The melting temperature of ceramics varies widely depending on their composition and type. Traditional ceramics, such as those used in pottery and cookware, typically have lower melting points compared to advanced ceramics, which are engineered for high-performance applications. Advanced ceramics, due to their ionic or covalent bonds, exhibit extremely high melting temperatures, often exceeding 2000°C. These materials are designed to withstand extreme conditions, making them suitable for applications in aerospace, electronics, and industrial machinery. Understanding the specific type of ceramic and its intended use is crucial in determining its melting temperature.
Key Points Explained:
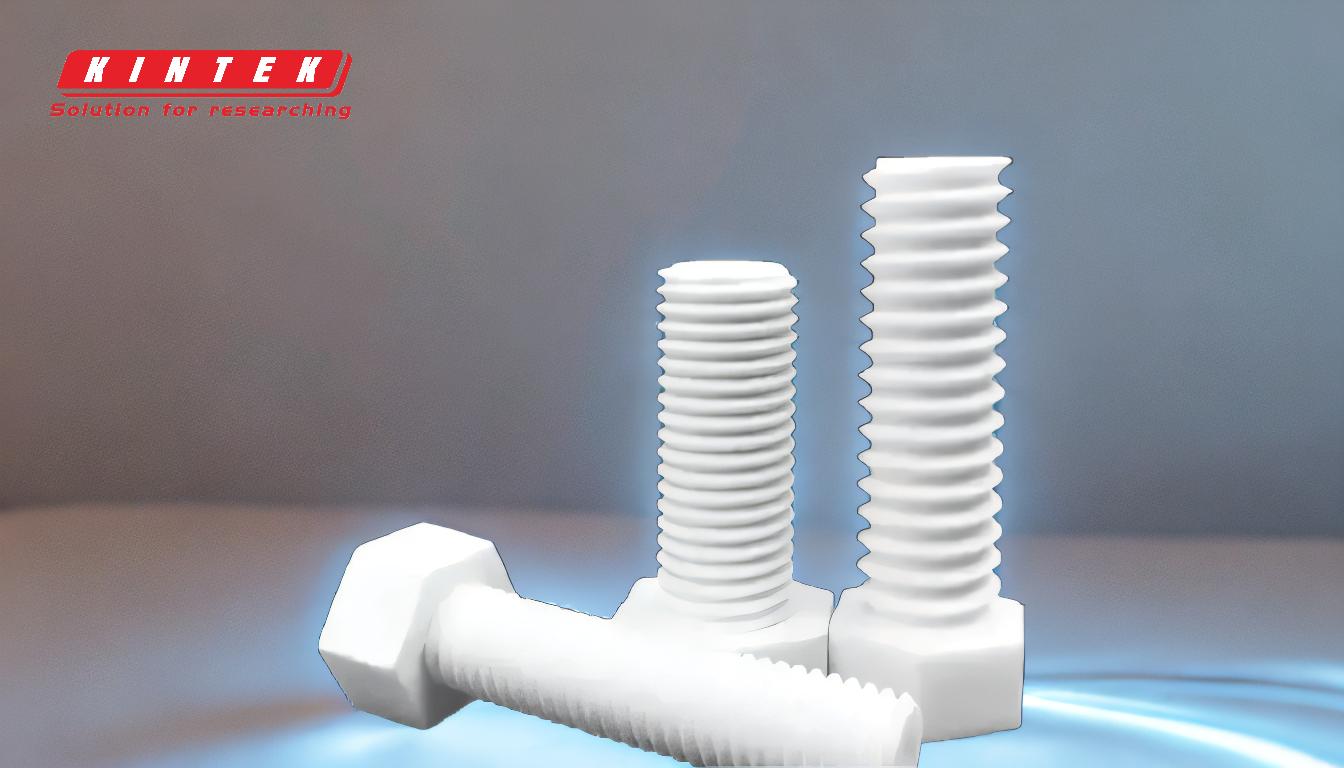
-
Definition and Types of Ceramics:
- Traditional Ceramics: These include materials like clay, porcelain, and earthenware, commonly used in pottery and cookware. They are known for their thermal stability but generally have lower melting points compared to advanced ceramics.
- Advanced Ceramics: These are engineered materials with superior properties, including high melting temperatures. They are used in high-tech applications due to their exceptional strength, hardness, and resistance to extreme conditions.
-
Factors Influencing Melting Temperature:
- Chemical Composition: The specific elements and compounds in the ceramic material significantly affect its melting point. For example, alumina (Al₂O₃) has a melting point of about 2072°C, while zirconia (ZrO₂) melts at approximately 2715°C.
- Bonding Type: Ionic and covalent bonds in ceramics contribute to their high melting temperatures. These bonds are stronger than metallic bonds, requiring more energy to break, thus leading to higher melting points.
-
Melting Temperatures of Common Ceramics:
- Traditional Ceramics: Typically melt between 1000°C and 1400°C. For example, porcelain melts around 1400°C.
- Advanced Ceramics: Have much higher melting points, often exceeding 2000°C. For instance, silicon carbide (SiC) melts at about 2730°C, and boron carbide (B₄C) at approximately 2450°C.
-
Applications and Implications of Melting Temperature:
- Traditional Ceramics: Used in everyday items like dishes and tiles, where moderate thermal resistance is sufficient.
- Advanced Ceramics: Employed in demanding environments such as jet engine components, cutting tools, and semiconductor manufacturing, where high melting temperatures are crucial for performance and durability.
-
Measurement and Testing:
- Thermal Analysis Techniques: Methods like Differential Scanning Calorimetry (DSC) and Thermogravimetric Analysis (TGA) are used to determine the melting temperatures of ceramics accurately.
- Importance in Material Selection: Knowing the melting temperature is vital for selecting the right ceramic material for specific applications, ensuring safety, efficiency, and longevity.
Understanding the melting temperature of ceramics is essential for their application in various industries. By considering the type of ceramic, its composition, and the intended use, one can select the appropriate material that meets the required thermal and mechanical properties.
Summary Table:
Ceramic Type | Examples | Melting Temperature Range | Key Applications |
---|---|---|---|
Traditional Ceramics | Clay, Porcelain | 1000°C - 1400°C | Pottery, Cookware, Tiles |
Advanced Ceramics | Alumina, Silicon Carbide | 2000°C - 2730°C | Aerospace, Electronics, Industrial Machinery |
Need help selecting the right ceramic material for your application? Contact our experts today!