Sintering is a manufacturing process that transforms powdered materials into a solid, cohesive structure through the application of heat and pressure. The process involves several key steps, including powder preparation, compaction, heating, and cooling. Each step is critical to achieving the desired material properties, such as density, strength, and porosity. Sintering is widely used in industries like metallurgy, ceramics, and glass manufacturing, where it helps create complex shapes and high-performance materials. The process can be tailored to specific applications by adjusting parameters such as temperature, pressure, and the use of additives like binders or liquid phases.
Key Points Explained:
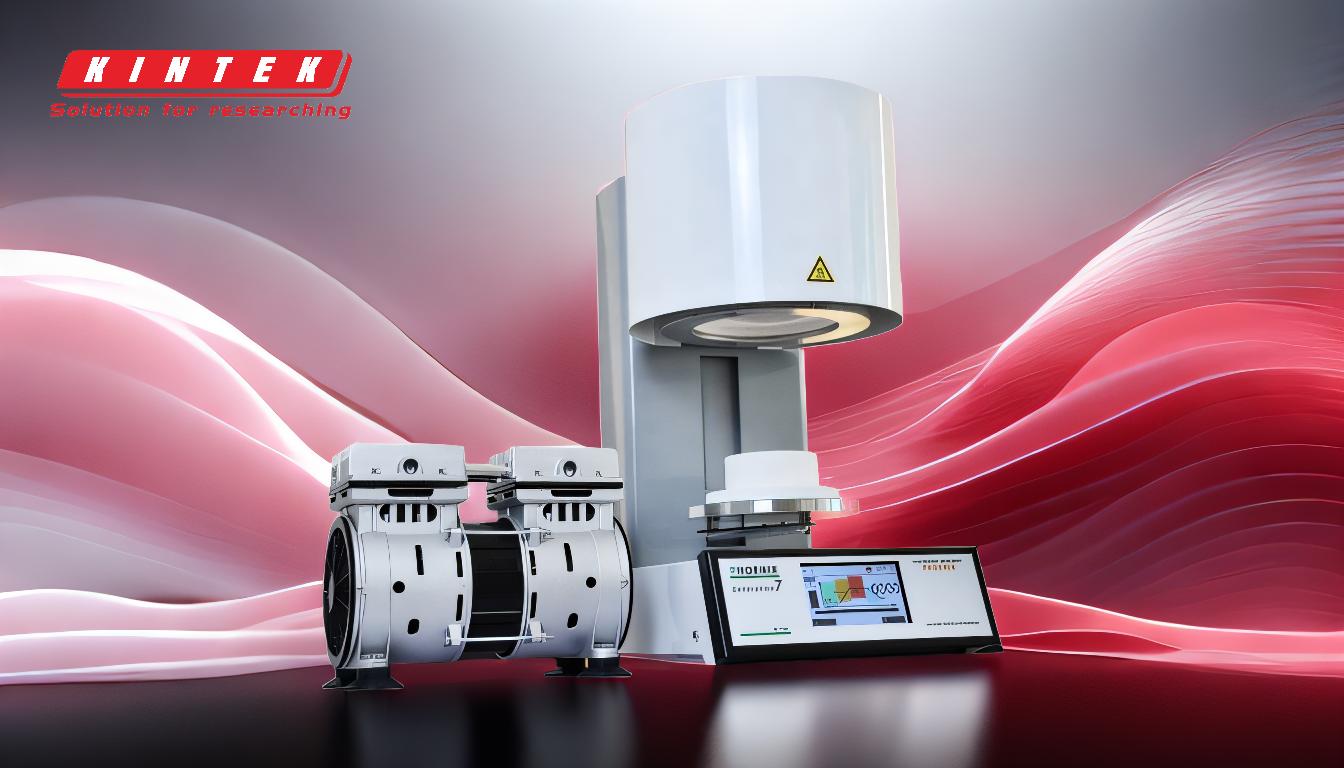
-
Powder Preparation
- The first step in sintering involves preparing the raw material in powdered form. This can include metals, ceramics, or other materials.
- The powder is often mixed with additives like binders, coupling agents, or lubricants to improve compaction and bonding during the process.
- In some cases, the powder is pre-treated to remove impurities or achieve a specific particle size distribution.
-
Compaction
- The powdered material is then compacted into a desired shape using methods such as cold pressing, 3D-printed lasers, or pressing tools.
- High pressure is applied to ensure the powder particles are tightly packed, which helps achieve the required density and structural integrity.
- The compacted shape, known as a "green body," is fragile and requires further processing to become a solid product.
-
Heating and Consolidation
- The green body is heated in a controlled environment, typically in a sintering furnace, to a temperature just below the material's melting point.
- This heating activates the bonding mechanisms between particles, such as diffusion and grain boundary formation, leading to densification.
- In some cases, liquid phase sintering (LPS) is used, where a liquid additive helps accelerate particle merging and densification.
-
Particle Merging and Densification
- During heating, the particles begin to merge, reducing porosity and increasing the material's density.
- This stage is critical for achieving the desired mechanical properties, such as strength and durability.
- The process can be influenced by factors like temperature, heating rate, and the presence of additives.
-
Cooling and Solidification
- After the sintering process, the material is cooled gradually to allow it to solidify into a unified mass.
- Controlled cooling helps prevent defects like cracking or warping and ensures the material retains its desired properties.
- The final product is a dense, solid structure with minimal porosity, ready for further processing or use.
-
Applications and Variations
- Sintering is used in various industries, including metallurgy (e.g., producing sintered iron for blast furnaces), ceramics, and glass manufacturing.
- The process can be adapted for specific applications by adjusting parameters like temperature, pressure, and the use of additives.
- For example, in metal sintering, powdered iron mixed with coke is ignited to form lumps suitable for steel production.
By understanding these key steps, manufacturers can optimize the sintering process to produce high-quality materials tailored to specific applications. The ability to control parameters like temperature, pressure, and additives makes sintering a versatile and essential manufacturing technique.
Summary Table:
Step | Description |
---|---|
Powder Preparation | Prepare raw materials in powdered form, often mixed with additives. |
Compaction | Compact powder into a desired shape using high pressure. |
Heating & Consolidation | Heat the green body below melting point to activate bonding mechanisms. |
Particle Merging | Particles merge, reducing porosity and increasing density. |
Cooling | Gradually cool the material to solidify and prevent defects. |
Applications | Used in metallurgy, ceramics, and glass manufacturing for high-performance materials. |
Discover how sintering can optimize your manufacturing process—contact us today for expert advice!