Brazing paste is a specialized material used in the brazing process, which involves joining two or more metal parts by heating them to a temperature above 450°C (842°F) but below the melting point of the base metals. The paste typically consists of a mixture of metal powders and a flux, which helps to clean the metal surfaces, prevent oxidation, and promote the flow of the filler metal. The choice of brazing paste depends on the specific metals being joined, the desired joint strength, and the operating environment of the final product. Brazing pastes are widely used in industries such as automotive, aerospace, and electronics due to their ability to create strong, durable, and leak-proof joints.
Key Points Explained:
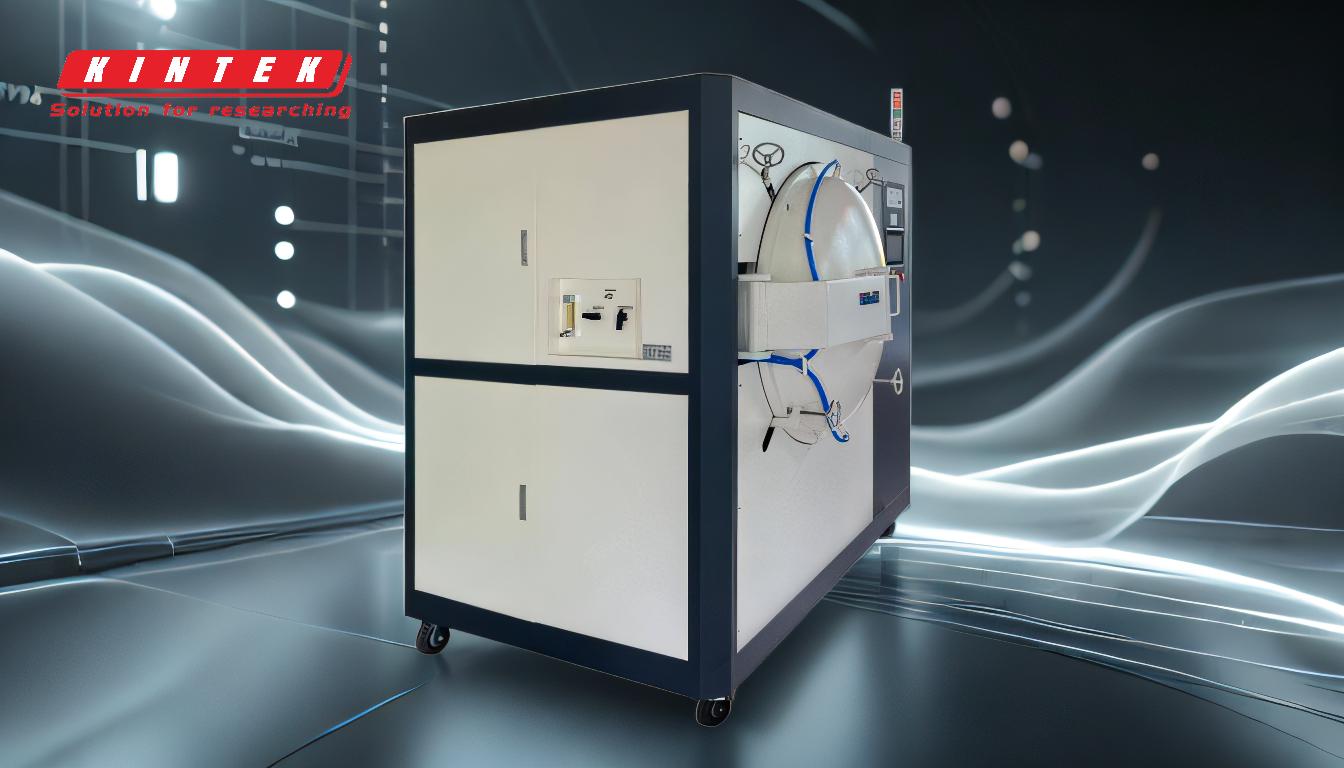
-
Composition of Brazing Paste:
- Brazing paste is primarily composed of two main components: metal powders and flux.
