Sintering ceramics is a critical process in the manufacturing of ceramic objects, involving the transformation of powdered materials into a dense, cohesive structure through the application of heat and sometimes additional forces like pressure or electrical currents. The process typically includes several stages: preparation of the powder compact, heating to high temperatures to induce particle bonding and densification, and cooling to solidify the material. This method reduces porosity, causes shrinkage, and enhances the mechanical properties of the ceramic. The sintering process can vary depending on the specific materials and desired outcomes, but it generally involves steps such as pressing, heating, and sometimes post-sintering machining or assembly.
Key Points Explained:
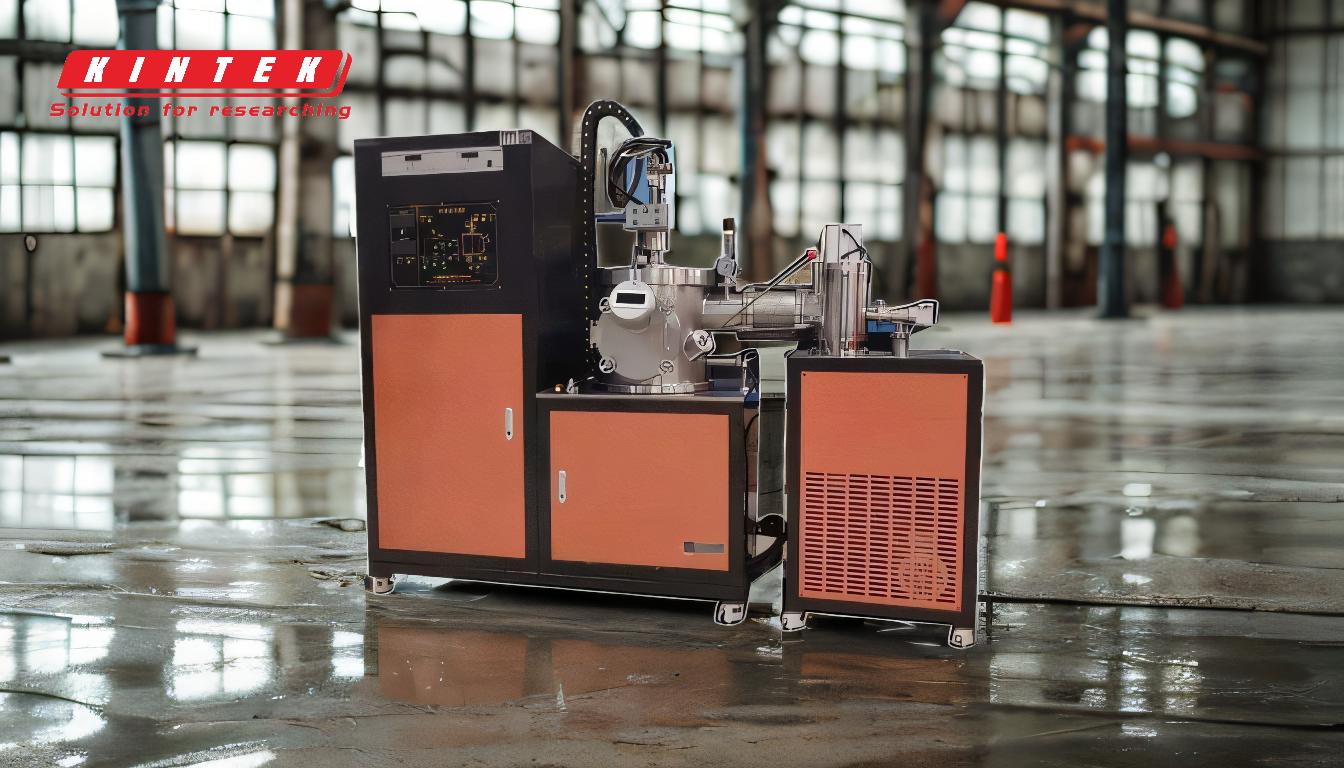
-
Preparation of the Powder Compact:
- Mixing and Composition: The process begins with the preparation of a powder mixture, which includes primary ceramic materials, coupling agents, binders, and deflocculants. This mixture is often combined with water to form a slurry.
