High-temperature furnace elements are constructed using specialized materials that can withstand extreme heat and harsh operating conditions. The materials used vary depending on the furnace type, temperature range, and application. Common materials include platinum, tungsten disilicide, molybdenum disilicide, molybdenum, silicon carbide, iron-chrome aluminum, nickel chrome alloys, tungsten, tantalum, and graphite. These materials are chosen for their high melting points, resistance to oxidation, and ability to maintain structural integrity at elevated temperatures. For vacuum furnaces operating above 1200°C, pure metals like tungsten, tantalum, and graphite are often preferred due to their stability in low-oxygen environments.
Key Points Explained:
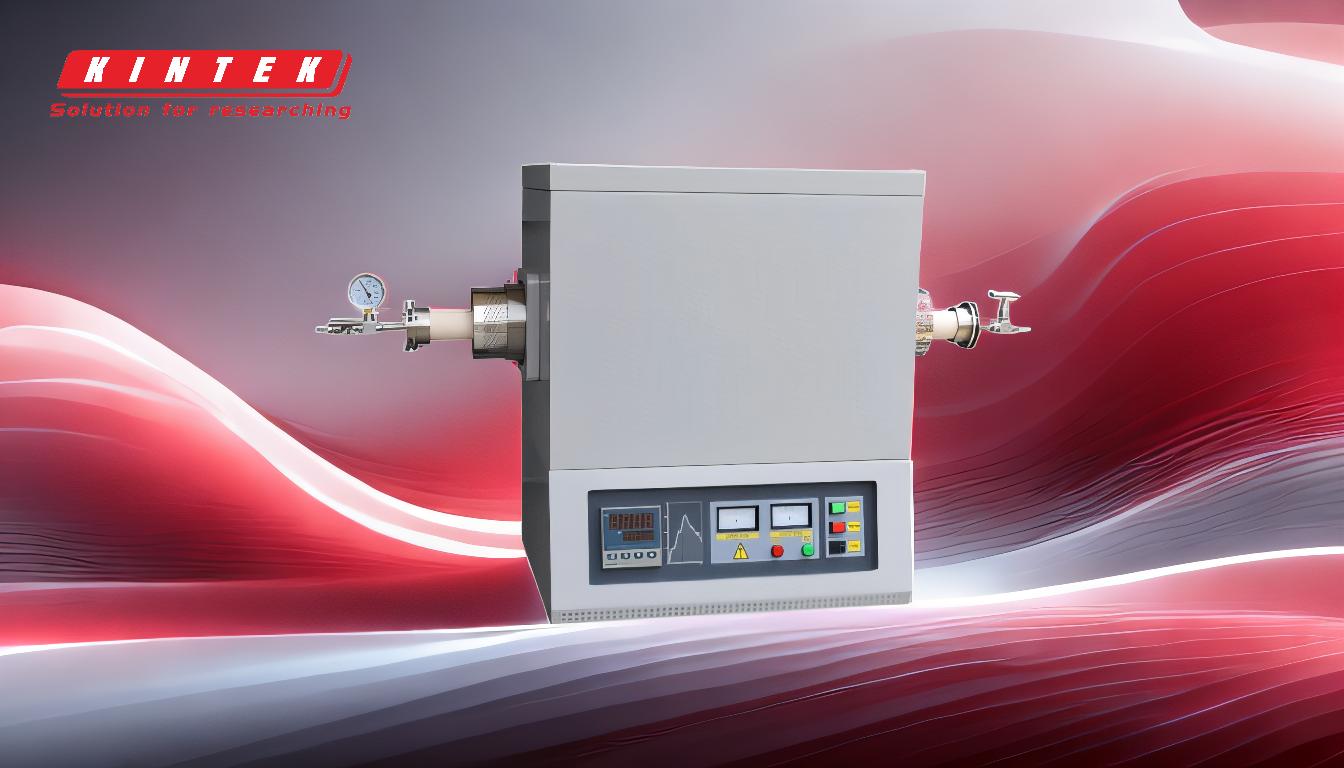
-
Exotic Materials for High-Temperature Applications
- Materials like platinum, tungsten disilicide, molybdenum disilicide, and silicon carbide are commonly used in high-temperature furnaces.
- These materials are chosen for their exceptional thermal stability and resistance to oxidation at extreme temperatures.
- For example, silicon carbide is ideal for furnaces operating in oxidizing atmospheres, while molybdenum disilicide is suitable for both oxidizing and reducing environments.
-
Alloys for Industrial Furnaces
- Iron-chrome aluminum and nickel chrome alloys are widely used in industrial furnaces.
- These alloys are cost-effective and can be shaped into cylindrical, semi-circular, or flat panels for efficient heat distribution.
- They are typically used in furnaces with operating temperatures below 1200°C.
-
Pure Metals for Vacuum Furnaces
- For vacuum furnaces operating above 1200°C, pure metals like tungsten, tantalum, and graphite are preferred.
- These materials maintain their structural integrity in low-oxygen environments and have high melting points.
- Graphite is particularly favored for its lightweight and excellent thermal conductivity.
-
Specialized Forms and Configurations
- Heating elements are available in various forms, such as lightweight curved graphite or molybdenum strips.
- Options like pure or lanthanated molybdenum strips offer enhanced performance in specific applications.
- The choice of form depends on the furnace design and the required thermal efficiency.
-
Material Selection Based on Operating Conditions
- The selection of heating element material depends on factors like temperature range, atmosphere (oxidizing, reducing, or vacuum), and mechanical stress.
- For example, tungsten is ideal for ultra-high-temperature vacuum furnaces, while silicon carbide is better suited for oxidizing environments.
By understanding the properties and applications of these materials, purchasers can make informed decisions when selecting heating elements for high-temperature furnaces.
Summary Table:
Material | Key Properties | Applications |
---|---|---|
Platinum | High melting point, oxidation resistance | High-temperature furnaces, chemical processing |
Tungsten Disilicide | Exceptional thermal stability, oxidation resistance | Oxidizing and reducing environments |
Molybdenum Disilicide | High thermal stability, oxidation resistance | Oxidizing and reducing environments |
Silicon Carbide | Excellent oxidation resistance, thermal conductivity | Oxidizing atmospheres |
Iron-Chrome Aluminum | Cost-effective, heat distribution efficiency | Industrial furnaces (<1200°C) |
Nickel Chrome Alloys | Cost-effective, versatile shapes | Industrial furnaces (<1200°C) |
Tungsten | High melting point, structural integrity in vacuum | Ultra-high-temperature vacuum furnaces |
Tantalum | High melting point, stability in low-oxygen environments | Vacuum furnaces (>1200°C) |
Graphite | Lightweight, excellent thermal conductivity | Vacuum furnaces (>1200°C) |
Need help selecting the right materials for your high-temperature furnace? Contact our experts today for personalized guidance!