Fast pyrolysis is a process that converts biomass into bio-oil, bio-char, and gases by heating it at high temperatures (400–700°C) in the absence of oxygen for very short residence times (less than 2 seconds). The particle size of the feedstock is critical, as most pyrolysis technologies can only process particles up to a maximum of 2 mm to ensure rapid heat transfer. This small particle size is essential for achieving the high heating and heat transfer rates required for fast pyrolysis, which maximizes bio-oil yields (up to 65–80% on a dry feed basis). The process is highly efficient but requires precise control of temperature and residence time to optimize product yields.
Key Points Explained:
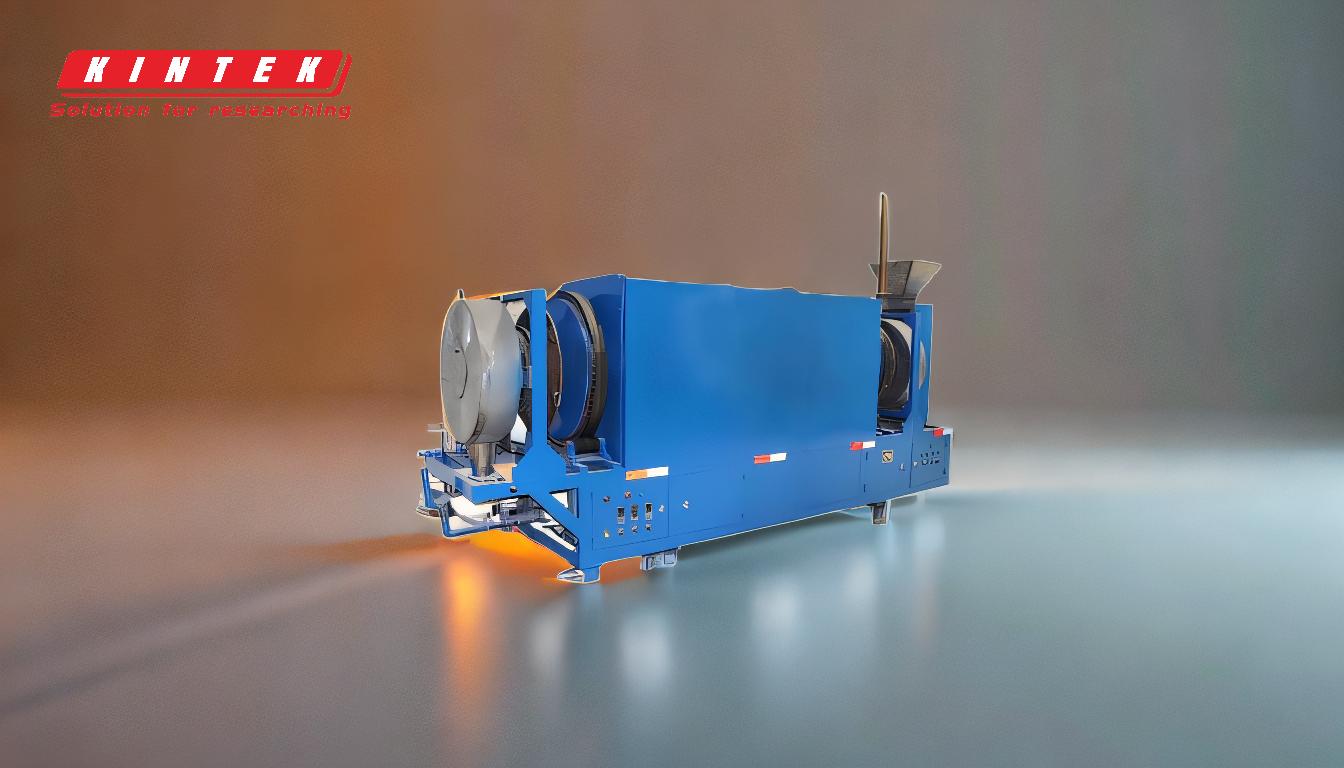
-
Particle Size in Fast Pyrolysis:
- The particle size of the feedstock in fast pyrolysis is typically limited to 2 mm or smaller. This ensures rapid heat transfer through the particles, which is critical for achieving the high heating rates (10–200°C/s) and short residence times (0.5–10 seconds) required for the process.
