The power factor of a core-type induction furnace is typically high, often close to unity (1.0), due to its design and operational principles. This is because the furnace operates similarly to a transformer, where the primary coil induces a current in a secondary loop of molten metal, resulting in efficient energy transfer with minimal reactive power. The high power factor is a significant advantage, contributing to the furnace's overall efficiency of up to 98%. This makes core-type induction furnaces ideal for high-throughput operations with minimal energy losses.
Key Points Explained:
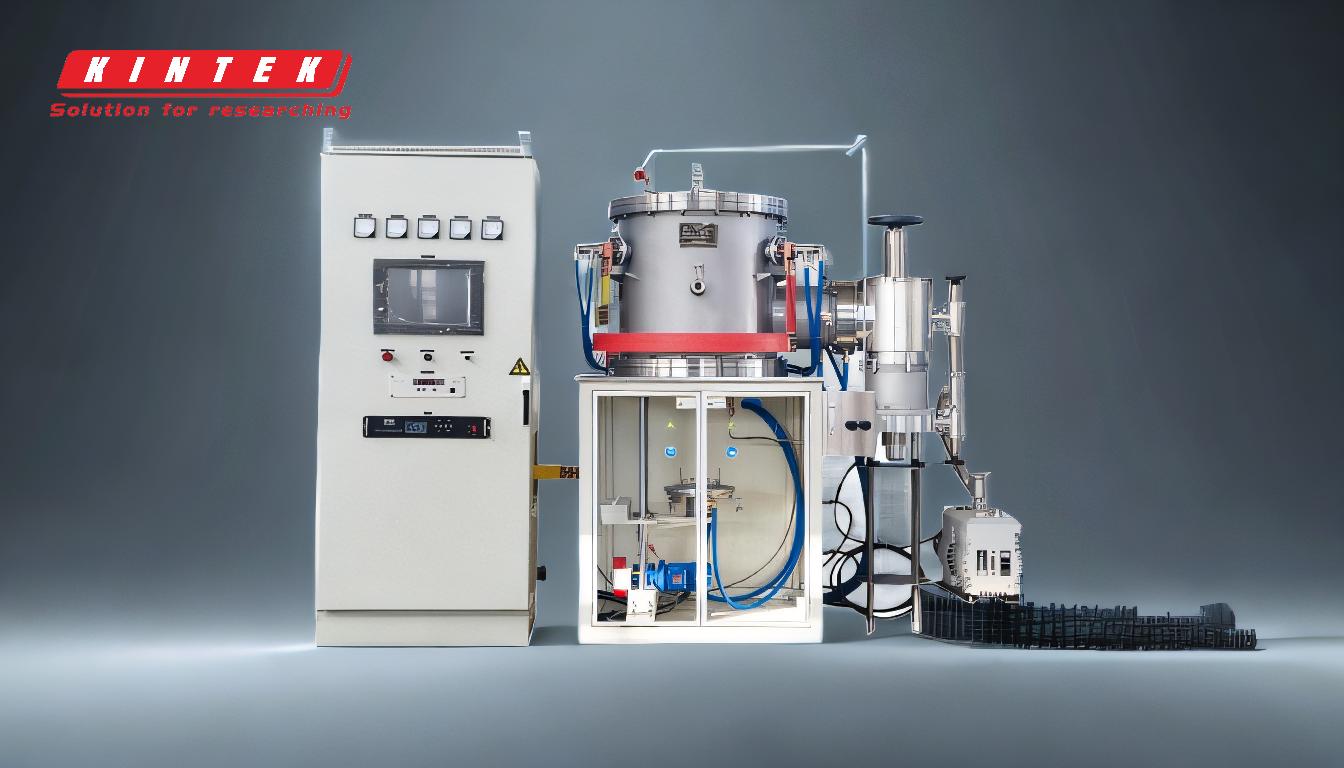
-
Transformer Principle in Core-Type Induction Furnaces:
- Core-type induction furnaces operate on the transformer principle, where an alternating current flows through a primary coil surrounding an iron core.
- This induces a larger current in a secondary loop formed by molten metal, generating heat via the Joule Effect.
- The transformer-like operation ensures efficient energy transfer, contributing to a high power factor.
-
High Power Factor:
- The power factor of core-type induction furnaces is typically close to unity (1.0), indicating minimal reactive power and efficient energy usage.
- This high power factor is a result of the furnace's design, which minimizes energy losses and maximizes the conversion of electrical energy into heat.
-
Efficiency and Energy Savings:
- Core-type induction furnaces achieve up to 98% power efficiency, making them highly efficient for industrial applications.
- The high power factor plays a crucial role in this efficiency, as it reduces the amount of reactive power that would otherwise be wasted.
-
Comparison with Coreless Induction Furnaces:
- Coreless induction furnaces, while versatile, have a lower power efficiency (approximately 75%) and a lower power factor compared to core-type furnaces.
- The core-type design's ability to maintain a high power factor makes it more suitable for continuous, high-throughput operations.
-
Operational Advantages:
- The high power factor and efficiency of core-type induction furnaces make them ideal for operations requiring consistent performance and minimal downtime.
- These furnaces are particularly well-suited for applications with few alloy changes, as they are designed for continuous operation and require minimal cooling.
-
Design Features Contributing to High Power Factor:
- The primary and secondary coil arrangement in core-type furnaces ensures a balanced load, which helps maintain a high power factor.
- The use of an iron core in the design further enhances the magnetic coupling between the primary and secondary coils, improving energy transfer efficiency.
-
Industrial Applications:
- Core-type induction furnaces are commonly used in industries requiring high production rates and consistent quality, such as steel manufacturing and metal casting.
- The high power factor and efficiency make them a cost-effective choice for large-scale operations.
In summary, the power factor of a core-type induction furnace is typically close to unity, thanks to its transformer-like operation and efficient design. This high power factor contributes to the furnace's overall efficiency of up to 98%, making it a preferred choice for high-throughput industrial applications.
Summary Table:
Key Feature | Description |
---|---|
Power Factor | Close to unity (1.0), indicating minimal reactive power and efficient energy use. |
Efficiency | Up to 98%, making it highly efficient for industrial operations. |
Transformer Principle | Operates like a transformer, ensuring efficient energy transfer. |
Design Features | Primary and secondary coil arrangement with an iron core for balanced load. |
Applications | Ideal for steel manufacturing, metal casting, and high-throughput operations. |
Maximize your industrial efficiency with a core-type induction furnace—contact us today to learn more!