The melting process in an electric arc furnace (EAF) is a highly efficient and controlled method for melting metals, particularly steel scrap, using electric arcs generated between electrodes and the metal charge. The process involves several stages, including charging, meltdown, and refining, and relies on intense heat produced by the electric arc to melt the metal. The furnace operates on a three-phase electric current, and the arc temperature can reach up to 3275°F (1800°C), ensuring rapid melting. Key factors influencing the process include temperature, the presence of impurities, slag formation, and oxidants. The EAF is widely used in steel production due to its ability to recycle scrap metal and its self-contained nature, requiring no secondary heat source.
Key Points Explained:
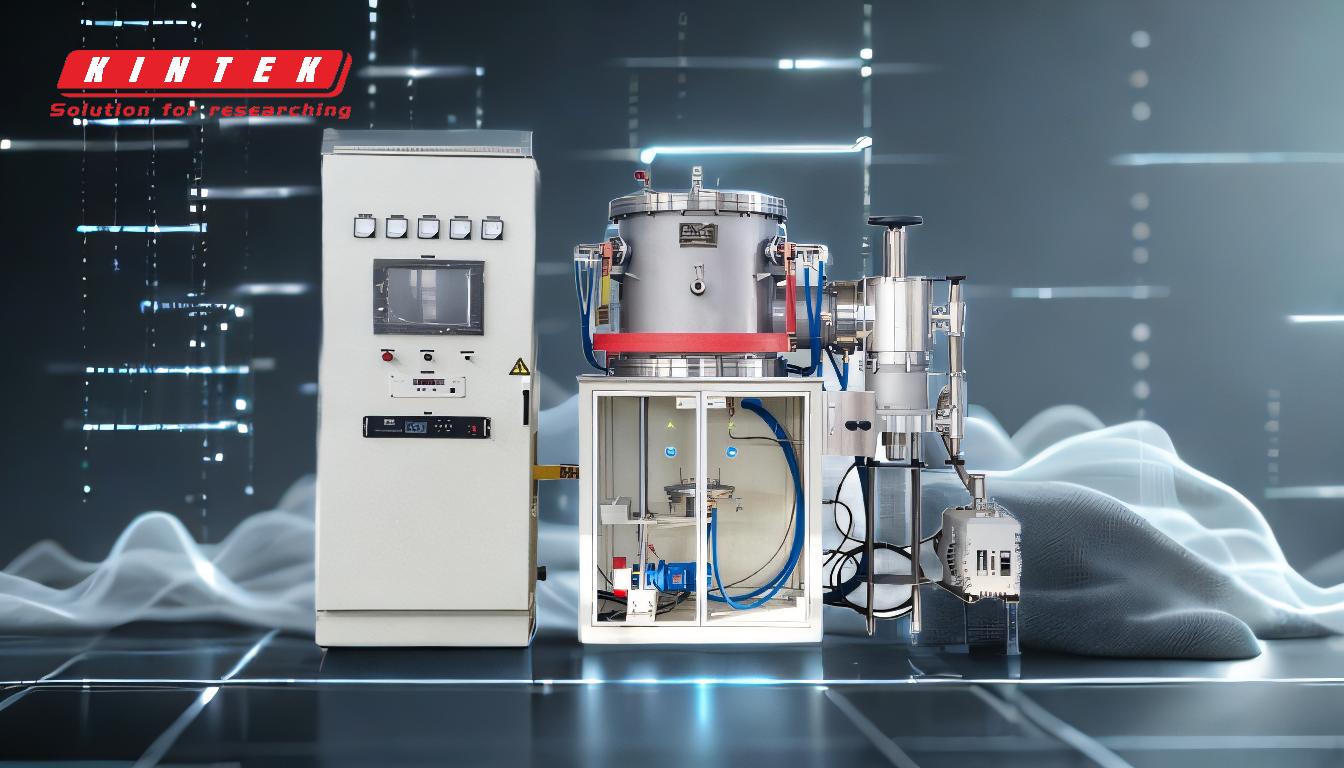
-
Electric Arc Generation and Heat Production:
- The electric arc furnace generates heat through an electric arc formed between graphite electrodes and the metal charge.
- The arc temperature can reach up to 3275°F (1800°C), providing sufficient heat to melt metals rapidly.
- The process is self-contained, meaning it does not require an external heat source, making it energy-efficient.
-
Stages of the Melting Process:
- Charging: Heavy and light scrap metal is loaded into the furnace using a large basket. The scrap is often preheated using exhaust gases to improve energy efficiency.
- Meltdown: The electrodes are lowered onto the scrap, and an electric arc is formed. The voltage is increased to accelerate the melting process. During this stage, carbon, silicon, and manganese in the metal are oxidized.
- Refining: After melting, refining agents such as burnt lime and spar are added to form slag, which helps remove impurities from the molten metal.
-
Role of Slag and Oxidants:
- Slag formation is critical for removing impurities and improving the quality of the molten metal. Burnt lime and spar are added to facilitate slag formation.
- Oxidants are used to accelerate the melting process and improve the efficiency of impurity removal.
-
Energy Consumption and Efficiency:
- The electric arc furnace requires approximately 350 kWh to 370 kWh of energy to melt one ton of scrap metal.
- The use of preheated scrap and exhaust gases enhances the overall energy efficiency of the process.
-
Applications and Advantages:
- EAFs are primarily used for recycling steel scrap and producing carbon and alloy steels.
- The process is environmentally friendly, as it recycles scrap metal and reduces the need for raw materials.
- The ability to control the melting process precisely makes EAFs suitable for producing high-quality steel with specific chemical compositions.
-
Factors Influencing the Melting Process:
- Temperature: The high temperature of the electric arc is crucial for rapid melting.
- Pressure: Although not explicitly mentioned, the furnace operates under controlled atmospheric conditions.
- Impurities and Slag: The presence of impurities affects the quality of the molten metal, and slag formation is essential for impurity removal.
- Oxidants: Oxidants are used to speed up the melting process and improve metal quality.
In summary, the melting process in an electric arc furnace is a sophisticated and efficient method for melting metals, particularly steel scrap. It involves generating intense heat through electric arcs, followed by controlled stages of charging, meltdown, and refining. The process is energy-efficient, environmentally friendly, and capable of producing high-quality steel with precise chemical compositions.
Summary Table:
Key Aspect | Details |
---|---|
Electric Arc Temperature | Up to 3275°F (1800°C) for rapid melting. |
Energy Consumption | 350-370 kWh per ton of scrap metal. |
Stages of Melting Process | Charging, Meltdown, Refining. |
Role of Slag | Removes impurities; formed using burnt lime and spar. |
Applications | Recycling steel scrap, producing carbon/alloy steels. |
Advantages | Energy-efficient, environmentally friendly, precise chemical compositions. |
Discover how an electric arc furnace can optimize your metal recycling process—contact us today!