The optimal sintering temperature depends on the material being processed, the desired properties of the final product, and the specific sintering technique used. Generally, sintering temperatures range from 70% to 90% of the material's melting point. For many materials, this translates to temperatures between 900°C and 1400°C. Key factors influencing the optimal temperature include the material's composition, particle size, and the desired density and mechanical properties of the final product. Additionally, the heating rate, cooling rate, and atmospheric conditions (e.g., air, vacuum, or inert gas) play critical roles in achieving the best results. Below, we explore these factors in detail to determine the optimal sintering temperature for various applications.
Key Points Explained:
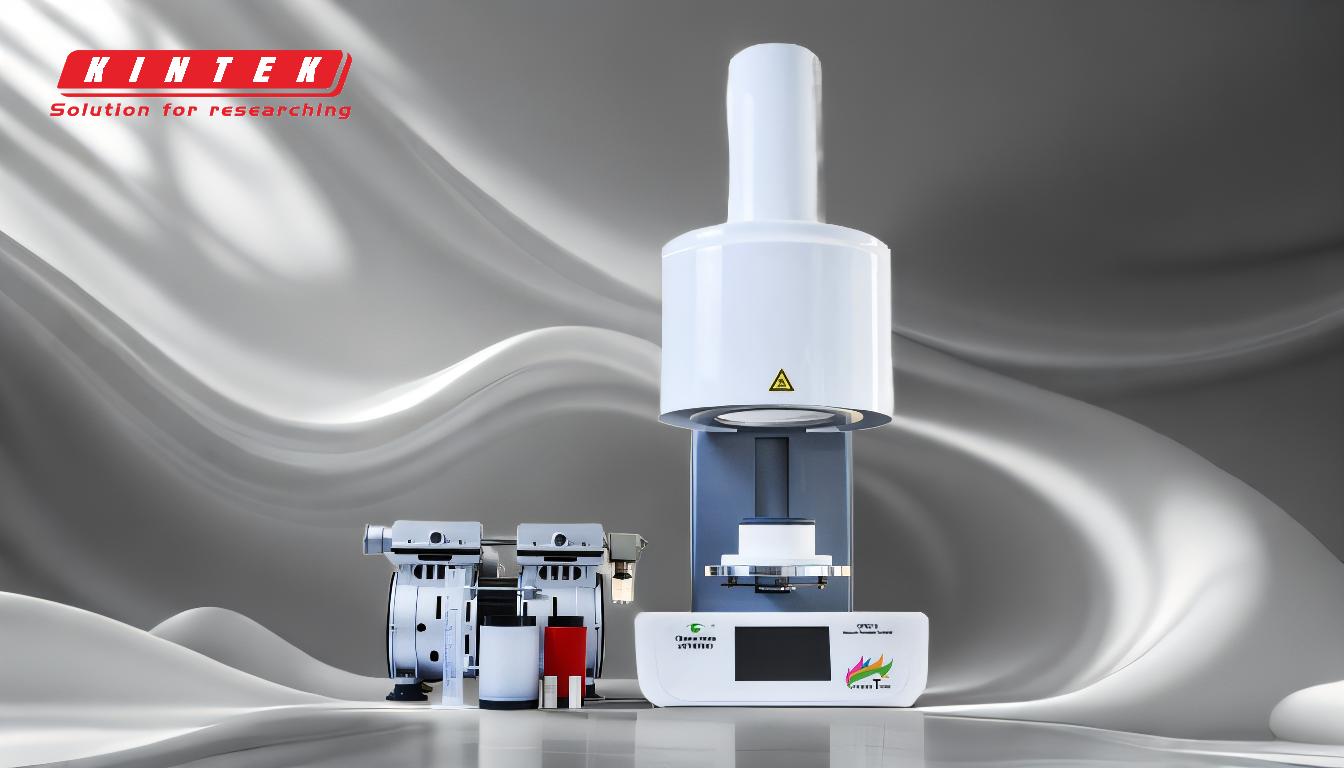
-
Material-Specific Sintering Temperatures:
- The optimal sintering temperature is highly dependent on the material being processed. For example:
- Ceramics: Typically sintered at 1200°C to 1400°C.
- Metals: Often sintered at 70% to 90% of their melting point, which can range from 900°C to 1300°C.
- Polymers: Require lower temperatures, usually below 300°C.
- The choice of temperature ensures proper densification without causing excessive grain growth or material degradation.
- The optimal sintering temperature is highly dependent on the material being processed. For example:
-
Influence of Particle Size:
- Finer powders generally require lower sintering temperatures due to their higher surface energy, which promotes faster densification.
- Larger particles may need higher temperatures to achieve the same level of compaction.
-
Heating and Cooling Rates:
- Heating Rate: A controlled ramp rate from 900°C to the top temperature is critical to avoid thermal shock and ensure uniform densification.
- Cooling Rate: Rapid cooling can lead to residual stresses, while slow cooling promotes equilibrium microstructures. The cooling rate back to 900°C is particularly important for achieving desired mechanical properties.
-
Atmospheric Conditions:
- The sintering atmosphere (e.g., air, vacuum, or inert gases like argon or nitrogen) affects the optimal temperature:
- Vacuum or Inert Gas: Prevents oxidation and allows higher temperatures for better densification.
- Air: May limit the maximum temperature to avoid oxidation or degradation of the material.
- The sintering atmosphere (e.g., air, vacuum, or inert gases like argon or nitrogen) affects the optimal temperature:
-
Desired Product Properties:
- Higher sintering temperatures generally improve tensile strength, bending fatigue strength, and impact energy.
- However, excessive temperatures can lead to grain growth, reduced strength, and dimensional instability.
-
Process Parameters:
- Layer Thickness: Thicker layers (250-500mm) may require higher temperatures to ensure uniform sintering.
- Machine Speed: Controlled at 1.5-4m/min to ensure the sintering feed is burned at the scheduled endpoint.
- Air Volume and Vacuum: Proper airflow (e.g., 3200m³ per ton of sintering ore) and vacuum levels are essential for consistent results.
-
Practical Considerations:
- The sintering furnace type (belt conveyor, push, or batch furnace) and its capabilities influence the achievable temperature range.
- The choice of process depends on balancing the desired product properties with limiting parameters such as equipment constraints and material behavior.
In summary, the optimal sintering temperature is not a fixed value but a carefully chosen parameter that balances material properties, process conditions, and desired outcomes. By considering factors such as material composition, particle size, heating and cooling rates, atmospheric conditions, and process parameters, manufacturers can determine the best temperature for their specific application.
Summary Table:
Factor | Influence on Sintering Temperature |
---|---|
Material | Ceramics: 1200°C–1400°C; Metals: 70%–90% of melting point (900°C–1300°C); Polymers: <300°C. |
Particle Size | Finer powders: Lower temperatures; Larger particles: Higher temperatures. |
Heating/Cooling Rates | Controlled heating avoids thermal shock; Slow cooling promotes equilibrium microstructures. |
Atmosphere | Vacuum/inert gas: Higher temperatures; Air: Limited to avoid oxidation. |
Desired Properties | Higher temps improve strength but risk grain growth; balance is key. |
Process Parameters | Layer thickness, machine speed, airflow, and vacuum levels impact sintering consistency. |
Need help determining the optimal sintering temperature for your materials? Contact our experts today!