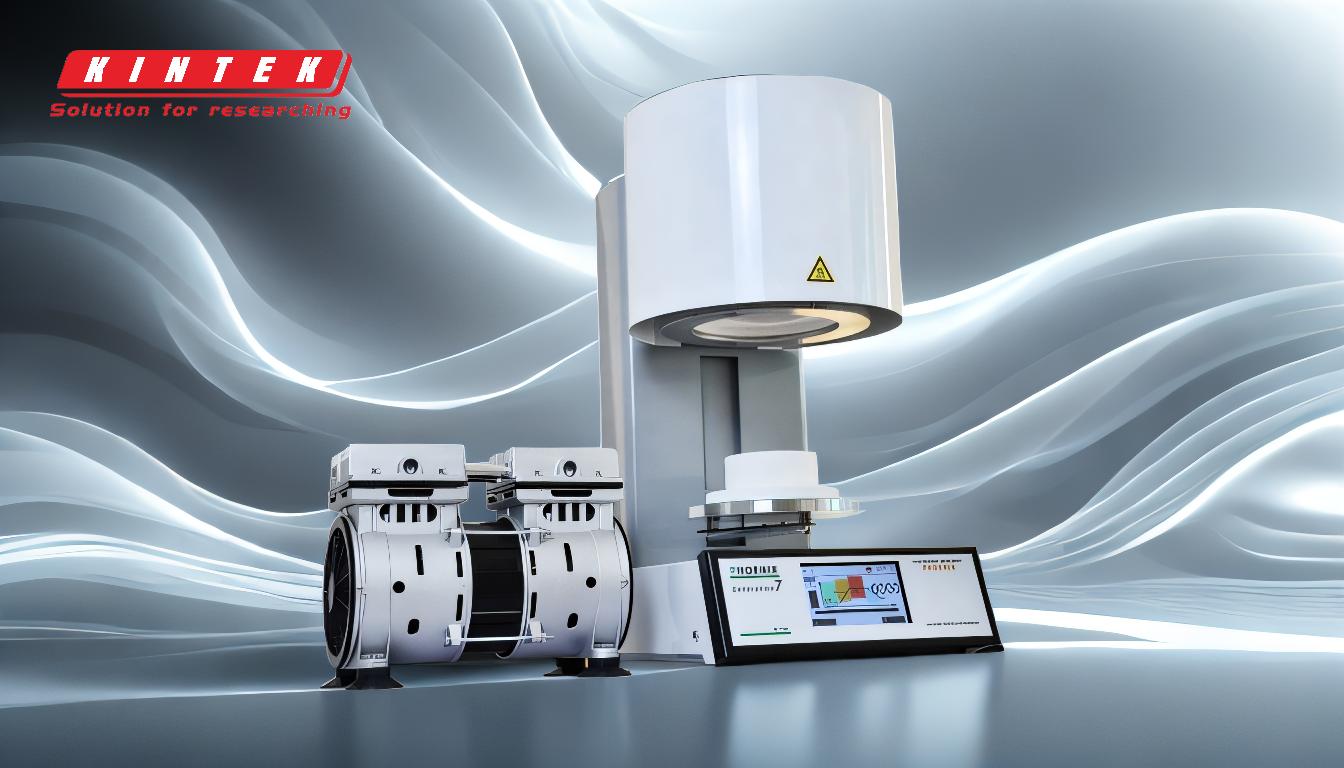
-
Transformation of Powdered Material into Dense Bodies:
- Sintering converts loose powdered materials into solid, dense bodies by bonding particles together. This is achieved through high temperatures, which facilitate atomic diffusion and particle bonding without melting the material.
- The process eliminates pores and reduces volume shrinkage, resulting in a compact and strong final product.
-
Enhancement of Mechanical Properties:
- Sintering improves the intrinsic strength and structural integrity of materials. By bonding particles and reducing porosity, the process creates a hard polycrystalline structure with enhanced mechanical properties, such as durability and resistance to wear.
- The controlled cooling rate during sintering can further fine-tune the material's properties, such as hardness and toughness.
-
Versatility in Manufacturing:
- Sintering is highly versatile and can be used to produce a wide range of components, including gears, bearings, electrical contacts, and rotors. It is applicable across industries like metallurgy, ceramics, and glass manufacturing.
- Unlike traditional manufacturing methods (e.g., casting or forging), sintering does not require a solid-liquid phase change, making it more flexible and cost-effective.
-
Control Over Microstructure and Dimensions:
- The sintering process allows for precise control over the microstructure of the final product, such as grain size and distribution. This control is critical for achieving desired material properties.
- Minor shrinkage during sintering is accounted for during the compaction phase, ensuring that the final dimensions of the part meet specifications.
-
Cost-Effectiveness and Efficiency:
- Sintering is a cost-effective process because it uses powdered materials, which are often less expensive than bulk materials. It also reduces material waste and energy consumption compared to melting-based processes.
- The ability to produce complex shapes and near-net-shape components further enhances its efficiency.
-
Applications in Various Industries:
- In metallurgy, sintering is used to produce steel from iron ore and coke, creating lumps suitable for blast furnace processing.
- In ceramics and glass manufacturing, sintering is essential for creating dense, durable products with specific properties.
- The process is also integral to powder metallurgy, where it shapes metal powders into end-use parts with high precision.
By understanding these key points, equipment and consumable purchasers can appreciate the critical role of sintering in manufacturing and make informed decisions about materials and processes for their specific applications.
Summary Table:
Key Aspect | Description |
---|---|
Transformation of Powdered Material | Converts loose powders into dense, solid bodies under high temperatures. |
Enhanced Mechanical Properties | Improves strength, durability, and wear resistance by reducing porosity. |
Versatility in Manufacturing | Produces complex shapes like gears, bearings, and electrical components. |
Microstructure & Dimension Control | Enables precise control over grain size, distribution, and final dimensions. |
Cost-Effectiveness | Uses less expensive powdered materials, reduces waste, and saves energy. |
Industry Applications | Widely used in metallurgy, ceramics, glass manufacturing, and powder metallurgy. |
Learn how solid-state sintering can optimize your manufacturing process—contact us today for expert guidance!