Sputtering is a physical vapor deposition (PVD) technique widely used in various industries for thin film deposition. The major purpose of sputtering is to create thin, uniform coatings on substrates by bombarding a target material with high-energy ions, typically argon, to dislodge atoms from the target. These atoms then travel through a vacuum chamber and deposit onto a substrate, forming a thin film. This process is highly controllable and allows for the deposition of a wide range of materials, including metals, semiconductors, and insulators, with precise thickness and uniformity. Sputtering is essential in applications such as semiconductor manufacturing, optical coatings, and the production of solar panels.
Key Points Explained:
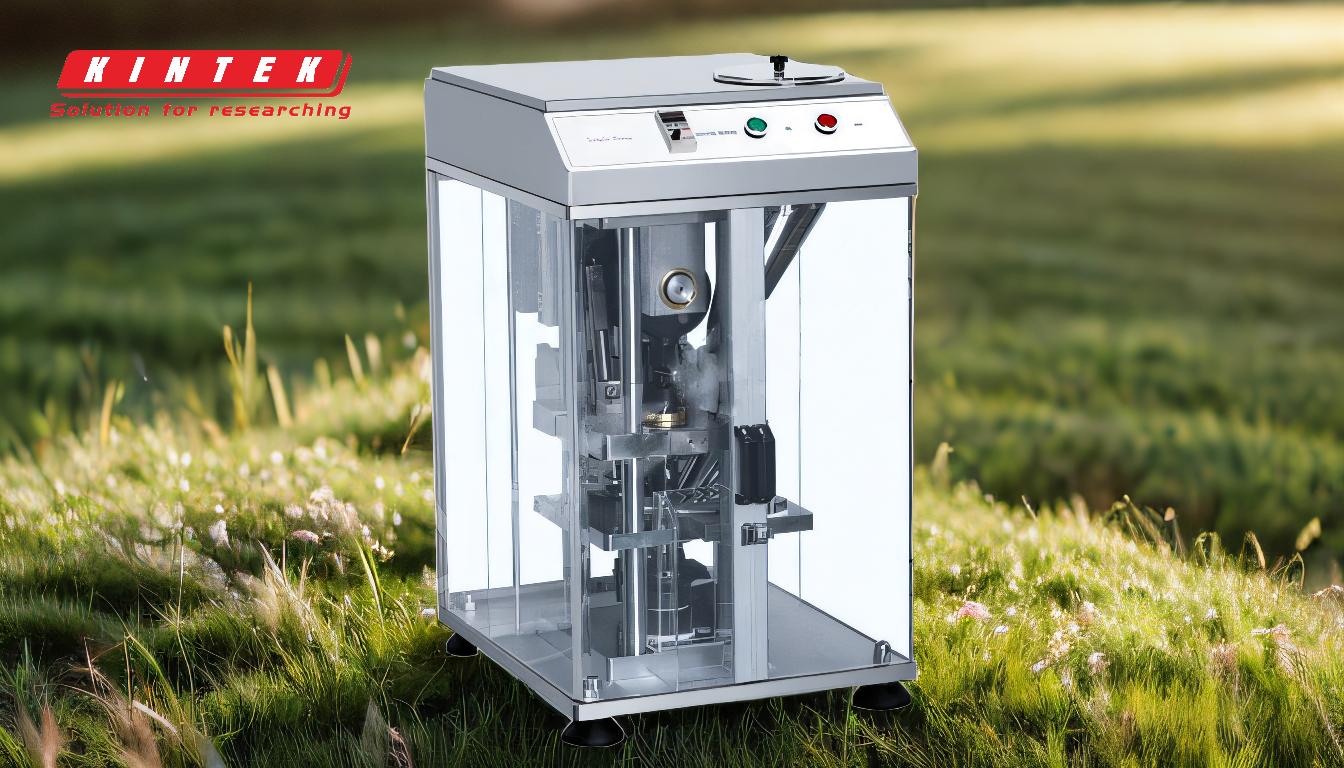
-
Thin Film Deposition:
- Sputtering is primarily used for depositing thin films onto substrates. The process involves the ejection of atoms from a target material due to bombardment by high-energy ions, typically argon. These ejected atoms travel through a vacuum chamber and deposit onto a substrate, forming a thin, uniform layer. This method is particularly valued for its ability to produce coatings with consistent thickness and high quality.
-
Uniformity and Consistency:
- One of the key advantages of sputtering is the uniformity of the deposited films. The low-pressure environment and the characteristics of the sputtered material ensure that the atoms deposit evenly across the substrate. This uniformity is crucial for applications where precise thickness and consistent coating quality are required, such as in semiconductor devices and optical coatings.
-
Versatility in Materials:
- Sputtering can be used to deposit a wide variety of materials, including metals, semiconductors, and insulators. This versatility makes it a valuable technique in multiple industries. For example, in the semiconductor industry, sputtering is used to deposit conductive layers, while in the optical industry, it is used to create anti-reflective coatings.
-
High-Energy Ion Bombardment:
- The process relies on the bombardment of the target material with high-energy ions, usually argon. These ions are accelerated towards the target, causing the ejection of atoms from the target surface. The energy transfer from the ions to the target material is what drives the sputtering process, making it a highly efficient method for thin film deposition.
-
Applications in Various Industries:
- Sputtering is used in numerous applications across different industries. In semiconductor manufacturing, it is used to create conductive pathways and interconnects. In the production of solar panels, sputtering is used to deposit thin films that enhance the efficiency of the panels. Additionally, sputtering is used in the creation of optical coatings, such as anti-reflective and mirror coatings, which are essential in various optical devices.
In summary, sputtering is a versatile and precise method for depositing thin films with uniform thickness and high quality. Its applications span across multiple industries, making it a critical technology in modern manufacturing and material science.
Summary Table:
Key Aspect | Description |
---|---|
Thin Film Deposition | Deposits thin, uniform layers on substrates using high-energy ion bombardment. |
Uniformity & Consistency | Ensures even coating thickness, critical for semiconductors and optical devices. |
Versatility in Materials | Works with metals, semiconductors, and insulators for diverse applications. |
High-Energy Ion Process | Uses argon ions to dislodge target atoms, enabling efficient thin film creation. |
Industry Applications | Essential for semiconductors, solar panels, and optical coatings. |
Ready to enhance your thin film processes? Contact our experts today to learn more about sputtering solutions!