The mean free path of sputtering magnetrons refers to the average distance that particles (such as atoms, ions, or electrons) travel between collisions in a sputtering process. This concept is crucial in understanding the efficiency and behavior of sputtering systems, as it influences factors like deposition rates, film quality, and the overall performance of the magnetron. The mean free path depends on the pressure, temperature, and type of gas used in the sputtering chamber. Lower pressures result in longer mean free paths, while higher pressures reduce it due to increased collision frequency. Understanding this parameter helps in optimizing sputtering conditions for specific applications.
Key Points Explained:
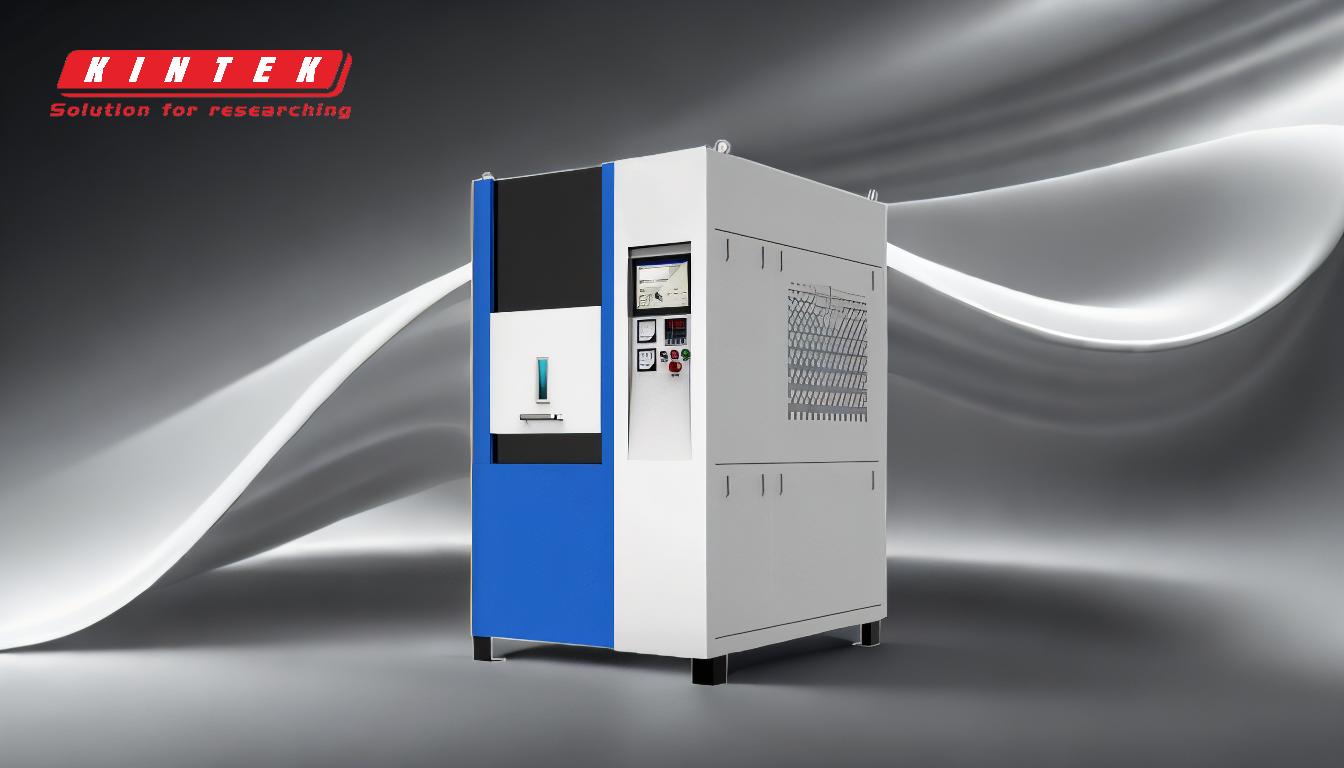
-
Definition of Mean Free Path:
- The mean free path is the average distance a particle travels between successive collisions with other particles in a gas or plasma.
- In sputtering magnetrons, this applies to atoms, ions, or electrons moving through the sputtering gas (e.g., argon).
-
Factors Influencing Mean Free Path:
- Pressure: Lower pressures increase the mean free path because there are fewer gas molecules to collide with. Conversely, higher pressures reduce the mean free path due to more frequent collisions.
- Temperature: Higher temperatures increase the kinetic energy of particles, potentially increasing the mean free path if pressure remains constant.
- Gas Type: The size and mass of gas molecules affect collision frequency. For example, lighter gases like helium have longer mean free paths compared to heavier gases like argon.
-
Relevance to Sputtering Magnetrons:
- The mean free path determines how far sputtered particles travel before colliding with gas molecules or the chamber walls.
- A longer mean free path can lead to higher deposition rates and better film uniformity, as particles are less likely to scatter or lose energy through collisions.
- Conversely, a shorter mean free path may result in more collisions, leading to reduced energy and potential defects in the deposited film.
-
Practical Implications:
- Low-Pressure Sputtering: Operates at pressures around 1–10 mTorr, resulting in longer mean free paths and efficient deposition.
- High-Pressure Sputtering: Used in specific applications but may lead to shorter mean free paths and reduced deposition efficiency.
- Optimization: Adjusting pressure and gas type can help balance mean free path and deposition quality for specific materials and applications.
-
Calculating Mean Free Path:
- The mean free path (λ) can be estimated using the formula:
[
\lambda = \frac{k_B T}{\sqrt{2} \pi d^2 P}
]
where:
- ( k_B ) is the Boltzmann constant,
- ( T ) is the temperature,
- ( d ) is the diameter of the gas molecule,
- ( P ) is the pressure.
- For argon gas at room temperature and 1 mTorr pressure, the mean free path is approximately 6.6 cm.
- The mean free path (λ) can be estimated using the formula:
[
\lambda = \frac{k_B T}{\sqrt{2} \pi d^2 P}
]
where:
-
Applications and Considerations:
- Thin Film Deposition: A longer mean free path is desirable for high-quality, uniform films.
- Reactive Sputtering: The mean free path affects the reaction kinetics between sputtered particles and reactive gases.
- Chamber Design: Understanding the mean free path helps in designing sputtering chambers to minimize collisions and maximize deposition efficiency.
By considering these factors, users can optimize sputtering magnetron systems for specific applications, ensuring efficient and high-quality thin film deposition.
Summary Table:
Key Factor | Impact on Mean Free Path |
---|---|
Pressure | Lower pressure increases mean free path; higher pressure decreases it. |
Temperature | Higher temperature may increase mean free path if pressure remains constant. |
Gas Type | Lighter gases (e.g., helium) have longer mean free paths than heavier gases (e.g., argon). |
Applications | Longer mean free paths improve deposition rates and film uniformity. |
Chamber Design | Understanding mean free path helps optimize chamber design for minimal collisions. |
Optimize your sputtering process today—contact our experts for tailored solutions!