Muffle furnaces are essential tools in metallurgy and various industrial processes due to their ability to provide precise, high-temperature, and contamination-free heating environments. In metallurgy, they are primarily used for processes such as hardening, annealing, sintering, stress relief, and heat treatment of metals and alloys. Additionally, muffle furnaces are employed for tasks like ashing, calcination, and ignition loss testing, which are critical for material analysis and quality control. Their versatility and ability to handle extreme temperatures make them indispensable in research, manufacturing, and laboratory settings.
Key Points Explained:
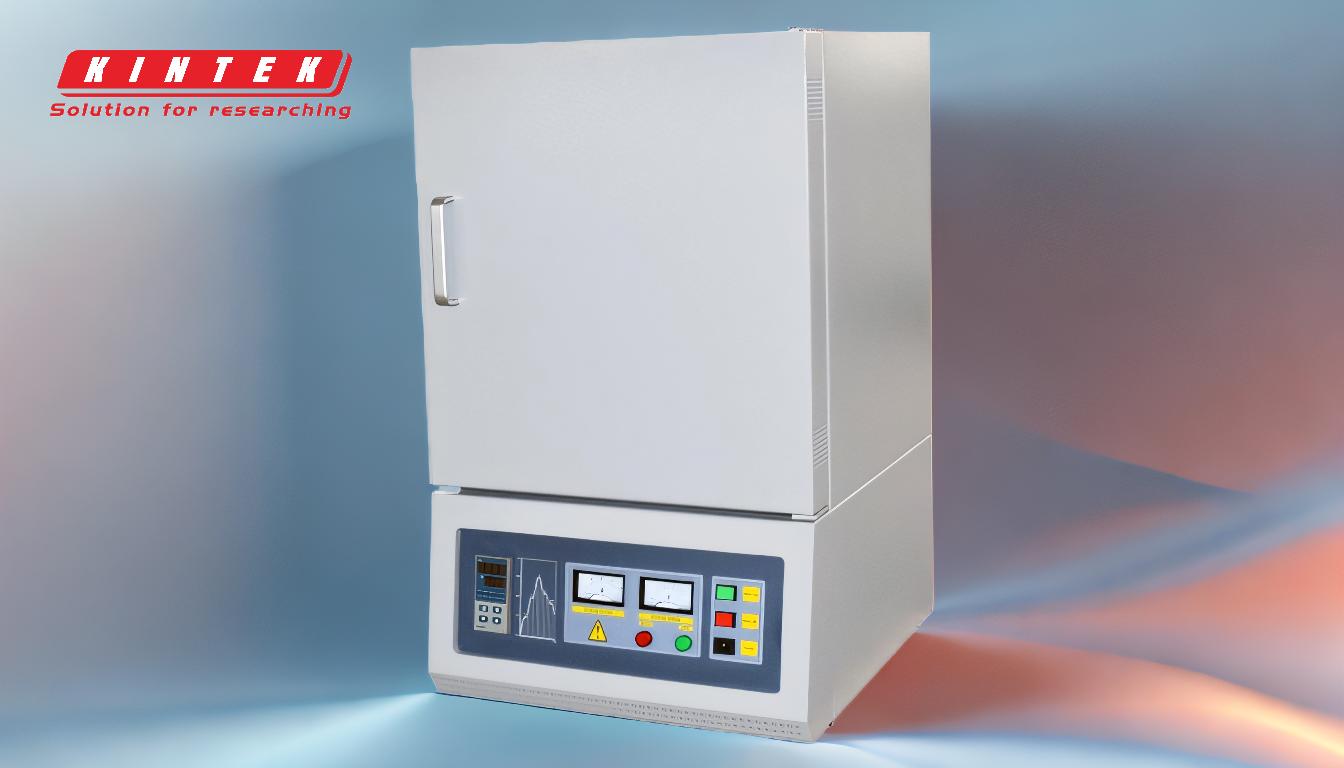
-
Heat Treatment of Metals:
- Hardening: Muffle furnaces are used to heat metals to specific temperatures to increase their hardness and strength. This process involves heating the metal above its critical temperature and then rapidly cooling it (quenching).
- Annealing: This process involves heating metals to a specific temperature and then slowly cooling them to reduce internal stresses, improve ductility, and refine the grain structure. Annealing is crucial for enhancing the workability of metals.
- Stress Relief: Muffle furnaces are used to relieve internal stresses in metals that may have accumulated during manufacturing processes like welding or machining. This helps prevent distortion or cracking in the final product.
-
Sintering:
- Sintering is a process where powdered metals or ceramics are heated to a temperature below their melting point, causing the particles to bond together and form a solid mass. Muffle furnaces provide the controlled environment necessary for this process, which is essential in the production of metal alloys and technical ceramics.
-
Ashing and Calcination:
- Ashing: Muffle furnaces are used to burn off organic materials from a sample, leaving behind inorganic residues. This is particularly important in metallurgy for analyzing the composition of metals and alloys.
- Calcination: This process involves heating materials to high temperatures to drive off volatile components, such as water or carbon dioxide, and to induce thermal decomposition. Calcination is used in the production of metals from their ores.
-
Ignition Loss Testing:
- Ignition loss testing is a method used to determine the amount of volatile or combustible material in a sample. In metallurgy, this is important for assessing the purity of metals and the quality of raw materials used in metal production.
-
Production of Special Alloys:
- Muffle furnaces are used in the production of special alloys, where precise temperature control is required to achieve the desired properties. These alloys are often used in high-performance applications, such as aerospace and automotive industries.
-
Research and Quality Control:
- In research facilities, muffle furnaces are used for various analytical techniques, including thermogravimetric analysis (TGA) and loss on ignition (LOI) analysis. These techniques are crucial for understanding the thermal properties of materials and ensuring the quality of metallurgical products.
-
Versatility Across Industries:
- Beyond metallurgy, muffle furnaces are used in industries such as glass manufacturing (for melting and annealing glass), petrochemical (for analyzing hydrocarbon samples), and semiconductor (for processing materials at high temperatures). This versatility underscores their importance in industrial and laboratory settings.
In summary, muffle furnaces play a critical role in metallurgy by enabling precise heat treatment, sintering, and material analysis. Their ability to provide controlled, high-temperature environments makes them indispensable for enhancing the properties of metals and ensuring the quality of metallurgical products.
Summary Table:
Application | Process | Purpose |
---|---|---|
Heat Treatment | Hardening, Annealing, Stress Relief | Enhances hardness, ductility, and reduces internal stresses in metals |
Sintering | Bonding powdered metals/ceramics below melting point | Produces solid metal alloys and technical ceramics |
Ashing & Calcination | Burning off organic materials, driving off volatile components | Analyzes metal composition and produces metals from ores |
Ignition Loss Testing | Determines volatile/combustible material in samples | Assesses metal purity and raw material quality |
Special Alloys | Precise temperature control for alloy production | Creates high-performance alloys for aerospace and automotive industries |
Research & Quality Control | Thermogravimetric analysis (TGA), loss on ignition (LOI) | Ensures material quality and thermal property understanding |
Versatility | Used in glass, petrochemical, and semiconductor industries | Provides high-temperature processing for diverse industrial applications |
Unlock the full potential of muffle furnaces for your metallurgical needs—contact our experts today!