The maximum temperature for brazing is not a fixed value but depends on the specific braze alloy being used. Generally, the brazing temperature should be set at least 25°C (50°F) above the liquidus temperature of the braze alloy to ensure proper melting and flow. However, it should not exceed the melting point of the base materials being joined. The goal is to achieve a temperature that allows the braze alloy to melt and flow effectively without damaging the components. This balance ensures strong, reliable joints while maintaining the integrity of the materials involved.
Key Points Explained:
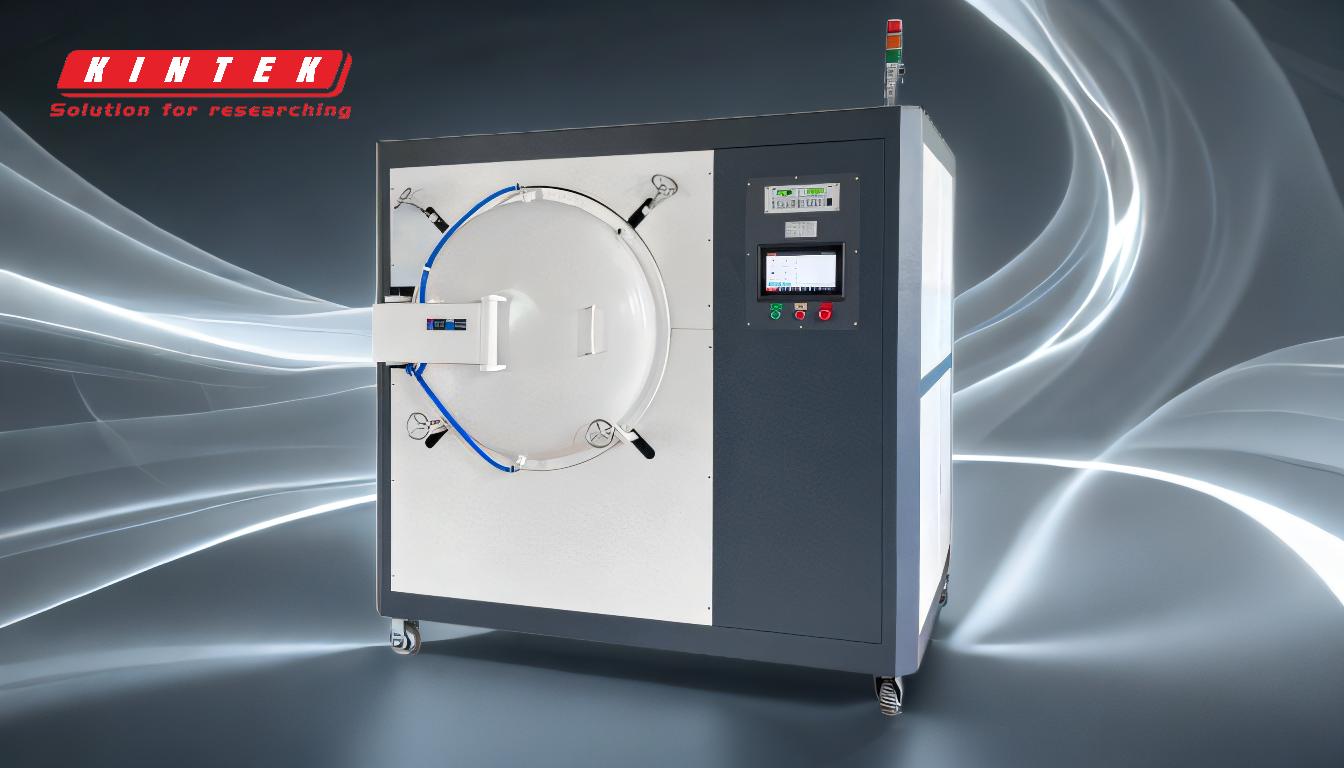
-
Brazing Temperature Range:
- The brazing temperature is determined by the liquidus temperature of the braze alloy, which is the temperature at which the alloy becomes completely liquid.
- It is recommended to set the brazing temperature at least 25°C (50°F) above the liquidus temperature to ensure the alloy flows properly into the joint.
-
Importance of Staying Above Liquidus Temperature:
- Staying above the liquidus temperature ensures that the braze alloy fully melts, allowing it to wet the surfaces of the base materials and form a strong bond.
- If the temperature is too close to the liquidus temperature, the alloy may not flow sufficiently, leading to weak or incomplete joints.
-
Avoiding Excessive Temperatures:
- While the temperature must be high enough to melt the braze alloy, it should not exceed the melting point of the base materials.
- Excessive temperatures can cause distortion, grain growth, or even melting of the base materials, compromising the integrity of the joint.
-
Factors Influencing Maximum Temperature:
- The type of braze alloy used (e.g., silver-based, copper-based, or nickel-based alloys) will determine the liquidus temperature and, consequently, the brazing temperature.
- The base materials being joined also play a critical role, as their thermal properties and melting points set an upper limit for the brazing temperature.
-
Practical Considerations:
- In industrial applications, precise temperature control is essential to achieve consistent results.
- Furnaces, torches, or induction heating methods are commonly used, with temperature monitoring tools ensuring the process stays within the desired range.
By carefully selecting the appropriate braze alloy and controlling the brazing temperature, manufacturers can achieve strong, durable joints while avoiding damage to the base materials.
Summary Table:
Key Factor | Details |
---|---|
Brazing Temperature Range | Set at least 25°C (50°F) above the braze alloy's liquidus temperature. |
Importance of Liquidus Temp | Ensures proper melting and flow of the braze alloy for strong bonds. |
Avoid Excessive Temperatures | Must not exceed the melting point of the base materials to prevent damage. |
Influencing Factors | Braze alloy type and base material properties determine the optimal range. |
Practical Considerations | Use precise temperature control tools like furnaces or induction heating. |
Need help optimizing your brazing process? Contact our experts today for tailored solutions!