Induction heating is a highly efficient and precise method of heating conductive materials, primarily metals, using electromagnetic induction. The maximum temperature achievable with induction heating depends on several factors, including the material being heated, the design of the induction coil, and the power supply. Based on the references provided, induction heating can reach temperatures of up to 2000°C, particularly in specialized applications like induction melting furnaces. This high-temperature capability makes induction heating suitable for processes such as melting, forging, and heat treatment of metals. However, achieving these extreme temperatures requires careful engineering, including the design of the induction coil and the management of high-current densities.
Key Points Explained:
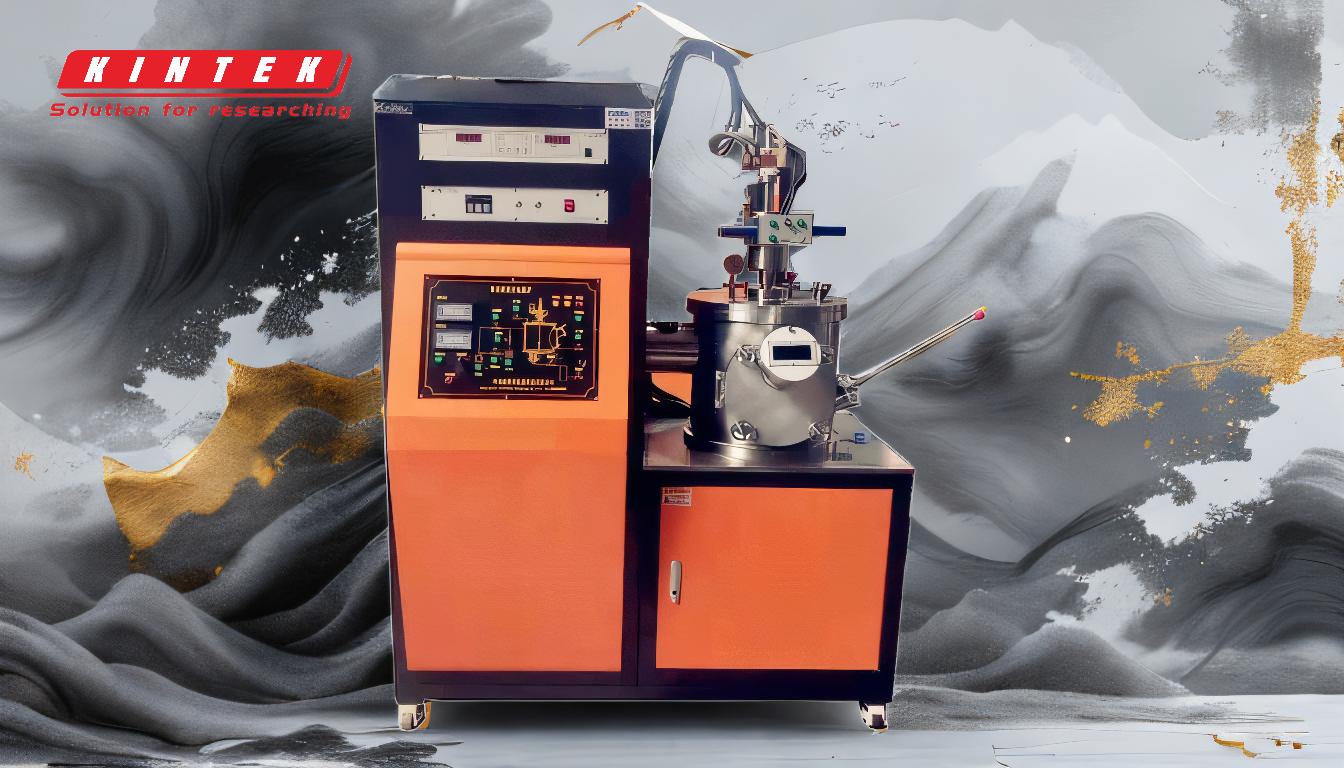
-
Maximum Temperature in Induction Heating:
- Induction heating can achieve temperatures up to 2000°C, as demonstrated by induction melting furnaces. This temperature range is sufficient for melting most metals, including steel, copper, and aluminum.
- The ability to reach such high temperatures is dependent on the inductive coupling between the coil and the material being heated, as well as the power supply's capacity.
-
Factors Influencing Maximum Temperature:
- Material Properties: The material's electrical conductivity and magnetic permeability significantly influence the heating efficiency and maximum temperature. Materials with high conductivity and permeability heat up more efficiently.
- Coil Design: The design of the induction coil, including its geometry and the current density it can handle, plays a critical role in determining the maximum achievable temperature.
- Power Supply: The power output of the induction heating system must be sufficient to generate the required heat. Higher power systems can achieve higher temperatures.
-
Engineering Challenges:
- High-Current Densities: Managing high-current densities in the induction coil is a significant challenge. Specialized engineering and materials, such as high-purity copper, are often required to handle these conditions without overheating or degradation.
- Inductor Design: Custom inductors are often needed for specific applications, which can be expensive and time-consuming to design and manufacture.
-
Applications of High-Temperature Induction Heating:
- Melting: Induction melting furnaces are widely used in foundries to melt metals for casting. The ability to reach temperatures up to 2000°C makes them suitable for melting a wide range of metals.
- Heat Treatment: Induction heating is used for processes like annealing, hardening, and tempering, where precise temperature control is essential.
- Forging: Induction heating is used to heat metals to forging temperatures, allowing for precise control over the heating process.
-
Advantages of Induction Heating:
- Efficiency: Induction heating is highly efficient, as it directly heats the material without significant heat loss to the surrounding environment.
- Precision: The process allows for precise control over the heating temperature and duration, making it ideal for applications requiring strict temperature control.
- Speed: Induction heating can rapidly heat materials to the desired temperature, reducing processing times.
-
Limitations of Induction Heating:
- Cost: The need for custom inductors and specialized engineering can make induction heating systems expensive.
- Material Limitations: Induction heating is most effective with conductive materials. Non-conductive materials, such as plastics, cannot be heated using this method.
In conclusion, induction heating is a versatile and powerful heating method capable of reaching temperatures up to 2000°C, making it suitable for a wide range of industrial applications. However, achieving these high temperatures requires careful consideration of material properties, coil design, and power supply capabilities, as well as overcoming engineering challenges related to high-current densities and inductor design.
Summary Table:
Aspect | Details |
---|---|
Maximum Temperature | Up to 2000°C, suitable for melting, forging, and heat treatment. |
Key Factors | Material properties, coil design, and power supply capabilities. |
Applications | Melting, heat treatment, and forging of metals. |
Advantages | High efficiency, precise control, and rapid heating. |
Limitations | High cost and material limitations (conductive materials only). |
Ready to harness the power of induction heating for your industrial needs? Contact us today to learn more!