- The metal powders are typically made from alloys such as silver, copper, nickel, or aluminum, depending on the application.
- The flux is a chemical compound that cleans the metal surfaces, removes oxides, and promotes wetting, which ensures the filler metal flows smoothly and bonds effectively.
-
Types of Brazing Pastes:
- Silver-Based Pastes: These are the most common and are used for joining a wide range of metals, including stainless steel, copper, and brass. They offer excellent strength and conductivity.
- Copper-Based Pastes: Often used for high-temperature applications, such as in the automotive and aerospace industries, where joints need to withstand extreme conditions.
- Nickel-Based Pastes: These are used for joining high-strength alloys and are ideal for applications requiring corrosion resistance and high-temperature stability.
- Aluminum-Based Pastes: Suitable for joining aluminum and its alloys, these pastes are commonly used in the electronics and HVAC industries.
-
Functions of Flux in Brazing Paste:
- The flux in brazing paste serves multiple purposes:
- Cleaning: It removes oxides and other impurities from the metal surfaces, ensuring a clean surface for bonding.
- Oxidation Prevention: It forms a protective layer that prevents further oxidation during the heating process.
- Wetting Agent: It lowers the surface tension of the molten filler metal, allowing it to spread evenly and form a strong bond.
- The flux in brazing paste serves multiple purposes:
-
Application of Brazing Paste:
- Brazing paste is applied directly to the joint area using a syringe, brush, or automated dispensing system.
- The paste is then heated using a torch, furnace, or induction heating system until the filler metal melts and flows into the joint.
- After cooling, the flux residue is typically removed to prevent corrosion and ensure a clean finish.
-
Advantages of Using Brazing Paste:
- Ease of Application: The paste form allows for precise application, reducing waste and ensuring consistent joint quality.
- Versatility: Brazing pastes can be used with a wide range of metals and alloys, making them suitable for diverse applications.
- Strong Joints: The use of flux ensures that the joints are free from defects and have excellent mechanical properties.
- Leak-Proof Seals: Brazing pastes are ideal for creating leak-proof joints, which are critical in applications such as refrigeration and plumbing.
-
Considerations When Choosing Brazing Paste:
- Base Metals: The choice of brazing paste depends on the types of metals being joined. For example, silver-based pastes are suitable for copper and brass, while nickel-based pastes are better for high-strength alloys.
- Operating Environment: The paste must be able to withstand the environmental conditions of the final product, such as high temperatures or corrosive environments.
- Joint Strength: The required strength of the joint will influence the choice of filler metal and flux.
- Ease of Cleanup: Some fluxes leave residues that require cleaning, so it's important to consider the post-brazing cleanup process.
-
Common Applications of Brazing Paste:
- Automotive Industry: Used for joining components such as radiators, air conditioning systems, and exhaust systems.
- Aerospace Industry: Essential for creating strong, lightweight joints in aircraft engines and structural components.
- Electronics Industry: Used for bonding components in circuit boards and other electronic devices.
- HVAC Systems: Ideal for joining copper tubing and other components in heating, ventilation, and air conditioning systems.
In summary, brazing paste is a critical material in the brazing process, offering a combination of metal powders and flux to create strong, durable, and leak-proof joints. Its versatility, ease of application, and ability to work with a wide range of metals make it indispensable in industries such as automotive, aerospace, and electronics. When selecting a brazing paste, it's important to consider factors such as the base metals, operating environment, and desired joint strength to ensure optimal performance.
Summary Table:
Aspect | Details |
---|---|
Composition | Metal powders (silver, copper, nickel, aluminum) and flux. |
Types | Silver-based, copper-based, nickel-based, aluminum-based pastes. |
Functions of Flux | Cleans surfaces, prevents oxidation, promotes wetting. |
Application | Applied via syringe, brush, or automated systems; heated to melt filler. |
Advantages | Ease of application, versatility, strong joints, leak-proof seals. |
Key Considerations | Base metals, operating environment, joint strength, cleanup requirements. |
Common Applications | Automotive, aerospace, electronics, HVAC systems. |
Need the right brazing paste for your project? Contact us today for expert advice and solutions!