- Spray Drying: The slurry is then spray-dried to produce a fine, free-flowing powder that is easier to handle and press.
- Pressing: The powder is compacted into a desired shape using pressing tools or molds. This step forms a "green body," which is a coherent but fragile structure that holds the shape of the final product.
-
Heating and Sintering:
- Binder Removal (Debinding): The green body is heated at a low temperature to burn off any organic binders or coupling agents. This step is crucial to prevent defects during the high-temperature sintering process.
-
High-Temperature Sintering: The green body is then heated to a temperature just below the melting point of the ceramic material. During this stage, several key processes occur:
- Particle Bonding: Powder particles begin to bond at their contact points, leading to the formation of grain boundaries.
- Material Migration: Atoms migrate across the grain boundaries, leading to densification and reduction in porosity.
- Shrinkage: As the particles bond and the material densifies, the ceramic undergoes significant shrinkage, which must be carefully controlled to achieve the desired final dimensions.
- Liquid Phase Sintering (Optional): In some cases, a liquid phase is introduced to accelerate the densification process. This involves adding elements like copper powder or cemented carbides, which melt at the sintering temperature and flow into the remaining pores, further enhancing the material's density.
-
Cooling and Solidification:
- After the sintering process, the ceramic is allowed to cool gradually. This cooling phase is critical to ensure that the material solidifies into a unified mass with the desired mechanical properties, such as strength and hardness.
-
Post-Sintering Processing:
- Machining: Depending on the application, the sintered ceramic part may require additional machining. This is often done using diamond tools or ultrasonic machining to achieve precise dimensions and surface finishes.
- Assembly: In some cases, ceramic parts are metallized and brazed to other components, especially in applications where ceramics are used in conjunction with metals.
-
Control Parameters:
- Temperature and Atmosphere: The sintering process requires precise control of temperature and atmosphere. The temperature must be high enough to induce particle bonding but not so high as to cause melting or excessive grain growth. The atmosphere (e.g., reducing, oxidizing, or inert) is also crucial to prevent unwanted reactions or oxidation.
- Layer Thickness and Speed: For continuous sintering processes, parameters like layer thickness, speed, and sintering endpoint must be carefully controlled to ensure uniform densification and minimize defects.
-
Applications and Outcomes:
- Reduction in Porosity: One of the primary outcomes of sintering is the reduction in material porosity, which enhances the ceramic's mechanical strength and durability.
- Formation of a Porcelain Body: Over time, the ceramic materials gradually become densified and form a porcelain body with a certain strength, suitable for various applications such as pottery, industrial components, and advanced ceramics.
In summary, the sintering of ceramics is a multi-step process that involves careful preparation, controlled heating, and precise post-sintering processing to achieve a dense, strong, and durable ceramic product. The process can be tailored to meet specific requirements by adjusting parameters such as temperature, atmosphere, and the use of additives like binders or liquid phases.
Summary Table:
Stage | Key Steps | Outcome |
---|---|---|
Preparation | Mixing, spray drying, pressing | Formation of a green body with desired shape |
Heating & Sintering | Binder removal, high-temperature sintering, optional liquid phase sintering | Particle bonding, densification, and shrinkage |
Cooling | Gradual cooling | Solidification into a unified mass with enhanced mechanical properties |
Post-Sintering | Machining, assembly | Precise dimensions, surface finishes, and integration with other components |
Control Parameters | Temperature, atmosphere, layer thickness, speed | Uniform densification and minimized defects |
Applications | Pottery, industrial components, advanced ceramics | Strong, durable, and low-porosity ceramic products |
Ready to optimize your ceramic manufacturing process? Contact our experts today for tailored solutions!