E-beam evaporation is a physical vapor deposition (PVD) technique used to create thin, high-purity coatings on substrates. The process involves using a high-energy electron beam to heat and evaporate a source material in a vacuum chamber. The evaporated particles then travel upward and deposit onto a substrate, forming a thin film typically ranging from 5 to 250 nanometers in thickness. This method is particularly effective for materials with high melting points, such as gold, and ensures high-purity coatings with excellent adhesion to the substrate. The vacuum environment minimizes contamination, and the process does not alter the substrate's dimensional accuracy.
Key Points Explained:
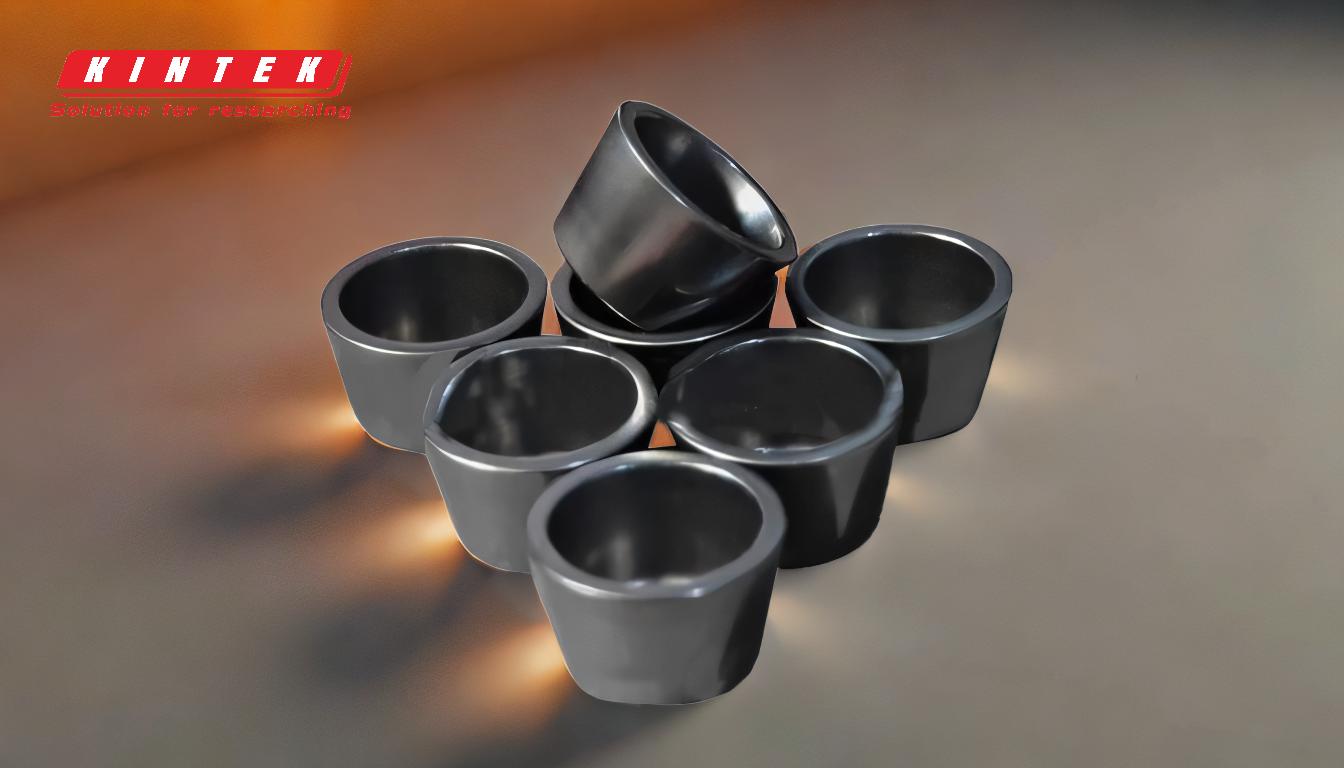
-
Principle of E-Beam Evaporation:
- E-beam evaporation is a type of physical vapor deposition (PVD) where a high-energy electron beam is used to vaporize a source material.