- Larger particles would hinder heat transfer, leading to incomplete pyrolysis and reduced yields of bio-oil and other products.
-
Importance of Small Particle Size:
- Small particles allow for uniform heating, ensuring that the entire biomass is pyrolyzed efficiently.
- They enable rapid heat transfer, which is necessary to achieve the high heating rates characteristic of fast pyrolysis.
- Small particles also minimize the risk of secondary reactions, which can degrade the quality of the bio-oil.
-
Process Conditions in Fast Pyrolysis:
- Temperature: Fast pyrolysis operates at moderate temperatures (400–700°C). Lower temperatures (up to 650°C) maximize the yield of condensable vapors (bio-oil), while higher temperatures (above 700°C) favor gas production.
- Residence Time: The residence time at pyrolysis temperature is very short, typically less than 2 seconds. This rapid processing prevents the breakdown of bio-oil into gases and char.
- Heating Rates: High heating rates (10–200°C/s) are essential for fast pyrolysis, as they ensure rapid decomposition of biomass into vapors, which are then condensed into bio-oil.
-
Product Yields:
- Fast pyrolysis is optimized for high bio-oil yields, typically ranging from 50–80% on a dry biomass basis.
- The remaining products include bio-char (solid residue) and non-condensable gases (such as methane, hydrogen, and carbon monoxide).
-
Comparison with Other Pyrolysis Methods:
- Slow Pyrolysis: Operates at lower temperatures (<500°C) and slower heating rates (0.1–2°C/s), with longer residence times (hours to days). It primarily produces char and tar, with lower bio-oil yields.
- Ultrafast Pyrolysis: Involves even higher heating rates and shorter residence times than fast pyrolysis, favoring gas production. It is more similar to gasification.
- Flash Pyrolysis: A variant of fast pyrolysis with even higher heating rates, achieving bio-oil yields of up to 75–80 wt%.
-
Applications of Fast Pyrolysis:
- The bio-oil produced can be used as a fuel in boilers, engines, and turbines.
- It can also serve as a source of chemical commodities, though it often requires further refining and upgrading for use as a transportation fuel.
-
Challenges and Considerations:
- The small particle size requirement (≤2 mm) necessitates pre-processing of biomass, such as grinding or milling, which adds to the cost and energy input of the process.
- The bio-oil produced often contains water, acids, and other impurities, requiring post-processing to improve its stability and quality.
In summary, the particle size in fast pyrolysis is a critical factor, with most technologies requiring particles ≤2 mm to ensure efficient heat transfer and high bio-oil yields. The process operates at moderate temperatures (400–700°C) with very short residence times (<2 seconds) and high heating rates (10–200°C/s), making it highly efficient for bio-oil production. However, the need for small particle sizes and the challenges associated with bio-oil quality highlight the importance of optimizing both pre- and post-processing steps in fast pyrolysis.
Summary Table:
Key Aspect | Details |
---|---|
Particle Size | ≤2 mm for rapid heat transfer and uniform heating. |
Temperature Range | 400–700°C; lower temps favor bio-oil, higher temps favor gas production. |
Residence Time | <2 seconds to prevent bio-oil breakdown. |
Heating Rates | 10–200°C/s for rapid biomass decomposition. |
Bio-Oil Yield | 50–80% on a dry biomass basis. |
Other Products | Bio-char and non-condensable gases (e.g., methane, hydrogen, carbon monoxide). |
Applications | Bio-oil used as fuel or chemical feedstock; requires refining for transport. |
Challenges | Pre-processing (grinding) and post-processing (bio-oil stabilization). |
Discover how fast pyrolysis can transform your biomass into valuable products—contact us today for expert guidance!