The maximum temperature an induction furnace can achieve depends on its design, power source, and the materials being melted. Medium frequency induction furnaces, which are commonly used in industrial applications, can reach temperatures close to 2000°C. This high temperature capability makes them suitable for melting a wide range of metals, including steel, iron, and other high-melting-point alloys. The use of advanced technologies, such as IGBT induction furnaces, further enhances their efficiency and temperature control, making them a preferred choice in modern metallurgical processes.
Key Points Explained:
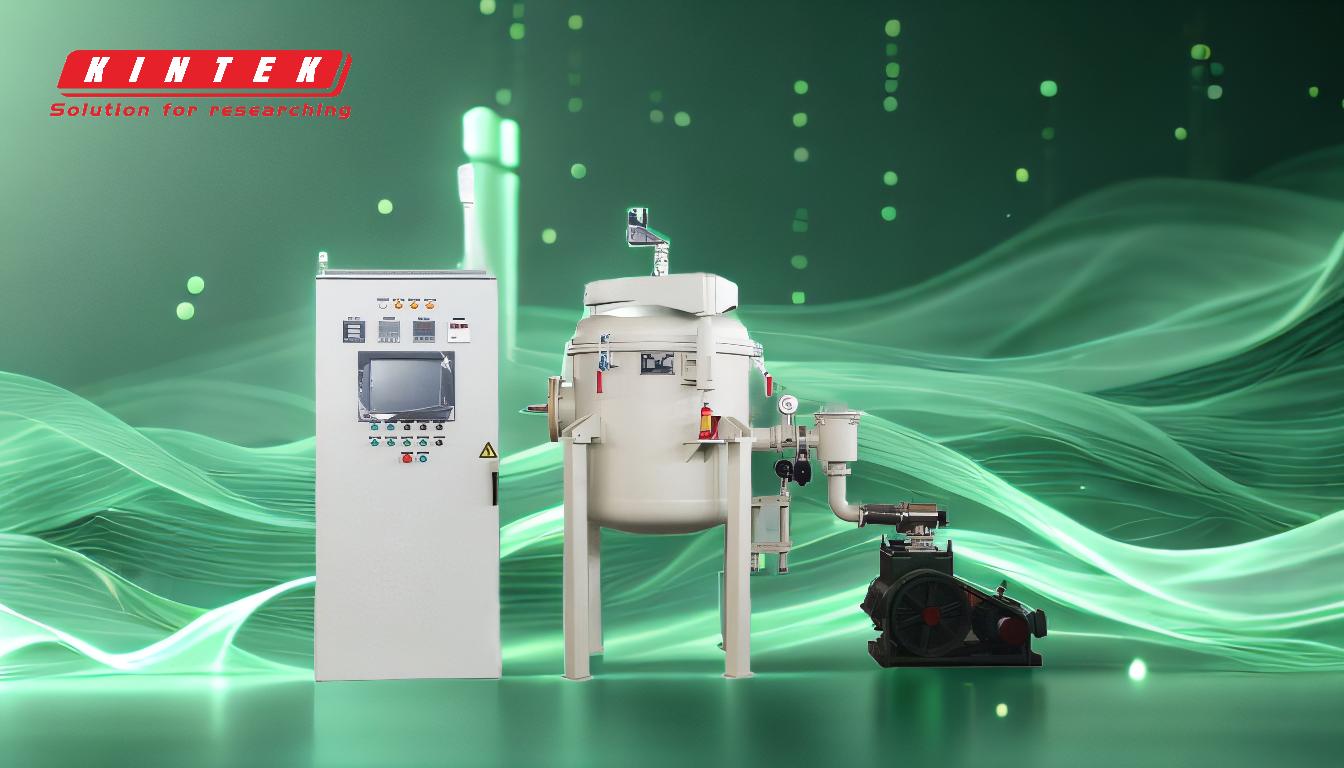
-
Maximum Temperature of Induction Furnaces:
- Induction furnaces, particularly medium frequency models, can achieve temperatures close to 2000°C. This high temperature is essential for melting metals with high melting points, such as steel and iron. The ability to reach such temperatures is a result of the furnace's efficient energy transfer and advanced design.
-
Role of Frequency in Heating:
- The frequency of the induction current plays a crucial role in determining the heating efficiency and maximum temperature. Medium frequency induction furnaces, typically operating in the range of 1-10 kHz, are designed to provide a balance between penetration depth and heating rate, making them ideal for high-temperature applications.
-
Advantages of IGBT Induction Furnaces:
- IGBT induction furnaces utilize Insulated Gate Bipolar Transistor technology, which offers superior control over the heating process. This technology allows for precise temperature regulation, improved energy efficiency, and reduced operational costs. The use of IGBTs also contributes to the furnace's ability to reach and maintain high temperatures consistently.
-
Applications Requiring High Temperatures:
- The ability to reach temperatures close to 2000°C makes induction furnaces suitable for a variety of industrial applications. These include the melting of high-melting-point metals, alloy production, and specialized metallurgical processes that require precise temperature control.
-
Factors Influencing Maximum Temperature:
- Several factors influence the maximum temperature an induction furnace can achieve, including the power supply, coil design, and the type of material being melted. Advanced designs and technologies, such as those found in IGBT induction furnaces, help optimize these factors to achieve higher temperatures and better performance.
-
Safety and Maintenance Considerations:
- Operating at such high temperatures requires careful attention to safety and maintenance. Proper insulation, cooling systems, and regular maintenance are essential to ensure the furnace operates efficiently and safely. The use of advanced technologies like IGBTs also contributes to safer operation by providing better control and reducing the risk of overheating.
By understanding these key points, purchasers and operators of induction furnaces can make informed decisions about the equipment they need, ensuring they achieve the desired results while maintaining safety and efficiency.
Summary Table:
Key Aspect | Details |
---|---|
Maximum Temperature | Up to 2000°C, ideal for melting high-melting-point metals like steel and iron. |
Frequency Range | 1-10 kHz for medium frequency induction furnaces. |
IGBT Technology | Enhances efficiency, temperature control, and energy savings. |
Applications | Melting metals, alloy production, and specialized metallurgical processes. |
Influencing Factors | Power supply, coil design, and material type. |
Safety & Maintenance | Requires proper insulation, cooling systems, and regular maintenance. |
Ready to achieve high-performance melting with induction furnaces? Contact us today to find the perfect solution for your needs!