- The electron beam delivers intense heat directly to the material, causing it to melt and evaporate.
- The vaporized material then travels through the vacuum chamber and deposits onto a substrate, forming a thin film.
-
Role of the Vacuum Chamber:
- The process takes place in a vacuum chamber to minimize contamination and ensure high-purity coatings.
- The vacuum environment reduces the presence of impurities and unwanted chemical reactions, which could degrade the quality of the deposited film.
-
Electron Beam Generation and Control:
- The electron beam is generated using an electron gun, which directs high-energy electrons onto the source material.
- The beam can be precisely controlled to focus on specific areas of the source material, allowing for efficient and localized heating.
- This control is crucial for materials with high melting points, as it ensures that the material is heated sufficiently to evaporate without causing damage to the crucible or surrounding components.
-
Source Material and Crucible:
- The source material is typically placed in a crucible or a water-cooled copper hearth.
- The crucible is designed to withstand high temperatures and is often cooled using a water cooling circuit to prevent it from melting or contaminating the material.
- The choice of crucible material and cooling method is critical to maintaining the purity of the deposited film.
-
Deposition onto the Substrate:
- The evaporated particles travel upward in the vacuum chamber and deposit onto the substrate, which is positioned above the source material.
- The substrate is carefully prepared and positioned to ensure uniform deposition of the thin film.
- The resulting film is typically very thin, ranging from 5 to 250 nanometers, and exhibits high purity and excellent adhesion to the substrate.
-
Advantages of E-Beam Evaporation:
- High Purity: The vacuum environment and precise control of the electron beam result in films with minimal impurities.
- High Melting Point Materials: E-beam evaporation is particularly effective for materials with high melting points, such as gold, which are difficult to evaporate using other methods.
- Thin Film Uniformity: The process allows for the deposition of very thin, uniform films, which are essential for applications in electronics, optics, and other high-tech industries.
- Dimensional Accuracy: The process does not alter the dimensional accuracy of the substrate, making it suitable for precision applications.
-
Applications of E-Beam Evaporation:
- Semiconductor Manufacturing: E-beam evaporation is widely used in the semiconductor industry to deposit thin films of metals and alloys on silicon wafers.
- Optical Coatings: The technique is used to create high-quality optical coatings for lenses, mirrors, and other optical components.
- Decorative Coatings: E-beam evaporation is also used to apply decorative coatings on various materials, including jewelry and consumer electronics.
- Research and Development: The process is employed in research labs to develop new materials and coatings with specific properties.
-
Challenges and Considerations:
- Cost: E-beam evaporation equipment can be expensive, and the process requires a high level of expertise to operate effectively.
- Material Limitations: While the process is suitable for many materials, some materials may not be compatible with e-beam evaporation due to their properties or the risk of contamination.
- Process Control: Achieving consistent results requires precise control over the electron beam, vacuum conditions, and substrate preparation.
In summary, e-beam evaporation is a highly effective method for depositing thin, high-purity films on substrates, particularly for materials with high melting points. The process involves generating a high-energy electron beam to vaporize a source material in a vacuum chamber, with the vaporized material then depositing onto a substrate. The resulting films are uniform, pure, and adhere well to the substrate, making e-beam evaporation a valuable technique in various industries, including semiconductor manufacturing, optics, and decorative coatings. However, the process requires careful control and expertise to achieve optimal results.
Summary Table:
Aspect | Details |
---|---|
Process | Uses high-energy electron beams to vaporize materials in a vacuum chamber. |
Film Thickness | Typically ranges from 5 to 250 nanometers. |
Key Advantages | High purity, excellent adhesion, and dimensional accuracy. |
Applications | Semiconductor manufacturing, optical coatings, decorative coatings. |
Challenges | High equipment cost, material limitations, and precise process control. |
Ready to explore e-beam evaporation for your projects? Contact our experts today to get started!