Milling is a machining process that involves the removal of material from a workpiece using a rotating cutting tool. The tool, known as a milling cutter, moves in a rotary motion to cut and shape the material. This process is versatile and can be performed using a variety of tools with different diameters and hardness levels. The rotational speed of the milling cutter is crucial to achieving a clean and precise finish on the milled surface or hole. Milling is widely used in manufacturing to create complex shapes, slots, holes, and other features on a workpiece.
Key Points Explained:
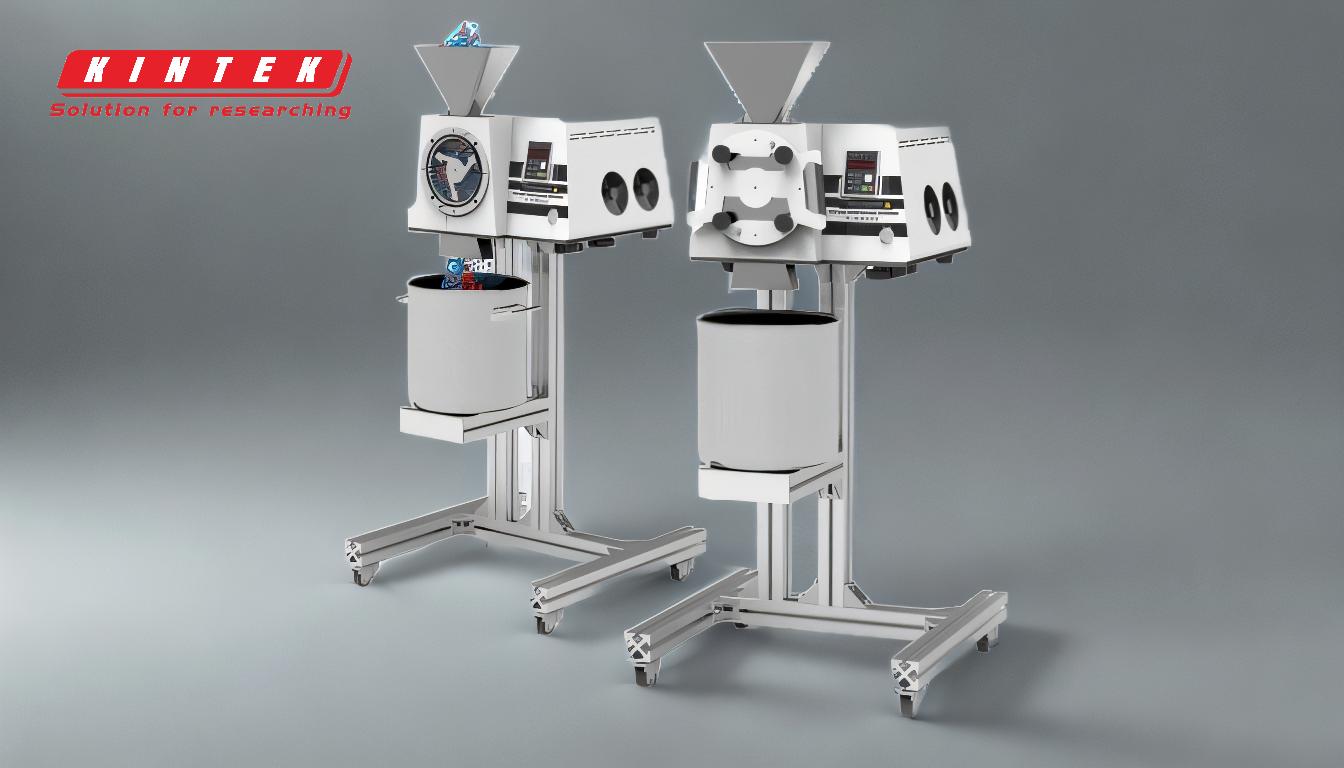
-
Definition of Milling:
- Milling is a machining process where a rotating cutting tool, called a milling cutter, removes material from a workpiece. This process is used to create various shapes, slots, and holes on the workpiece.
-
Rotary Motion of the Milling Tool:
- The milling cutter rotates at high speeds to cut the material. This rotary motion is essential for the cutting action and determines the efficiency and precision of the milling process.
-
Variety of Milling Tools:
- There are numerous types of milling tools available, each designed for specific tasks. These tools vary in diameter, hardness, and geometry, allowing for a wide range of milling operations, from roughing to finishing.
-
Importance of Rotational Speed:
- The rotational speed of the milling cutter is critical for achieving a clean and precise finish. Higher speeds generally result in smoother finishes, but the optimal speed depends on the material being milled and the type of milling operation.
-
Applications of Milling:
- Milling is used in various industries, including automotive, aerospace, and manufacturing, to create complex parts and components. It is capable of producing intricate shapes and features that are difficult to achieve with other machining processes.
-
Advantages of Milling:
- Milling offers several advantages, such as high precision, versatility, and the ability to work with a wide range of materials. It is also capable of producing complex geometries and fine surface finishes.
-
Considerations for Equipment and Consumable Purchasers:
- When purchasing milling equipment and consumables, consider factors such as the type of milling operations you will be performing, the materials you will be working with, and the desired finish quality. Selecting the right tools and equipment, such as a precision cutting machine or laboratory mill equipment, can significantly impact the efficiency and quality of your milling operations.
By understanding these key points, equipment and consumable purchasers can make informed decisions when selecting milling tools and equipment, ensuring optimal performance and results in their machining processes.
Summary Table:
Key Aspect | Details |
---|---|
Definition | A machining process using a rotating cutting tool to remove material. |
Rotary Motion | Essential for cutting; determines efficiency and precision. |
Variety of Tools | Tools vary in diameter, hardness, and geometry for different operations. |
Rotational Speed | Critical for achieving clean, precise finishes; depends on material/task. |
Applications | Used in automotive, aerospace, and manufacturing for complex parts. |
Advantages | High precision, versatility, and ability to work with diverse materials. |
Purchasing Considerations | Consider milling operations, materials, and desired finish quality. |
Need the right milling tools for your project? Contact us today for expert advice!